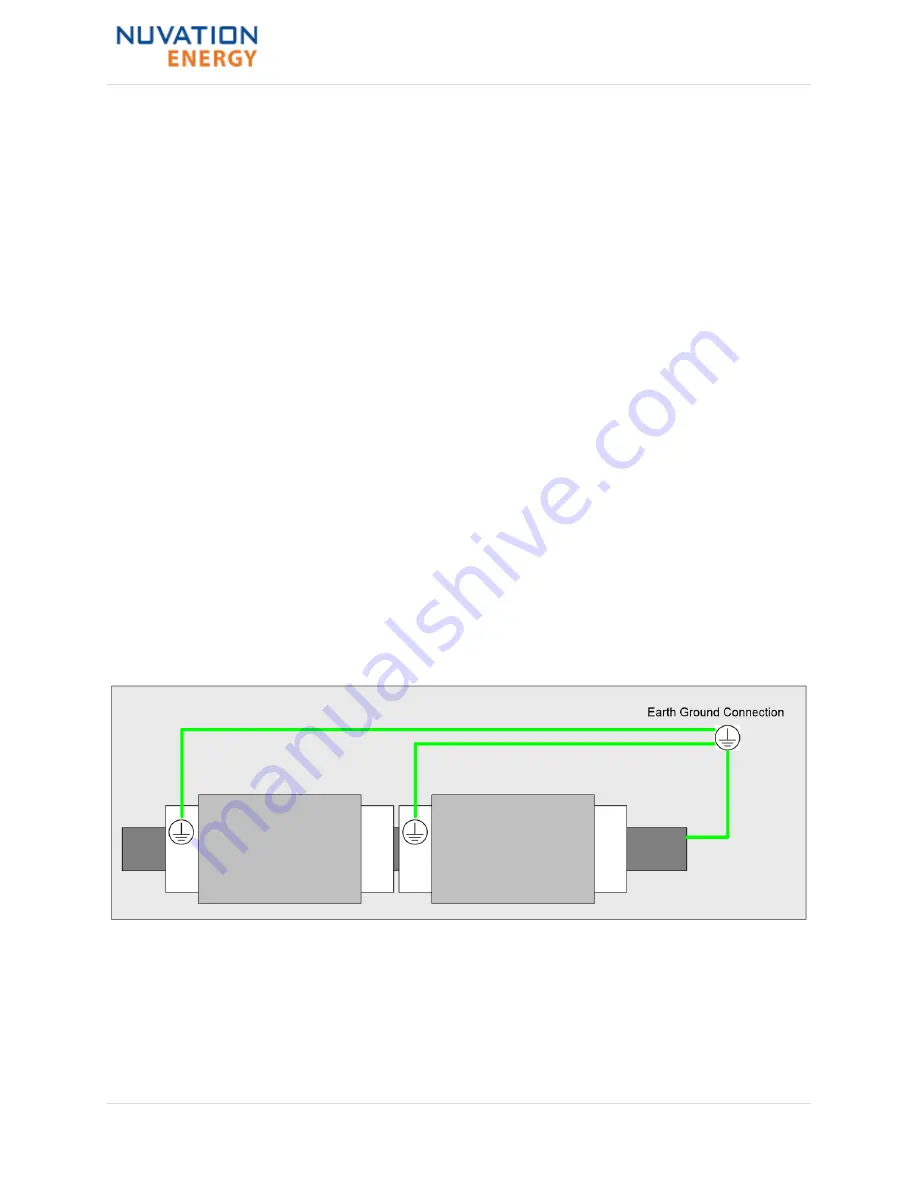
6. Nuvation BMS: Best Practices
This section describes important concepts which need special attention to achieve a reliable
installation.
6.1. Grounding
It is assumed that the Nuvation BMS will be attached electrically to an earth or local chassis
ground point, via the DIN rail grounding provision (#8-32 ,
¼
” Hex-head drive, earth grounding
screw), and the mounting brackets on the Nuvation BMS component enclosures.
Voltages and signals on the Stack Bus and Link Bus cables are chassis/earth ground referenced. In
addition, the Stack Controller’s USB port, non-isolated RS485, and GPIO-In signals; and the Power
Interface’s Contactor coils and Interlock signals are chassis/earth ground referenced.
All connections to the battery stack are isolated from chassis ground. This includes the Current
Shunt, Thermistor, and Stack Power connections on the Power Interface; and the Battery Cells and
Temperature Sensors connections on the Cell Interface, and Ethernet and CAN interfaces on the
Stack Controller.
It is acceptable, as may be required in some cases, for the battery stack to be ground-referenced
at some single point. However, a 24VRMS AC or 24VDC power supply connected to the Power
Interface’s External Power connection must be isolated from earth/chassis ground, with a working
isolation voltage of at least 60Vrms for all Power Interface models.
Protective earthing conductors must be attached to each DIN enclosure at the designated ground
screw location on the DIN clip. Furthermore, the DIN rail itself should be connected to earth
ground. 14AWG wire with a jacket color appropriate for indicating it is a protective earthing
conductor must be used.
An example of this grounding scheme is shown below:
Figure 14. Example Earth Ground Wiring Diagram
6.2. Excess Cable Management
During the first prototype system build, it is possible to encounter cable lengths that are too long
for your system. Leaving the excess cable length unmanaged can result in a messy system
installation.
Installation Guide - 2018-10-08, Rev. 2.0
33