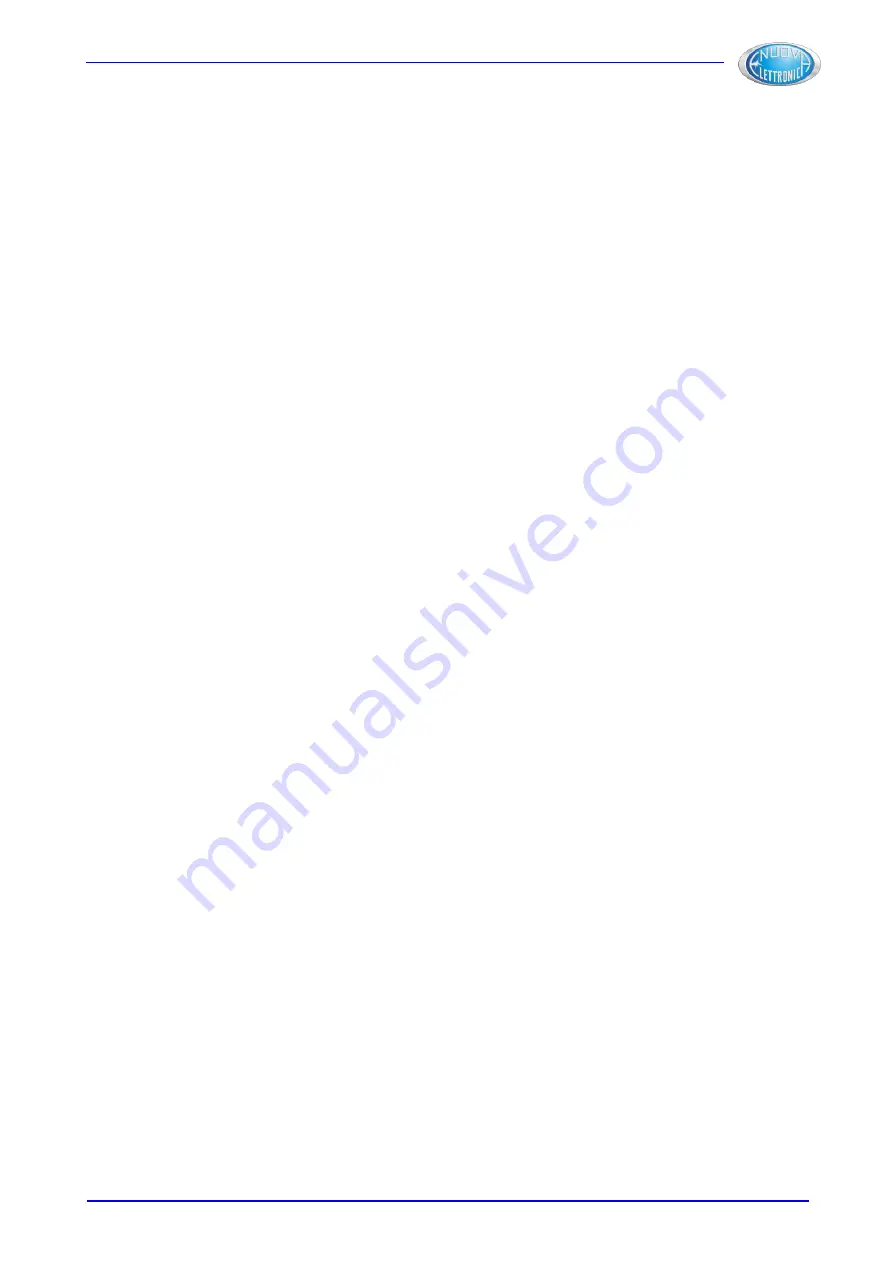
DSP
LASER
DSPLSR01EN
7
•
Stop immediately using the device in case of penetration of liquids or objects in it.
Disconnect the device and make it is checked by qualified personnel.
In order to disconnect the device, refer to the procedure described in the chapter
relevant to the removal of the device.
6.6.
Spare parts
The spare parts can be provided only by Nuova Elettronica.
6.7.
Decommissioning
When you decide not to use the device DSP LASER anymore because obsolete or
irreparably faulted, execute the decommissioning making the device itself not operating and
free from dangers. Seal the device inside a robust package and provide to its disposal
operating in compliance with the current laws, asking to the local bodies charged for these
operations.
Summary of Contents for DSP LASER
Page 2: ......
Page 4: ......
Page 48: ...DSP LASER 44 DSPLSR01EN CONNECTION SCHEMES Fig 13 6 scheme of connection with AL1B...
Page 49: ...DSP LASER DSPLSR01EN 45 Fig 13 7 scheme of connection with AL2B...
Page 50: ...DSP LASER 46 DSPLSR01EN Fig 13 8 scheme of connection with ALdc...
Page 51: ...DSP LASER DSPLSR01EN 47 Fig 13 9 scheme of connection without AL module...