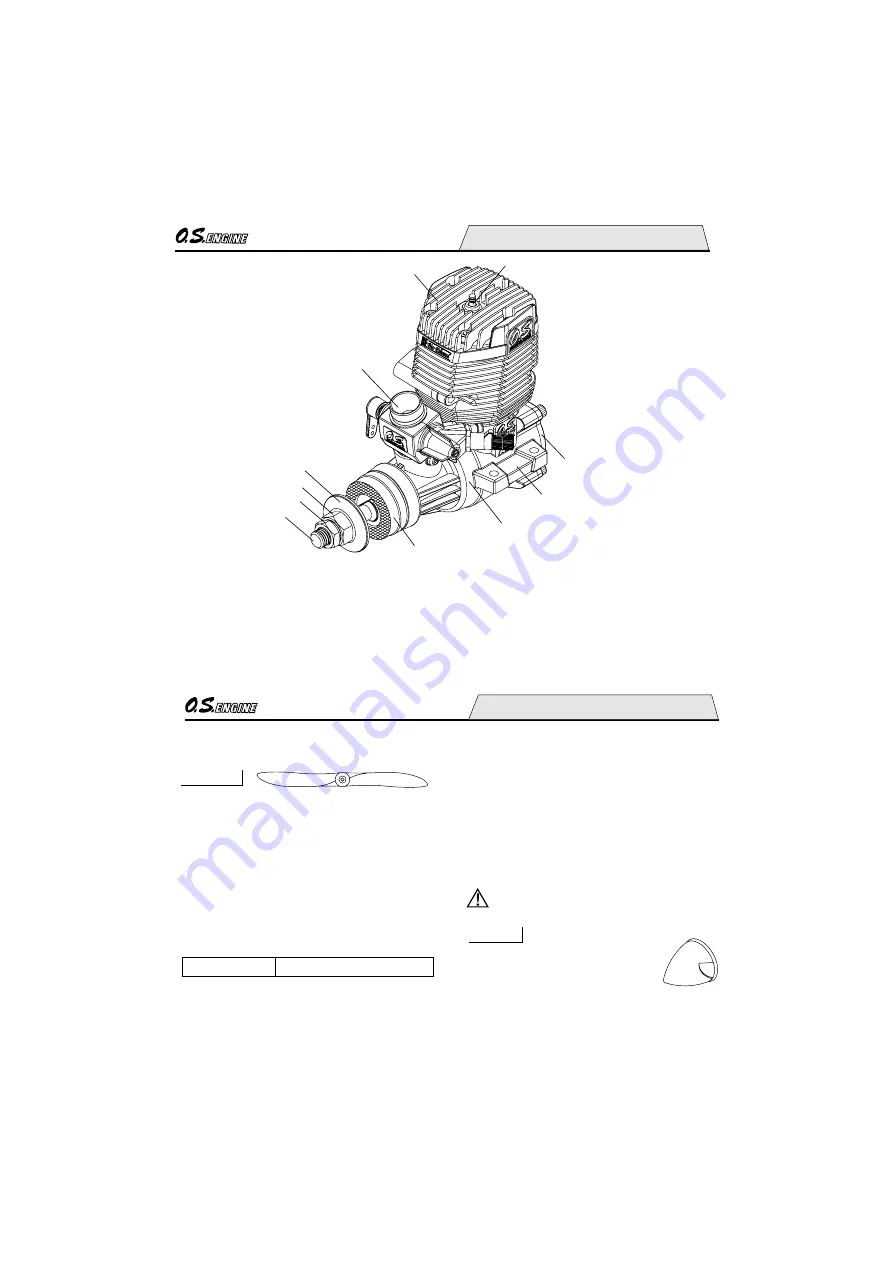
10
BASIC ENGINE PARTS
Cylinder head
Carburetor Type 61A-BE
Crankshaft
Propeller nut
Propeller washer
Drive Hub
Crankcase
Cover Plate
Glowplug
Beam Mount
Lock nut
11
Tools, accessories, etc. The following items
are necessary for operating the engine.
BEFORE STARTING
The choice of propeller depends on the design
and weight of the aircraft and the type of flying
in which you will be engaged. Determine the
best size and type after practical
experimentation. As a starting point, refer to
the props listed in the accompanying table.
Slightly larger, or even slightly smaller, props
than those shown in the table may be used,
but remember that the propeller noise will
increase, due to higher rpm or if a larger-
diameter/lower-pitched prop is used.
Propellers
13x9-10, 14x6-8, 15x6
Sport
Never touch, or allow any object to come into
contact with, the rotating propeller and do not
crouch over the engine when it is running.
Reminder!
Warning:
Make sure that the propeller is well
balanced. An unbalanced propeller and/or
spinner can cause serious vibration which
may weaken parts of the airframe or affect
the safety of the radio-controlled system.
DO NOT forget the WARNINGS and NOTES
on propeller and spinner safety given on
front pages.
Since the 75AX-BE is intended to
be started with an electric starter,
the addition of a spinner
assembly for centering the starter sleeve is
desirable. Use a heavy-duty, well balanced
spinner either of metal or plastic.
Spinner
It is suggested to use propellers which develop
maximum r.p.m. of 8,500~9,500 so that you
may enjoy pleasant exhaust sound keeping it
low.