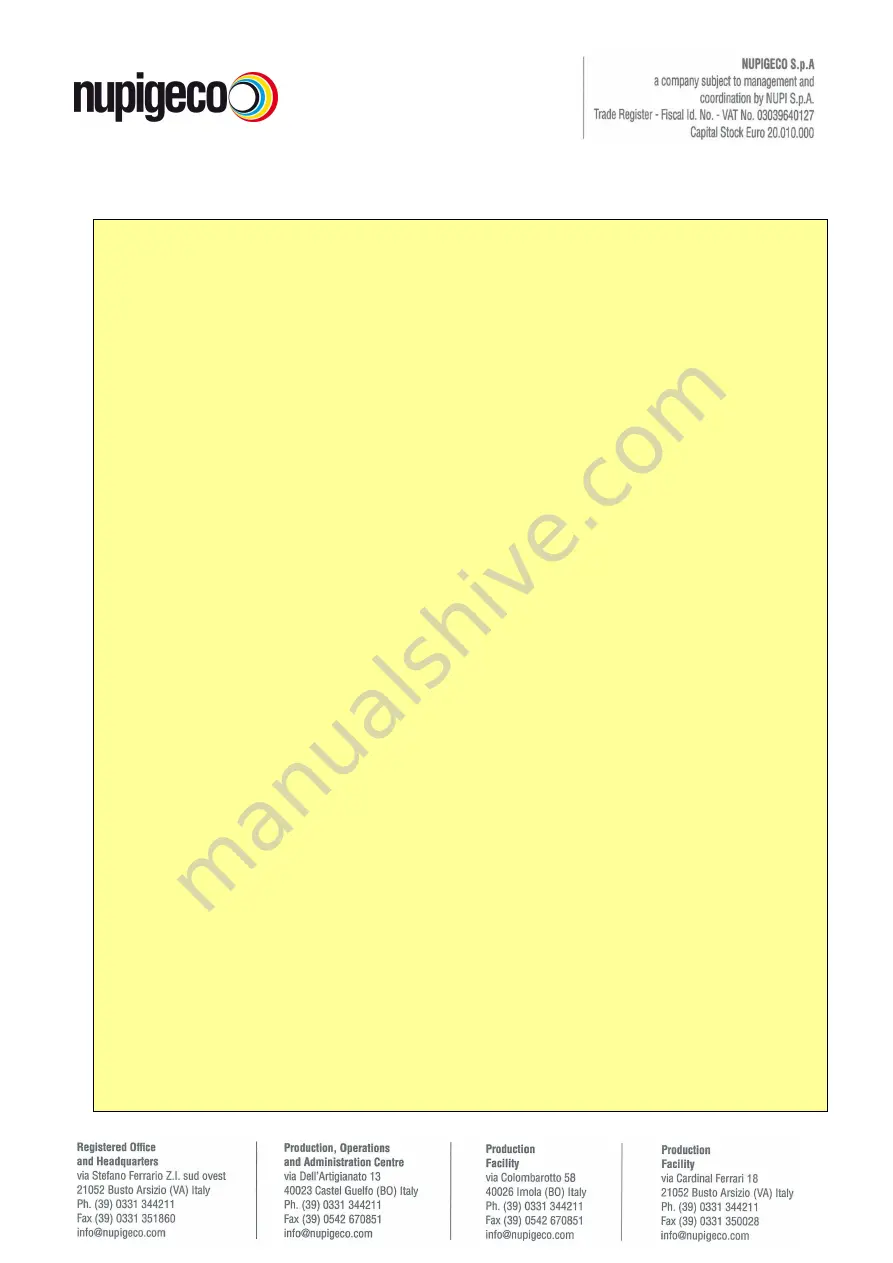
PROCEDURE
1. Turn off and shut down the electrical supply to the submersible pump (if present) and the
dispensers. This may require the assistance of authorised personnel.
2. Disconnect the pump and any dispenser devices.
3. Ready the UST closest dispenser hose to release pipeline pressure and to empty the product
into a suitable sealed containment vessel.
4. Empty the line completely of any fuels.
5. Test the confined space in the sump to be repaired by the use of an (O²) Oxygen sensor /
meter.
6. Before any personnel enter the sump, check the presence of enough (O²) Oxygen.
7. Close the ball valve of the submersible pump.
8. Open the test ports on the secondary containment fittings.
9. Detach the product line from the tank sump connection.
10. Assure to collect any residual fluid into the sealed containment vessel.
11. Open the shear valve access ports of the interested line to permit the fluid to flow down to the
tank sump.
12. Close the shear valve when the line is completely drained and dried.
13. Ventilate the sump to achieve an Oxygen (O²) level suitable for personnel to re-enter (20-
25%).
14. Remove the filled containment vessel from the tank sump.
15. Proceed with the repairing process following the Smartflex installation instructions.
16. During the repairing process care shall be taken to keep the line and the sumps continuously
purged with an inert gas like Nitrogen. It is important to monitor continuously the (O²) Oxygen
level.
17. Fill the line to be repaired and the sumps with Nitrogen until no Oxygen (O²) present (to be
checked with the (O²) Oxygen meter.
18. Place the welding unit as far as possible from the repairing site/area, above ground; ensuring
that the connecting cables are not tensioned.
19. Turn off the Nitrogen supply and, immediately commence the welding process.
20. At the end of the welding process, turn off the welding unit power supply and again start to
convey Nitrogen into the line and sump leaving the connecting cables connected to the fitting.
21. The flow of Nitrogen should continue for least 20-30 minutes during the cool down period.
22. Permit air exchange and when the (O²) level again reaches 20-25% the operator can enter the
welding zone and disconnect the cables.
23. Once the repairing process has been completed, the line shall be pressure tested as per the
Smartflex instruction (see Smartflex Technical Catalogue for more details).
24. After a positive result of the pressure test has been achieved, the line can be re-commissioned
and start working again.