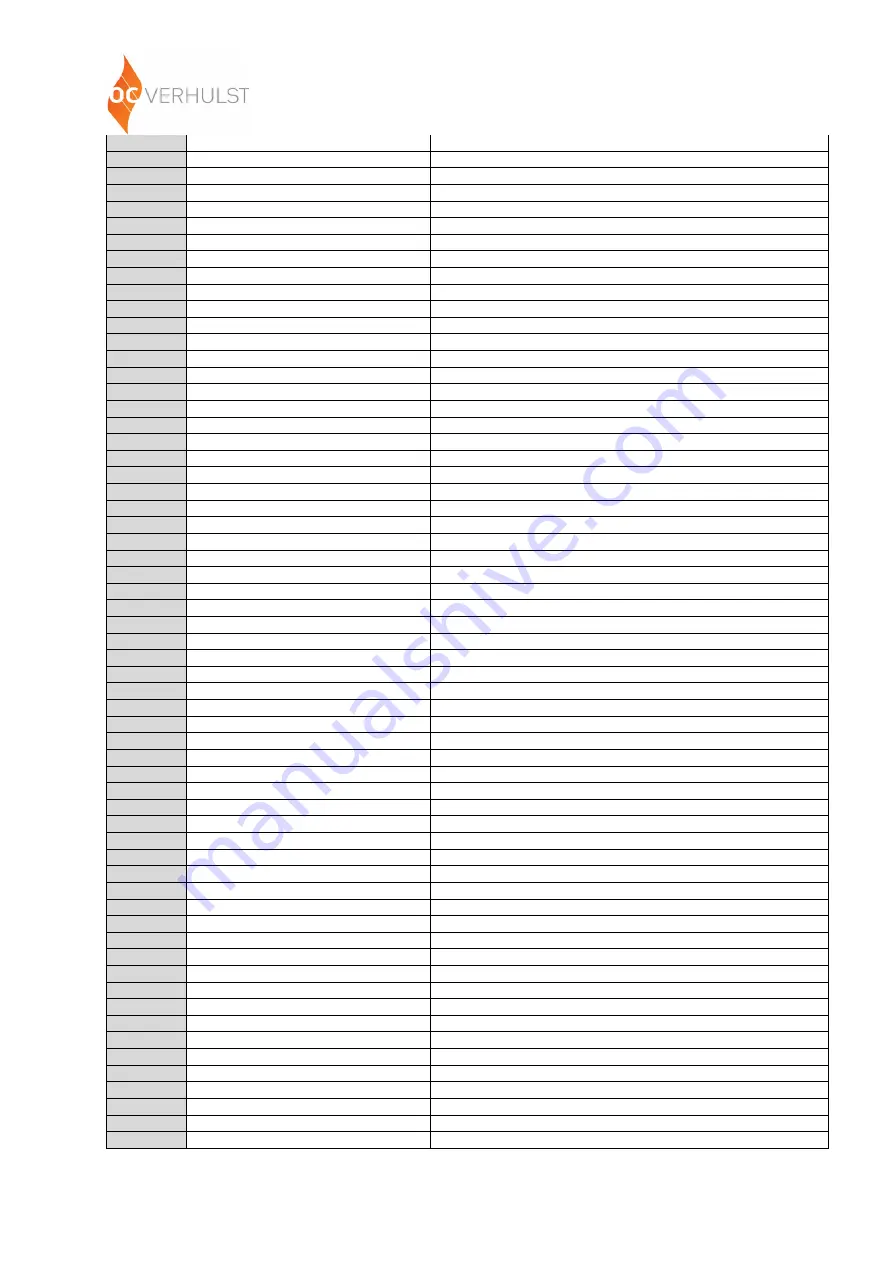
Version 5.2_2022 (January 26, 2022)
39
58
Automatic reset
DC voltage high EBM 2
59
Automatic reset
Supply voltage high EBM 2
60
Automatic reset
Line resistance high EBM 2
61
Automatic reset
Offline EBM 3
62
Manual reset
Phase fault EBM 3
63
Manual reset
Motor blocked EBM 3
64
Manual reset
Undervoltage power supply EBM 3
65
Manual reset
Overvoltage power supply EBM 3
66
Manual reset
Overvoltage DC connection EBM 3
67
Manual reset
Undervoltage DC connection EBM 3
68
Manual reset
Overheating motor EBM 3
69
Manual reset
Internal circuit overheating EBM 3
70
Manual reset
Overheating of outgoing phase EBM 3
71
Manual reset
Hall sensor fault EBM 3
72
Manual reset
Communication fault EBM 3
73
Manual reset
General fault EBM 3
74
Automatic reset
High temperature outgoing phase EBM 3
75
Automatic reset
High temperature internal circuit EBM 3
76
Automatic reset
High temperature motor EBM 3
77
Automatic reset
Low voltage DC connection EBM 3
78
Automatic reset
Output limit power supply EBM 3
79
Automatic reset
Current limit power supply EBM 3
80
Automatic reset
Braking mode EBM 3
81
Automatic reset
Cable break EBM 3
82
Automatic reset
Ice protection EBM 3
83
Automatic reset
Heating: motor stop EBM 3
84
Automatic reset
Speed below limit EBM 3
85
Automatic reset
DC voltage high EBM 3
86
Automatic reset
Supply voltage high EBM 3
87
Automatic reset
Line resistance high EBM 3
88
Automatic reset
Offline EBM 4
89
Manual reset
Phase fault EBM 4
90
Manual reset
Motor blocked EBM 4
91
Manual reset
Undervoltage power supply EBM 4
92
Manual reset
Overvoltage power supply EBM 4
93
Manual reset
Overvoltage DC connection EBM 4
94
Manual reset
Undervoltage DC connection EBM 4
95
Manual reset
Overheating motor EBM 4
96
Manual reset
Internal circuit overheating EBM 4
97
Manual reset
Overheating of outgoing phase EBM 4
98
Manual reset
Hall sensor fault EBM 4
99
Manual reset
Communication fault EBM 4
100
Manual reset
General fault EBM 4
101
Automatic reset
High temperature outgoing phase EBM 4
102
Automatic reset
High temperature internal circuit EBM 4
103
Automatic reset
High temperature motor EBM 4
104
Automatic reset
Low voltage DC connection EBM 4
105
Automatic reset
Output limit power supply EBM 4
106
Automatic reset
Current limit power supply EBM 4
107
Automatic reset
Braking mode EBM 4
108
Automatic reset
Cable break EBM 4
109
Automatic reset
Ice protection EBM 4
110
Automatic reset
Heating: motor stop EBM 4
111
Automatic reset
Speed below limit EBM 4
112
Automatic reset
DC voltage high EBM 4
113
Automatic reset
Supply voltage high EBM 4
114
Automatic reset
Line resistance high EBM 4
115
Automatic reset
EBM1 offline due to power disconnection
116
Automatic reset
EBM2 offline due to power disconnection
117
Automatic reset
EBM3 offline due to power disconnection
118
Automatic reset
EBM4 offline due to power disconnection