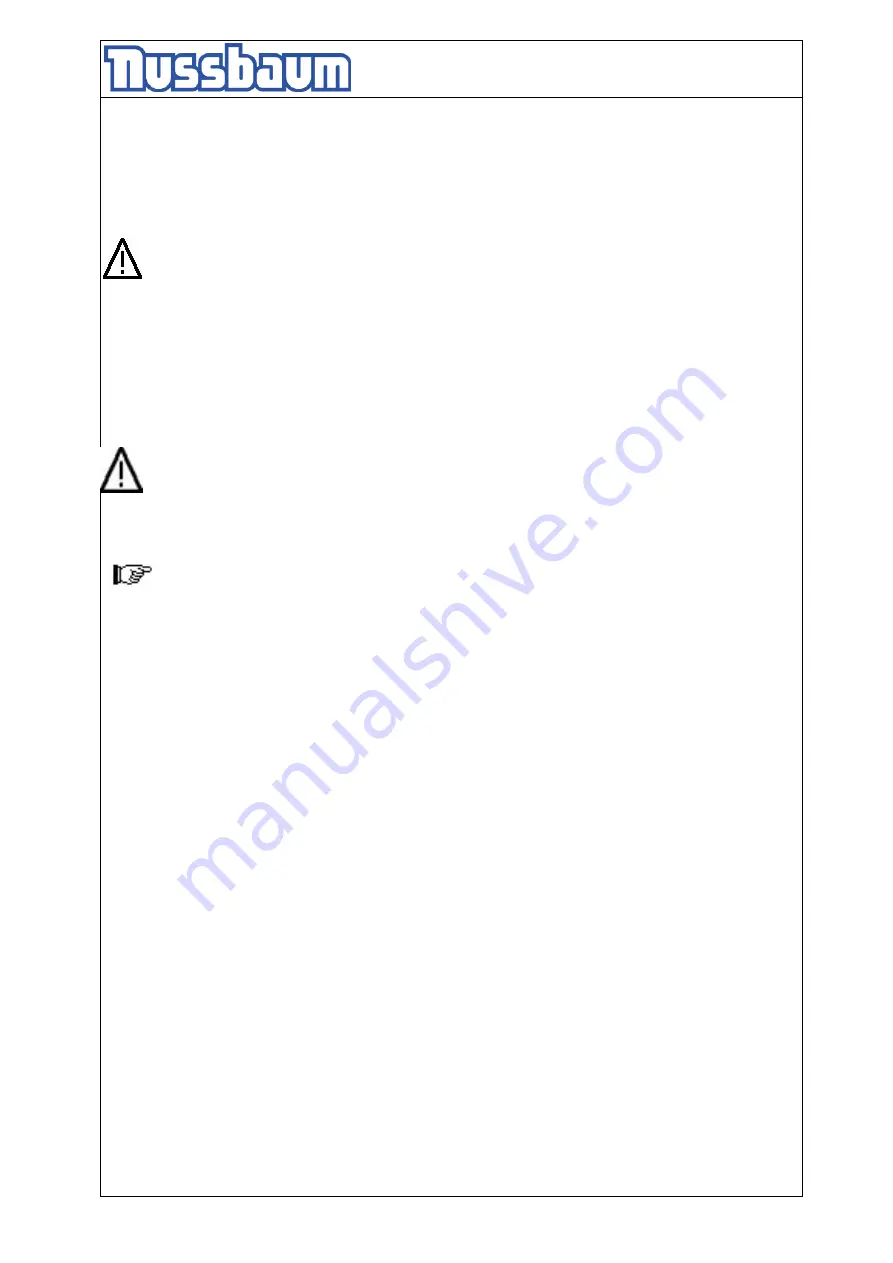
Operating instructions and documentation
4.65H/ 4.65 plus
- 29 -
6.3 Emergency lowering of the wheel free lift
In case of power failure or defective valves, the hydraulic valves for lowering of the wheel
free jack and the safety valves at lower side of the hydraulic cylinders and the magnet to
unlock the ratchet can not be opened. Therefore the lift cannot be lowered. In this case
it is possible to lower the lift by opening the hydraulic valve manually, so the vehicle
can be driven off.
The emergency lowering must only be performed by persons instructed to use the lift.
Please refer to the regulation "Lowering".
• Put the lever (on the side of the rail) on position wheel free lift.
• On the cylinder (wheel free lift) are safety valves. Unscrew the red locknut and
turn the set screw with a hexagon socket screw key one direction clockwise.
• Unscrew the red locknut (on the side of the rail) and turn the set screw with a
hexagon socket screw key one direction anticlockwise.
• The lowering process starts. Observe the complete process.
• If the wheel free lift is in the lowest position. Fasten and safe the set screw and
the locknut.
After finishing the emergency lowering, the emergency screw and the red security nut
must be brought into the position they have had before. Otherwise malfunction of the
wheel free jack can occur.
7 Inspection and maintenance
Before conducting maintenance work, preparations must be made to ensure that
during maintenance and repair work there is no risk to the safety of people working on
or around the lift and also that there is no risk of damage to equipment being used on
or around the lift.
To guarantee the utmost availability and to ensure that the lift remains functional, maintenance
work contracts are organised between our clients and their local retailers.
A service must be performed at regular intervals of 3 months through the operator in accordance
with following service manual. If the lift is in continuous operation or in a dirty environment, the
maintenance rate must be increased.
During daily operation the lift must be closely observed to ensure that it is functioning correctly. In
the case of malfunction or leakage the technical service must be informed.
7.1 Maintenance plan of the lift
•
Before beginning any maintenance work isolate the power supply. Secure the main switch (lock it). Secure
the danger area around the automotive lift and secure the lift against unintentional lowering.
• Clean and check the stripper of the cylinder.
• Clean the piston-rod using compressed air.
• Clean the protection hose at the operating column. Grease it with a multipurpose liquid, otherwise the hose
sticks to the column.
• Check the condition of ropes. If torn wires are discovered, the complete rope-set must be changed.
• Check the condition of the electrical parts.
• Clean and lubricate the moving parts of the lift (hinge bolts, sliding pieces, sliding surfaces) grease with a
multipurpose liquid (example: Auto Top 2000 LTD. Agip).
• Grease the lubricate nipples with a multipurpose lipid. (i.e. Auto Top 2000 LTD. Agip).
• Clean and check the function of the ratchet. Grease the surface with a multipurpose lipid.
• Check all welded joints for cracks on the automotive-lift.
If any cracks are found on the lift cease use immediately. Switch-off and secure the main switch (lock) and
call the service partner.
• Check all surfaces and repair if necessary.
• Damage to external surfaces, must be immediately repaired.
Summary of Contents for 4.65H
Page 9: ...Operating instructions and documentation 4 65H 4 65 plus 9 2 5 Declaration of conformity ...
Page 11: ...Operating instructions and documentation 4 65H 4 65 plus 11 3 3 Datasheet ...
Page 12: ...Operating instructions and documentation 4 65H 4 65 plus 12 ...
Page 36: ...Operating instructions and documentation 4 65H 4 65 plus 36 9 7 Position of the columns ...