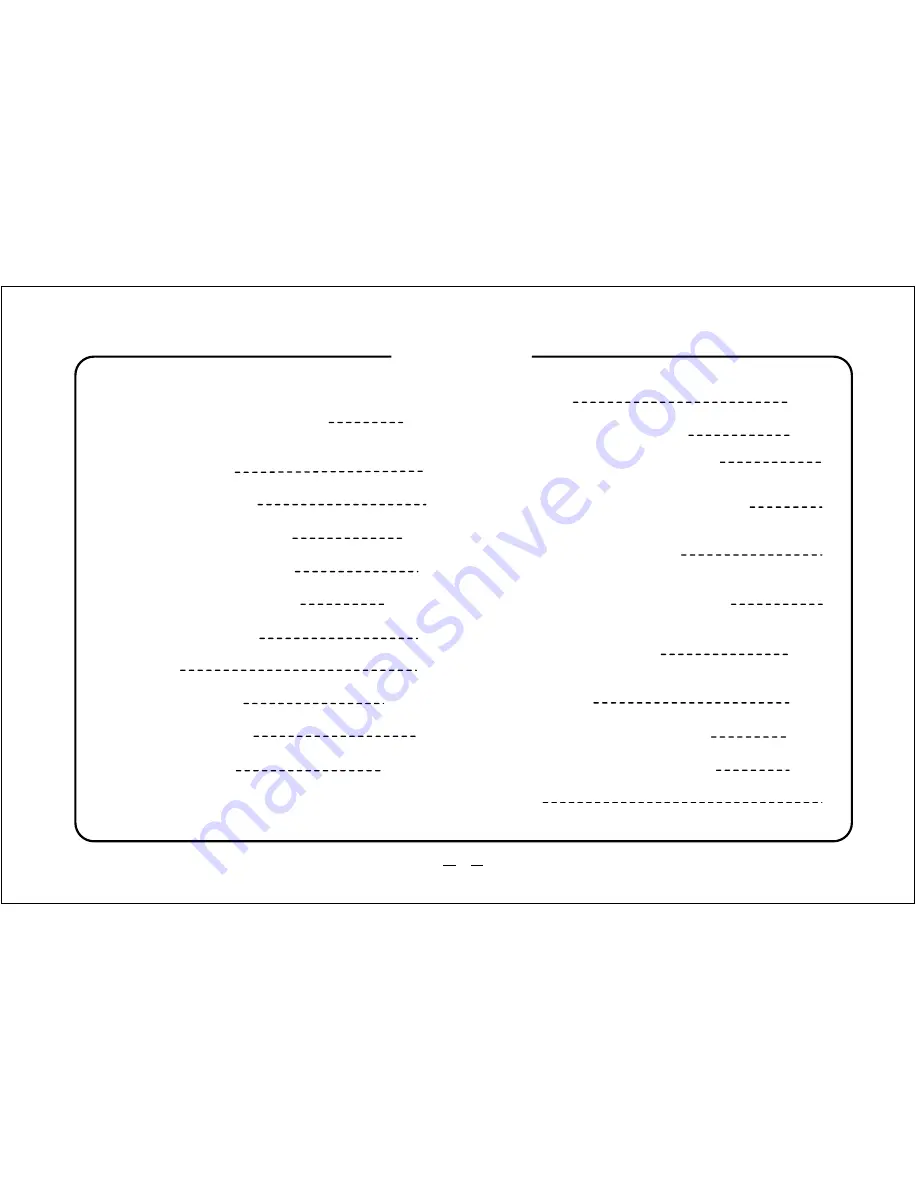
SAFETY INSTRUCTIONS AND
WARNINGS ABOUT YOUR O.S. ENGINE
FEATURES OF FX SERIES ENGINES, BEFORE
INSTALLING THE ENGINE
BASIC ENGINE PARTS
NEEDLE-VALVE LOCATION
INSTALLATION OF THE ENGINE
THROTTLE LINKAGE, SILENCER
FUEL TANK LOCATION
GLOWPLUG
FUEL, PROPELLERS
MIXTURE CONTROLS
BEFORE STARTING
RUNNING-IN (Breaking-in)
IDLING ADJUSTMENT CHART
MIXTURE CONTROL VALVE ADJUSTMENT,
REALIGNMENT OF MIXTURE CONTROL VALVE
SUBSEQUENT STARTING PROCEDURE
SUBSEQUENT READJUSTMENT
CARBURETOR CLEANLINESS,
ENGINE CARE AND MAINTENANCE
ENGINE EXPLODED VIEWS &
ENGINE PARTS LISTS
CARBURETOR EXPLODED VIEWS
& PARTS LISTS
GENUINE O.S. PARTS & ACCESSORIES
ENGINE THREE VIEW DRAWINGS
MEMO
STARTING
CONTENTS
17
~
18
2
~
6
7
8
8
~
9
10
11
~
12
12
13
14
~
15
15
16
~
17
19
~
21
22
23
24
25
36
~
37
26
~
33
34
~
35
38
~
41
42
1