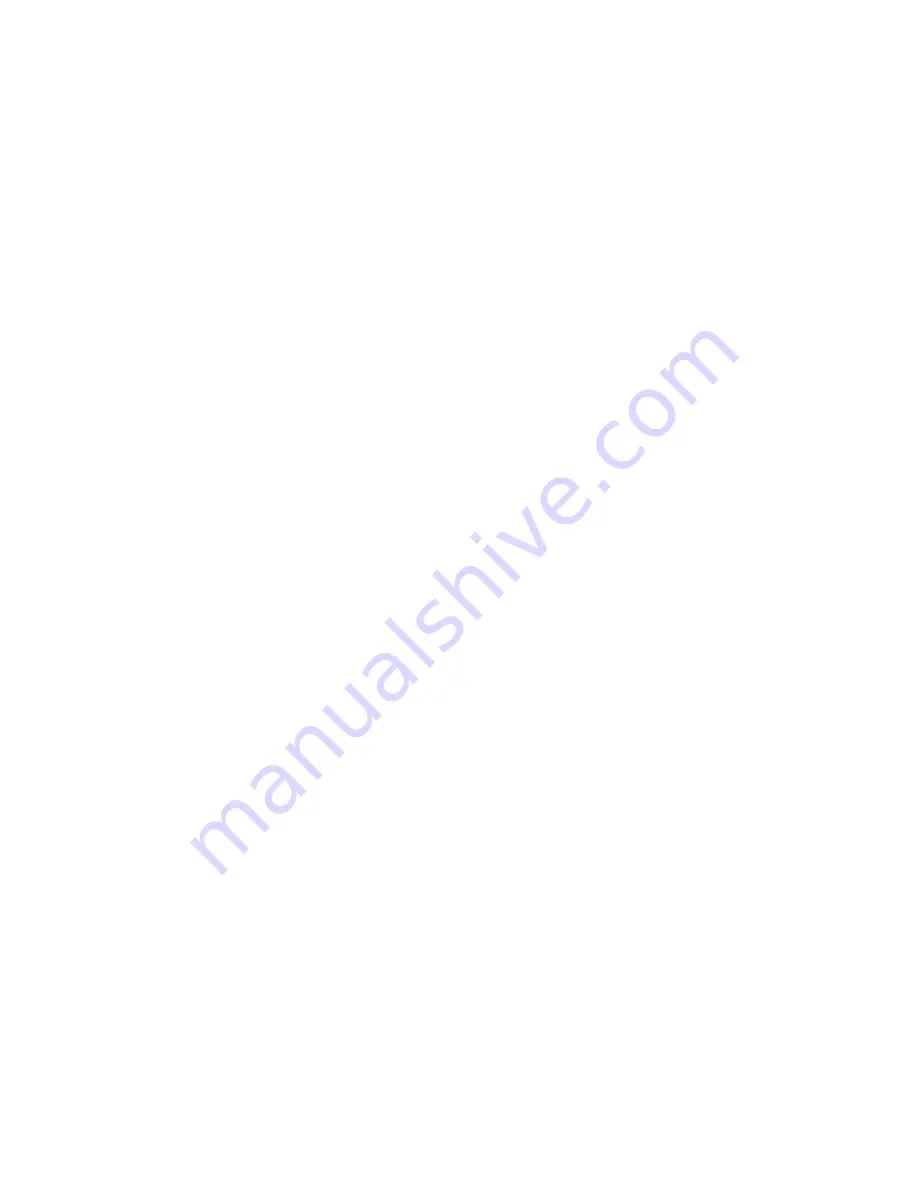
1 Description
1.1 Design
and
function
The SOGEVAC SV300 B are single- stage, oil-sealed rotary vane pumps. The anti-
suckback valve, gas ballast valve (optional), exhaust filter, oil return circuit and
oil cooling oil are integrated functional elements. The pumps are driven by a
directly flanged motor.
The rotor mounted eccentrically in the pump cylinder has three vanes which
divide the pump chamber into several compartments. The volume of each chan-
ges periodically with the rotation of the rotor.
As the rotor rotates, the intake portion of the pumping chamber expands and
sucks gas through the intake port. The gas passes through the dirt trap and the
open anti-suckback valve and enters the pump chamber. As the rotor rotates
further, the vane separates part of the pump chamber from the intake port.
This part of the pump chamber is reduced, and the gas is compressed. At slight-
ly above atmospheric pressure the gas is expelled from the chamber via the
exhaust valve.
Oil injected into the pump chamber serves to seal, lubricate and cool the pump.
The oil entrained with the compressed gas is coarsely trapped in the oil case by
deflection. Then fine filtering occurs in the exhaust filter elements. The propor-
tion of oil in the exhaust gas is thus reduced below the visibility threshold (over
99 % entrapment rate).
Oil trapped in the exhaust filters is returned to the inlet chamber via an oil
return transfer. To prevent gas flowing at atmospheric pressure from the oil
reservoir into the intake port, the oil return line is controlled by a float valve.
The oil cycle is maintained by the pressure difference existing between the oil
case (pressure above or equal to atmospheric pressure) and the intake port
(pressure below atmospheric pressure).The ball bearings are greased for 30 000
hours.
A fan running on the pump shaft generates the necessary cooling air. The oil
cools down through a radiator.
Water cooled pumps with en oil-water heat exchanger and thermostatic valve
are also available (as specific variants).
By opening the gas ballast valve, a controlled amount of air so called «gas
ballast» is admitted into the pump chamber. This gas ballast prevents conden-
sation (up to the limit of water vapor tolerance specified in the Technical Data)
when pumping condensable gases or vapors.
There are different types of gas ballast :
- small gas ballast ( 4 m
3
/h)
- standard gas ballast ( 7.5 m
3
/h)
- large gas ballast ( 15 m
3
/h)
- gas ballast with electromagnetical valve ( 10 m
3
/h) - See § 2.5.2
On pumps supplied without gas ballast valve, the valve can be retrofitted. The
gas ballast flows are indicative and valid at ultimate pressure.
Description
4
GA02330_002_06 - 01/2010 - © Oerlikon Leybold Vacuum