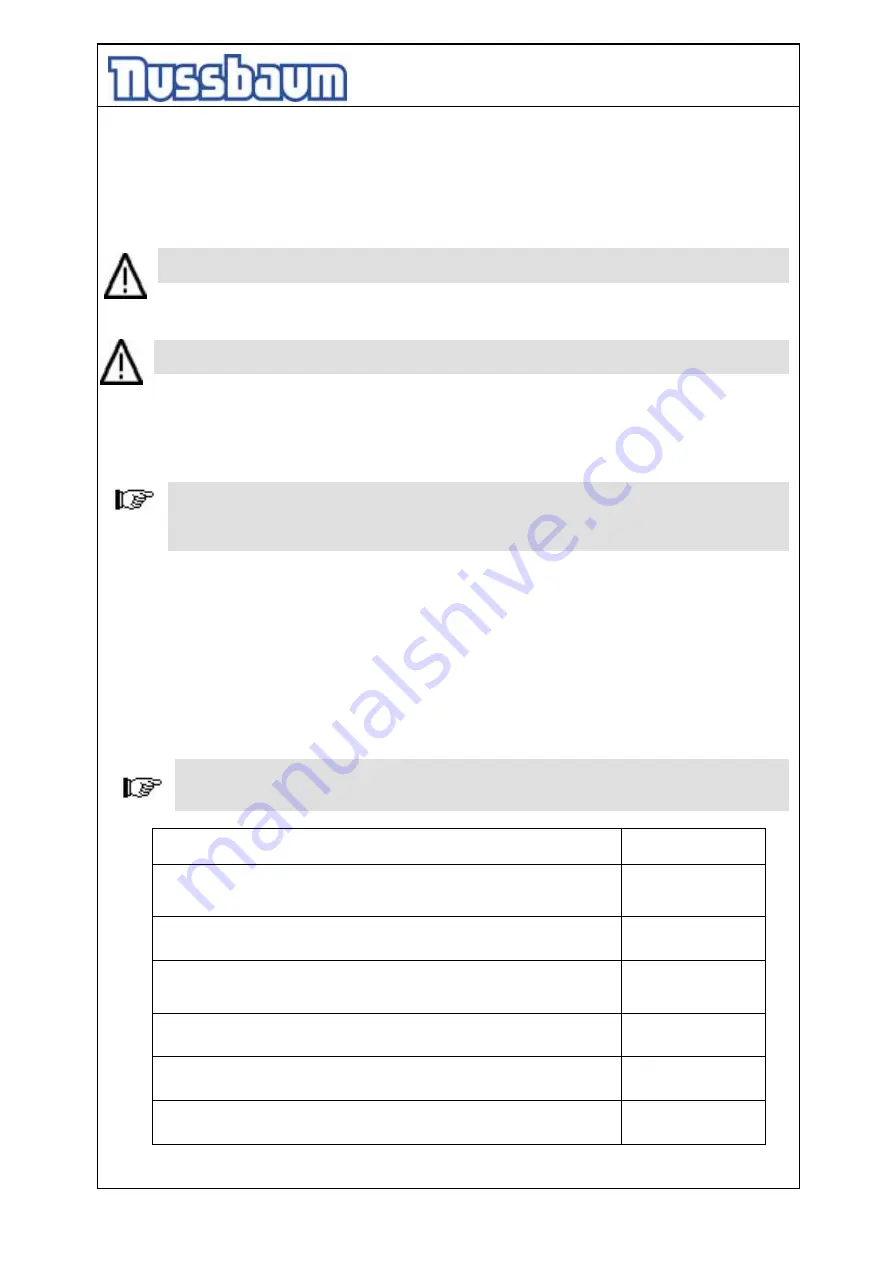
Operating Instruction and Documentation
UNI-LIFT 4000
- 47 -
• Fasten set screw and secure it by fastening the security screw.
• Drive off vehicle from the lift.
• After power is reinstalled, push button ”Lifting” and lift the lift until the access to the valves at
the cylinders’ bottom is free.
• Turn out set screws at the valve located at the bottom of each cylinder to the position they
have had before. Secure it with the security nut.
