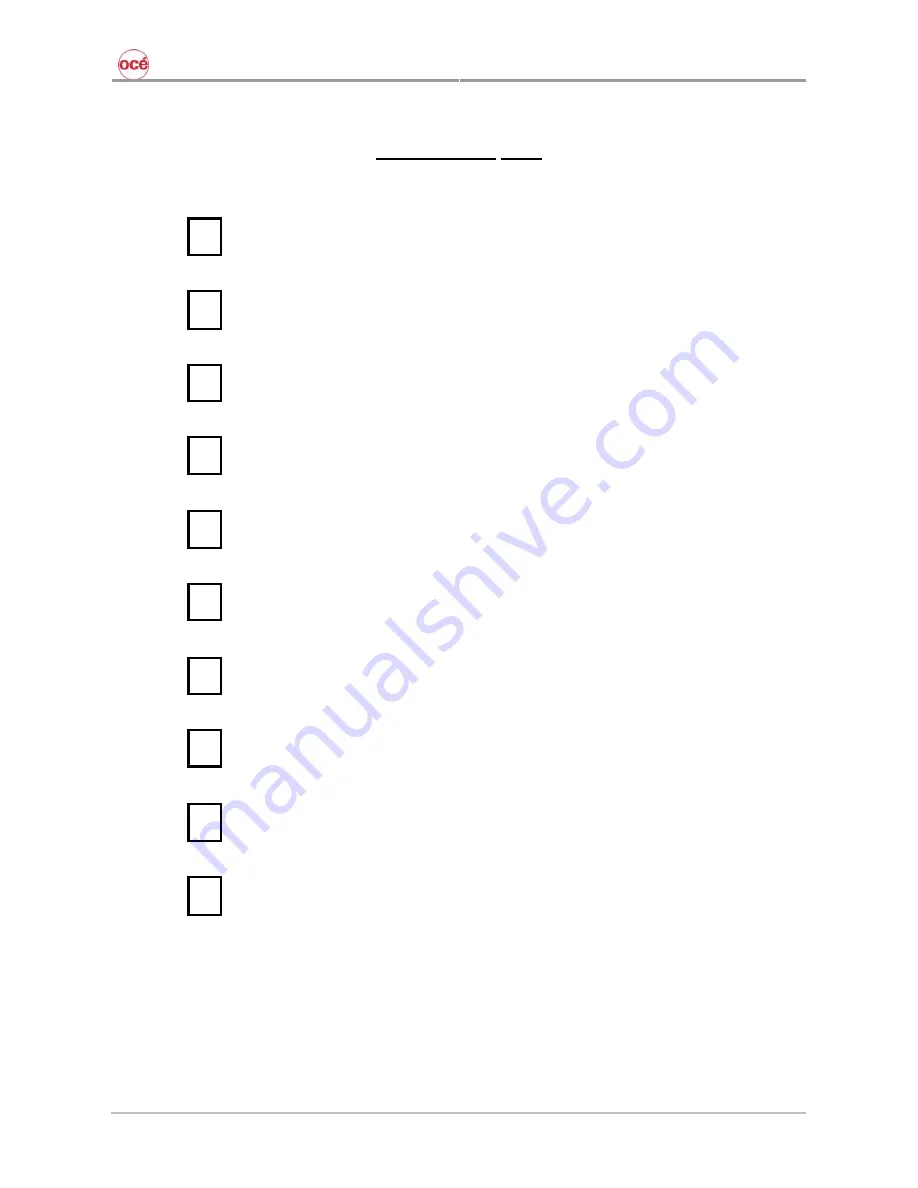
CS9200 Low Solvent series printers
6
AP-40301 – Rev. 2.0 – 02/05/2008
Step-by-step plan
1.
Check installation environment
►
Refer to chapter 1
2.
Unpack the printer, stand and boxes
►
Refer to chapter 3
3.
Check in-the-box configuration
►
Refer to chapter 2
4.
Assemble the printer / winder
►
Refer to chapter 4
5.
Connect the cables
►
Refer to chapter 5
6.
Load ink
►
Refer to chapter 6
7.
Load media
►
Refer to chapter 7
8.
Verify head adjustment
►
Refer to chapter 8
9.
Make Test Print
►
Refer to chapter 9
10.
Get to know the periodical maintenance
►
Refer to chapter 10
Summary of Contents for CS9265
Page 1: ...Oc CS9265 Oc CS9290 Installation Guide Low Solvent...
Page 2: ...CS9200 Low Solvent series printers 2 AP 40301 Rev 2 0 02 05 2008...
Page 4: ...CS9200 Low Solvent series printers 4 AP 40301 Rev 2 0 02 05 2008...
Page 8: ...CS9200 Low Solvent series printers 8 AP 40301 Rev 2 0 02 05 2008...
Page 12: ...CS9200 Low Solvent series printers 12 AP 40301 Rev 2 0 02 05 2008...
Page 20: ...CS9200 Low Solvent series printers 20 AP 40301 Rev 2 0 02 05 2008...
Page 40: ...CS9200 Low Solvent series printers 40 AP 40301 Rev 2 0 02 05 2008...
Page 46: ...CS9200 Low Solvent series printers 46 AP 40301 Rev 2 0 02 05 2008...