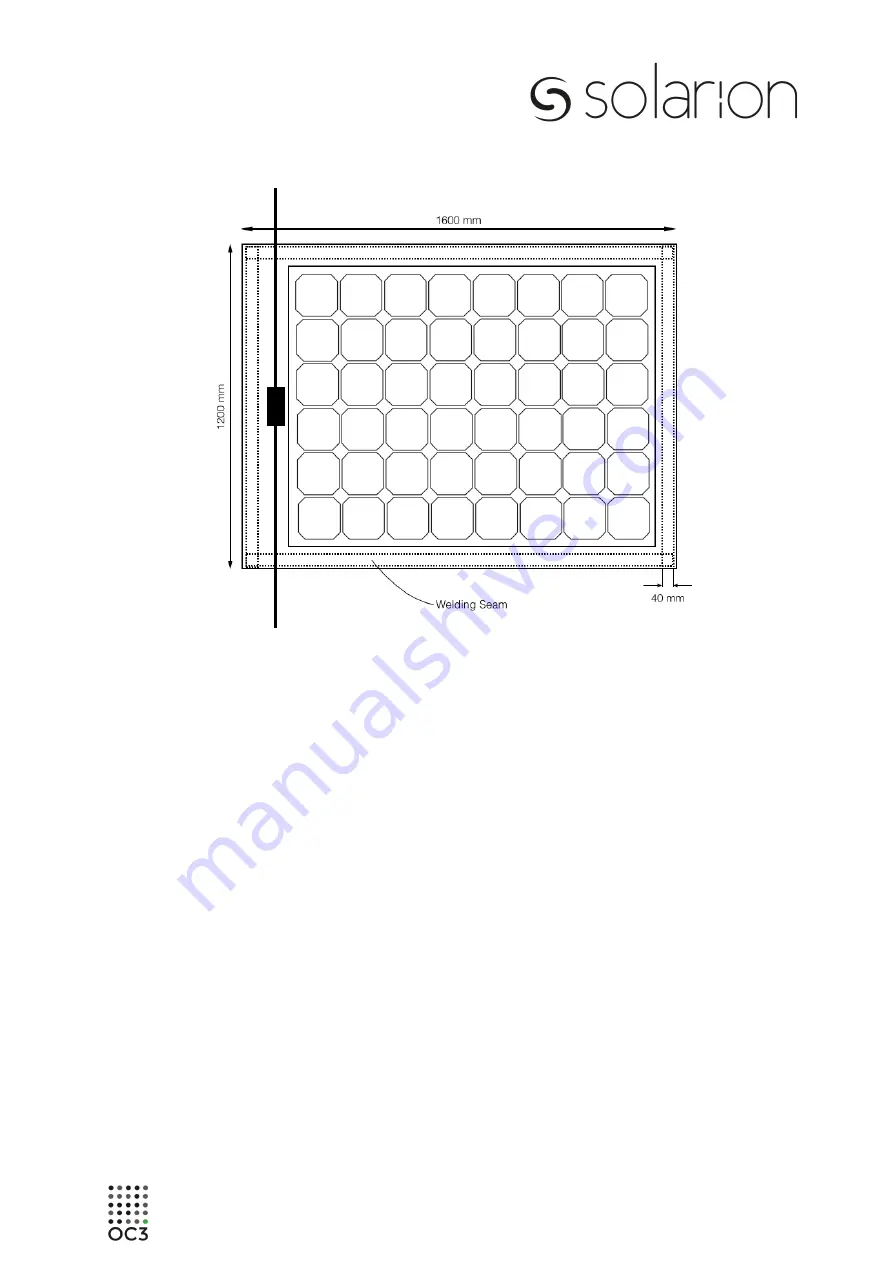
Solarion
M210P
KEE EN V1.0 2015-10-20 © OC3 AG
Figure 2: Allowable welding areas for mechanical fastening, valid for loads up to 2.4 kPa
The module weldings must be done by hot air welding along the long and short sides of the module. Welding seams should be done
inside of the dotted rectangles.
The edges of the membranes to be welded must be clean and dry. Minimum air temperature at the building site should be 10 °C.
The welding with a 40 mm nozzle has to be done stepwise.
-
Step 1. Spot welding: Weld the overlapping seam welding about every 40 cm at a distance of 6 cm from the edge.
-
Step 2. Pre-welding: Weld the rear overlap area so that a 4 cm wide area remains for the finishing weld.
-
Step 3. Welding: Weld the remaining stripe of 4 cm.
Welding temperature
for PVC is 550 °C
with a speed of approximately 2 meters per minute. As
accepted good practice, the following installation recommendations should be abided by:
•
The bending radius of the cables should be kept to a minimum of 60 mm
•
The junction boxes should be positioned on top at all times.
•
Bend or twist of the modules (without snow or wind loads) shall be kept < 3 mm/m
•
The minimum distance between glass edges of the solar modules should be 150 mm
•
Welding seam width between solar module backsheet membrane and membrane surface should be at
least 40 mm
•
Welding must be done on all 4 edges of the solar module