After finishing the emergency lowering, all the three set screws must be brought into
the position they have had before. Otherwise a malfunction of the lift can occur
• Reinstall covers at the cylinder’ s bottoms and at the command unit.
Switch off the main switch and lock it. Do not work with the lift until the faulty parts are
exchanged.
7. Inspection and Maintenance
Before conducting maintenance work, preparations must be made to ensure that
during maintenance and repair work there is no risk to the safety of people working
on or around the lift and also that there is no risk of damage to equipment being used
on or around the lift.
To guarantee the utmost availability and to ensure that the lift remains functional, maintenance
work contracts are organised between our clients and their local retailers.
A service must be performed at regular intervals of 3 months through the operator in
accordance with following service manual. If the lift is in continuous operation or in a dirty
environment, the maintenance rate must be increased.
During daily operation the lift must be closely observed to ensure that it is functioning correctly.
In the case of malfunction or leakage the technical service must be informed.
7.1 Maintenance plan of the lift
Before beginning any maintenance work isolate the power supply. Secure the main
switch (lock it). Secure the danger area around the automotive lift and secure the lift
against unintentional lowering.
Maintenance plan
Period
Clean the piston rod from dirt with air pressure. Check the piston for
damages.
min. once in a year
Clean and check the stripper of the cylinder.
min. once in a year
Clean and lubricate the moving parts of the lift (hinge bolts, sliding
pieces, sliding surfaces) grease with a multipurpose liquid (e.g.: Auto
Top 2000 LTD. Agip).
min. once in a year
Check the condition of the DU bush bearings. In case of damages
exchange it.
min. once in a year
Check the condition of the white polymer supports. If necessary
exchange it.
min. once in a year
Examine the electrical parts for damages (cables, switches, plugs,
press buttons, optional: lighting, etc.)
min. once in a year
Summary of Contents for UNI-LIFT 4000 MB
Page 4: ...Operating Instruction and Documentation UNI LIFT 4000 4...
Page 5: ...Operating Instruction and Documentation UNI LIFT 4000 5...
Page 6: ...Operating Instruction and Documentation UNI LIFT 4000 6...
Page 7: ...Operating Instruction and Documentation UNI LIFT 4000 7...
Page 8: ...Operating Instruction and Documentation UNI LIFT 4000 8...
Page 9: ...Operating Instruction and Documentation UNI LIFT 4000 9...
Page 16: ...Operating Instruction and Documentation UNI LIFT 4000 16 2 5 Declaration of conformity...
Page 18: ...Operating Instruction and Documentation UNI LIFT 4000 18 3 3 Datasheet...
Page 19: ...Operating Instruction and Documentation UNI LIFT 4000 19...
Page 22: ...Operating Instruction and Documentation UNI LIFT 4000 22...
Page 23: ...Operating Instruction and Documentation UNI LIFT 4000 23 3 4 Hydraulic diagram drawing...
Page 25: ...Operating Instruction and Documentation UNI LIFT 4000 25 3 5 Electrical diagram drawing...
Page 26: ...Operating Instruction and Documentation UNI LIFT 4000 26...
Page 27: ...Operating Instruction and Documentation UNI LIFT 4000 27...
Page 28: ...Operating Instruction and Documentation UNI LIFT 4000 28...
Page 29: ...Operating Instruction and Documentation UNI LIFT 4000 29...
Page 30: ...Operating Instruction and Documentation UNI LIFT 4000 30...
Page 31: ...Operating Instruction and Documentation UNI LIFT 4000 31...
Page 32: ...Operating Instruction and Documentation UNI LIFT 4000 32...
Page 33: ...Operating Instruction and Documentation UNI LIFT 4000 33...
Page 34: ...Operating Instruction and Documentation UNI LIFT 4000 34...
Page 35: ...Operating Instruction and Documentation UNI LIFT 4000 35...
Page 36: ...Operating Instruction and Documentation UNI LIFT 4000 36...
Page 37: ...Operating Instruction and Documentation UNI LIFT 4000 37 3 7 Electrical plug connection...