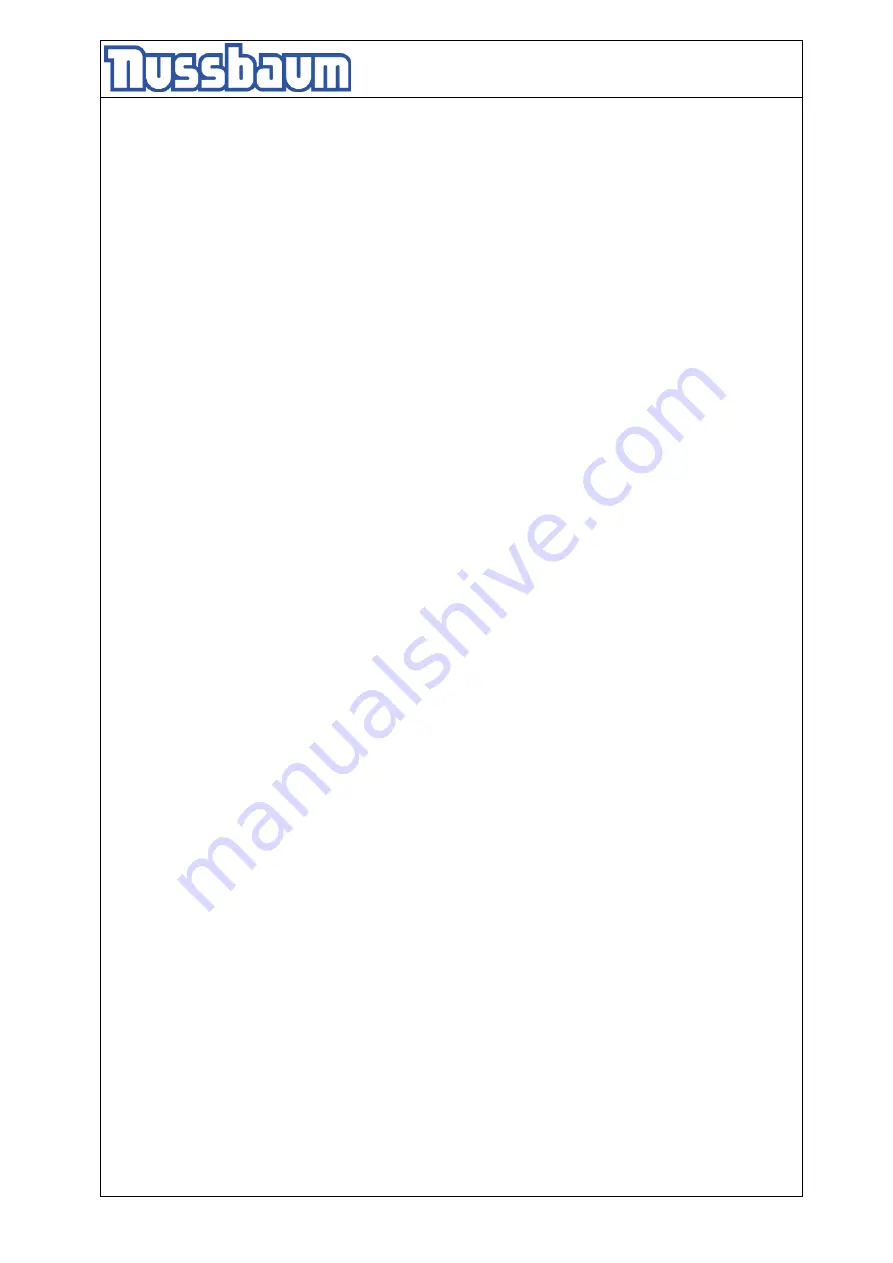
Operating instructions and documentation
4.50H/ 4.50H plus
- 6 -
Record of handing over
The automotive lift
with the serial number: ............................................
was installed on:...............................
at the firm:................................................. ……... ….
in:.........................................................
The lift was installed, checked and started up.
The persons below were familiarized with the operation of the automotive lift after the installation. The
briefing was performed by an expert from the lift-manufacturer or from a franchised dealer:
............................................
...................................................
........................................
date
name
signature
............................................
...................................................
........................................
date
name
signature
............................................
...................................................
........................................
date
name
signature
............................................
...................................................
........................................
date
name
signature
............................................
...................................................
........................................
date
name
signature
............................................
...................................................
........................................
date
name
signature
............................................
............................................. ….
........................................
date
name of expert
signature of the expert
Your customer service: .................................................................................................................................