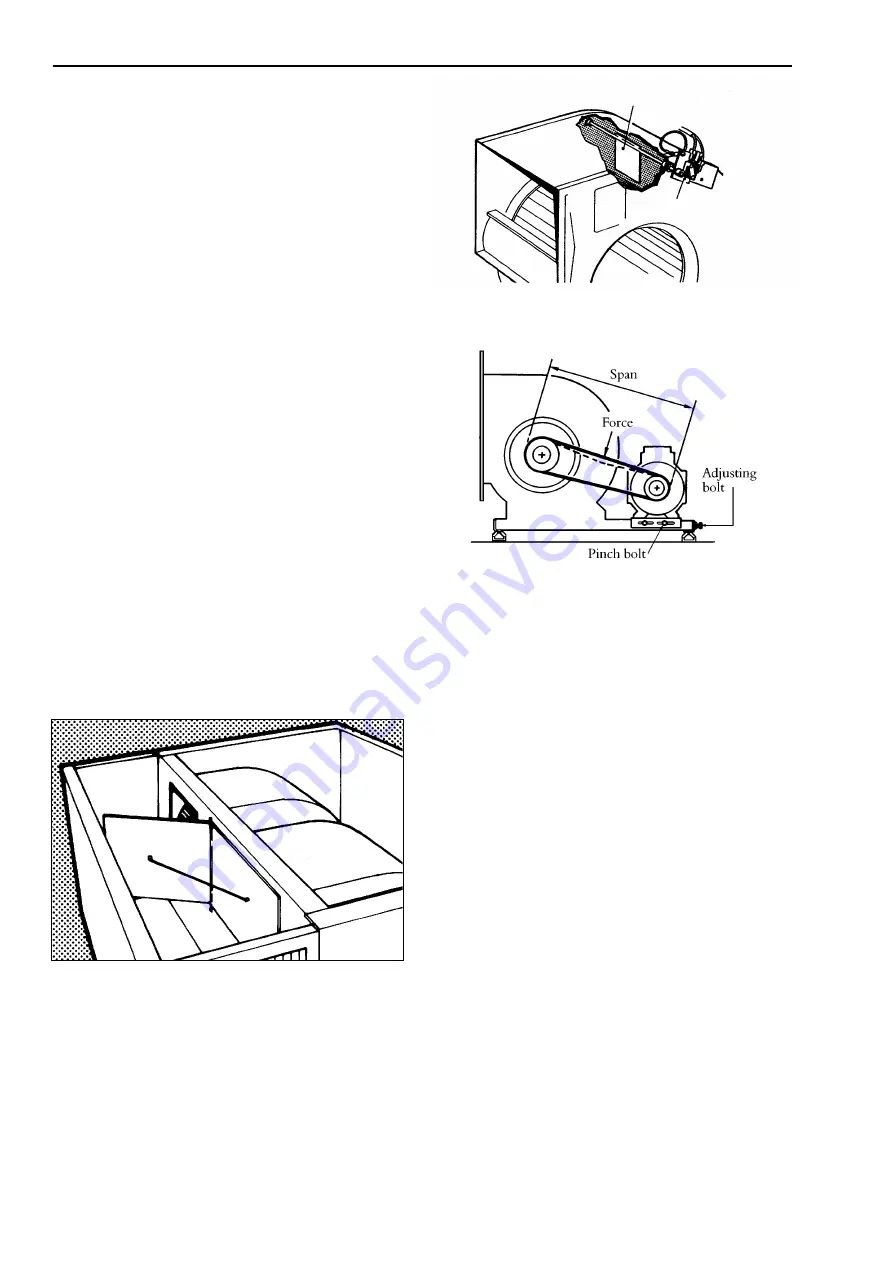
12
Installation and Maintenance
QUIETWIN QTR BELT DRIVE TWINFAN
Maintenance (continued).
CASE SIZE ‘D’ UNITS
ISOLATION
BEFORE COMMENCING WORK MAKE SURE
THAT THE UNIT AND NUAIRE CONTROL,
IF FITTED, ARE ELECTRICALLY ISOLATED FROM
THE MAINS SUPPLY.
Access to the unit internals is gained by removing the top
cover(s) Isolate the unit and inspect the following items three
months after commissioning and then once per year.
Maintenance Intervals
The first maintenance should be carried out three months
after commissioning and thereafter at twelve monthly inter-
vals. These intervals may need to be shortened if the unit is
operating in adverse environmental conditions, or in heavily
polluted air.
Motors
Brush away any dust or dirt from the motor housings and
ensure that the motor vents are unblocked.
Bearings
Lubrication is unnecessary as the motors are fitted with sealed
for life bearings.
Impellers
Remove any dust and check that the impellers are securely
fixed to the motor shafts. Take care not to disturb any balance
weights fitted. Check sealed for life bearings for excessive
wear.
Shutter Assembly
Remove any dust and check that the shutters operate freely.
and that they seal the appropriate fan outlet effectively.
Fig. 13. Quietwin shutter detail.
Anti Vibration motor plate mountings
Each motor plate is supported on ten individual resilient
mountings. Check that all the mountings are secure and in
good condition. See fig 13.
Aiflow Flapswitch for Auto changeover
Check the flag switches operate freely by locating the spindle
and flap (through the blower outlet aperture) and carefully
moving the flap. A click will be heard when the switch oper-
ates. See fig. 14.
NOTE: Do not bend the flaps.
Fig. 14 Auto changeover flap switch
Fig. 15 Tensioning the drive belts on size ‘D’ units.
Belts
All belt drive units incorporate belt tensioning devices. To
adjust the belt tension, slacken the pinch bolt on the sides of
the motor plate. Turn the adjusting bolt clockwise to tighten
the belt and counter clockwise to loosen it.
The drive should be tensioned until a slight bow appears in
the slack side of the ‘V’ belt when running under load. To
check for correct tension, proceed as follows.
1. Measure the span length (See fig. 15).
2. At the centre of the span, apply a force at right angles to the
belt sufficient to deflect one belt 16mm for every metre of
span length (see fig. 7). The force required to deflect the ‘V’
belt should be from 0.5kg to 0.8kg.
General Cleaning and Inspection
Clean and inspect the exterior of the fan unit and associated
controls etc.
Remove the access panel from the fan unit. Inspect and, if
necessary, clean the fan and motor assemblies and the interior
of the case. If the unit is heavily soiled it may be more conve-
nient to remove the fan / motor assemblies.
If NuAire controls and or remote indicators are fitted, remove
the covers and carefully clean out the interiors as necessary.
Check for damage.
Check security of components. Refit the access covers.
General
1. Check that all fixings are tight.
2. Check sealing strips around the fan outlets are tight up
against the bulkhead.
3. Check that duct connections are not leaking.
Flap and spindle
Micro switch