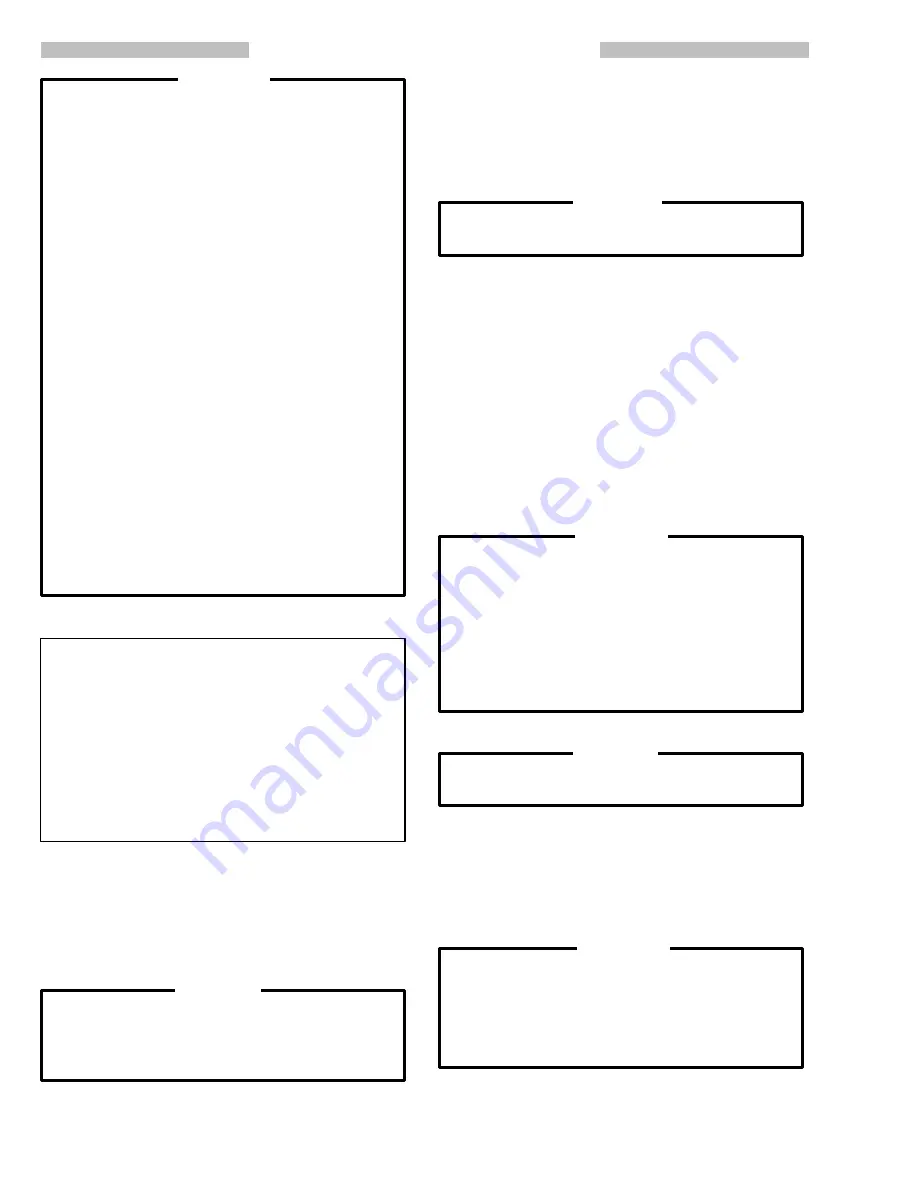
GENERAL REPAIR INFORMATION
Pressure Relief Procedure
To reduce the risk of serious bodily injury, including
fluid injection, injury from splashing fluid or solvent
in the eyes or on the skin, moving parts or electric
shock, always follow this procedure whenever you
shut off the sprayer, when checking or servicing any
part of the spray system, when installing, cleaning
or changing spray tips, and whenever you stop
spraying.
1. Engage the gun safety latch.
2. Turn the ON/OFF switch to OFF.
3. Unplug the power supply cord.
4. Disengage the gun safety latch. Hold a metal
part of the gun firmly to the side of a grounded
metal pail, and trigger the gun to
relieve
pressure.
5. Engage the gun safety latch.
6. Open the pressure drain valve, having a con-
tainer ready to catch the drainage. Leave the
pressure drain valve open until you are ready to
spray again.
If you suspect that the spray tip or hose is com-
pletely clogged, or that pressure has not been fully
relieved after following the steps above, loosen the
tip guard retaining nut or hose end coupling and
VERY SLOWLY loosen the part to relieve pressure
gradually, then loosen completely. Now clear the tip
or hose obstruction.
WARNING
Phillips screwdriver
Small flat blade
screwdriver
Needle nose pliers
Plastic mallet
Adjustable wrench
Adjustable, open–end
wrench
Torque wrench
1/4 in. hex key wrench
3/16 in. hex key wrench
5/8 in. socket wrench
3/8 in. open end wrench
1/2 in. open end wrench
3/4 in. open end wrench
7/8 in. open end wrench
High quality motor oil
Bearing grease
Tool List
5. When disconnecting wires
in the pressure control
assembly, use needle nose pliers to separate mating
connectors.
6. When reconnecting the wires
, be sure the flat blade
of the insulated male connector is centered in the
wrap–around blade of the female connector.
To reduce the risk of a pressure control malfunction,
be sure to properly mate connectors, and never pull
on a wire to disconnect it. Pulling on a wire could
loosen the connector from the wire.
CAUTION
7. Route wires carefully
in the pressure control assem-
bly, guiding them through the legs of the U–shaped
bourdon tube. This is to avoid interfering with the
bourdon tube, which moves as the pressure setting
changes, and to avoid pinching the wires between the
pressure control and cover.
CAUTION
Improper wire routing can result in poor sprayer per-
formance or damage to the pressure control.
8. Keep all screws, nuts, washers, gaskets, and
electrical fittings
removed during repair proce-
dures. These parts are not normally provided with re-
placement assemblies.
9. Test your repair before regular operation
of the
sprayer to be sure the problem is corrected.
10. If the sprayer does not operate properly
, review
the repair procedure again to verify that everything
was done correctly . If necessary , refer to the
Troubleshooting Guide, pages 14–19, to help identify
other possible problems and solutions.
To reduce the risk of serious bodily injury, including
electric shock, DO NOT touch any moving parts or
electrical parts with your fingers or a tool while in-
specting the repair.
Shut off the sprayer and unplug it as soon as you
complete the inspection.
Reinstall all covers, gaskets, screws and washers
before operating the sprayer.
WARNING
CAUTION
Do not run the sprayer dry for more than 30 seconds
to avoid damaging the pump packings.
11. Reinstall the motor shield before regular opera-
tion
of the sprayer and replace it if it is damaged. The
cover directs cooling air around the motor to help pre-
vent overheating. It can also help reduce the risk of
burns, fire or explosion; see the
WARNING,
below.
During operation, the motor and drive housing be-
come very hot and could burn your skin if touched.
Flammable materials spilled on the hot, bare motor
could cause a fire or explosion. Always have the mo-
tor shield in place during regular operation to reduce
the risk of burns, fire or explosion.
WARNING