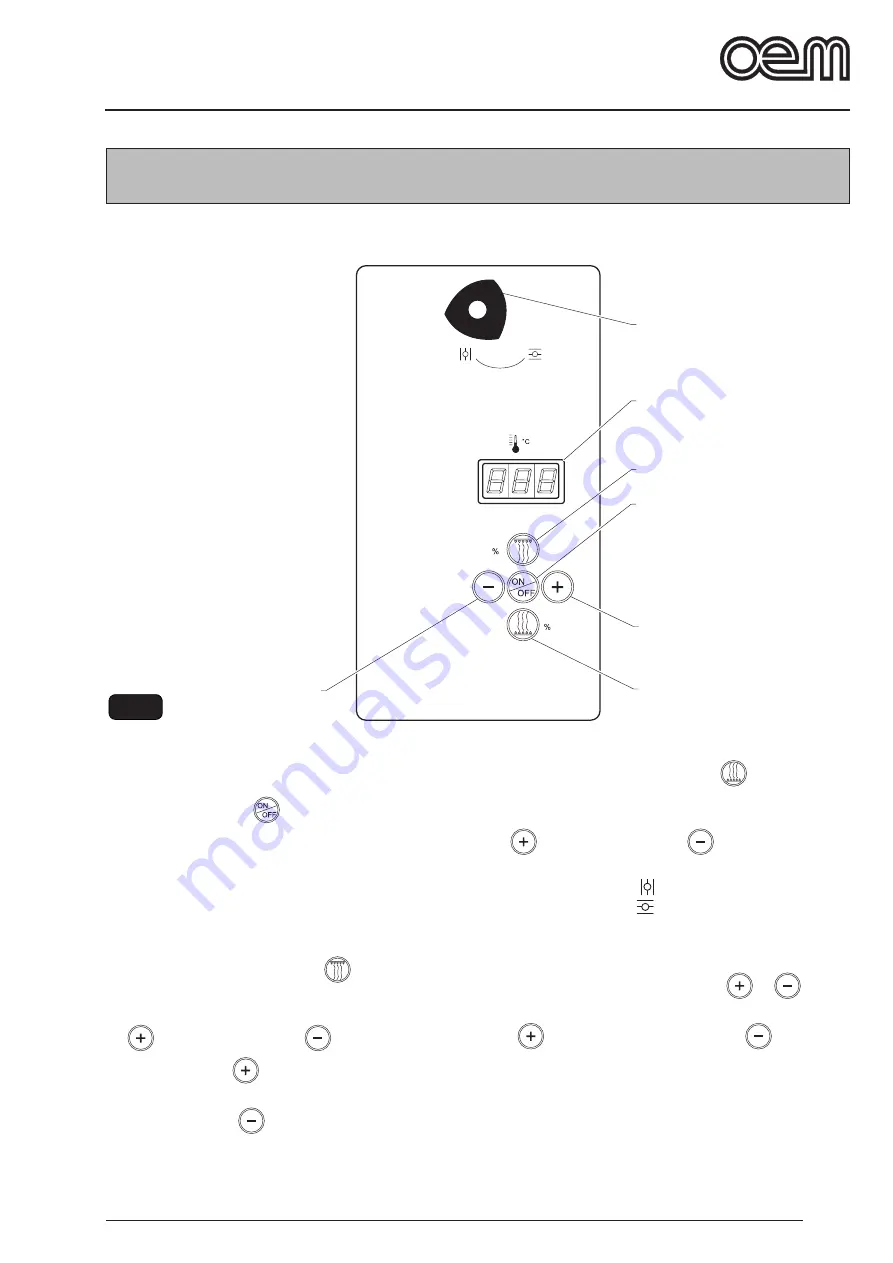
MILLENNIUM MM/MB
Functioning
GB - 17
Capitolo 5
2
3
1
6
4
7
5
FIG. 1
5.1 - CONTROL BOARD AND PILOT LIGHTS ON DIGITALLY CONTROLLED OVENS (Fig 1)
On the oven, there are the following control elements:
1. Line key ON/OFF
Pressing it, the display (2) lights up, the lamp inside
the chamber lights up and the control elements are
energized.
2. Display
The set and real temperature as well as the ceiling
and bedplate resistance functioning percentage are
displayed.
3. Ceiling resistance capacity
Pressing it, the connection percentage value of the
upper resistances is displayed; to increase it press
(4), to reduce it press
(5).
4. Increment key
To increase the values to be set.
5. Decrement key
To reduce the values to be set.
6. Bedplate resistance capacity
Pressing it, the connection percentage value of the
lower resistances is displayed; to increase it press
(4), to reduce it press
(5).
7. Handwheel opening/closing
By turning towards
, the chimney damper opens;
by turning towards
, the chimney damper closes.
Temperature setting
On the display (2) the real oven temperature is displayed,
to modify the set temperature press
or
, on the
display the set temperature is displayed, then press the
key
within 5 seconds to raise or
reduce the
temperature. After approximately 10 seconds from the
temperature setting, a temperature self-entering occurs
and the real oven temperature is displayed.
Summary of Contents for MILLENNIUM 1235/E
Page 1: ...Installation and Operation Manual PIZZA OVEN MILLENNIUM ...
Page 2: ......
Page 4: ......
Page 15: ......
Page 38: ......