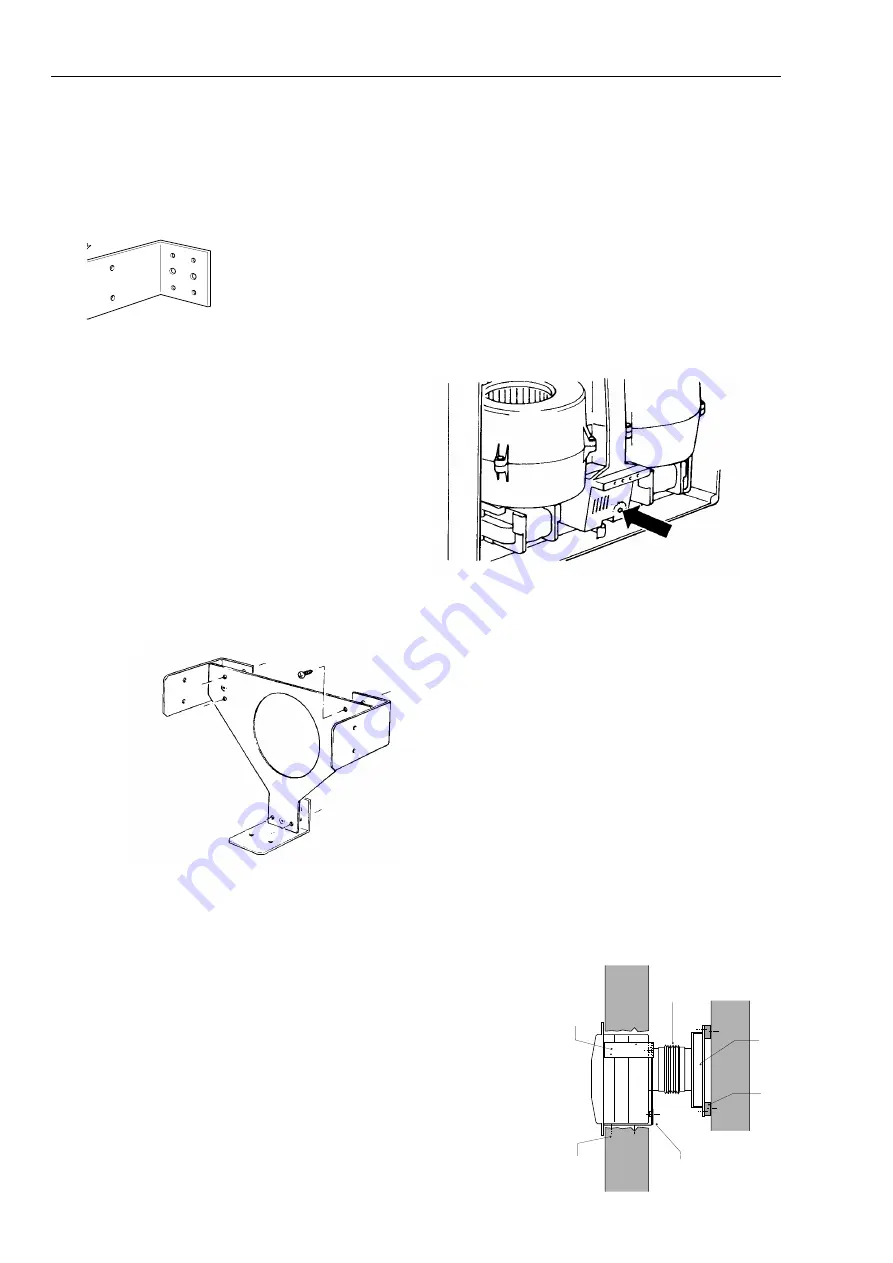
Installation and Maintenance
OPUS 12V (R rangr)
2
Installation
(continued)
It is assumed that a solid non-reverberant mounting posi
tion has been selected, and the necessary passages for
ductwork, from outlet spigot and to subsidiary inlet
spigot (if a second room is to be ventilated) as well as the
electrical connection prepared. It is also assumed that
compatible ductwork is already installed.
b)
Mounting brackets are supplied with all OPUS fans but,
depending on the type of unit, may need to be shortened.
The bracket has a series of notches, one of which is suit
able for your unit. Offer up the bracket to the unit (small
leg of bracket to back of unit) and note the notches which
correspond with the back of the skirt. Using a hacksaw
cut the bracket to length. Similarly prepare the two
remaining brackets. (Fig.3).
Attach the three brackets to the large 'Y' shaped plate
using the self tapping screws supplied to form a mounting
frame. (See fig. 4).
Position the mounting frame in the prepared aperture so
that the ends of the three cut brackets are flush with the
surface of the wall. Secure the mounting frame with suit
able fixings.
c)
Unclip and remove the fan module.
Knock out a suitable cable entry hole in the rear face of
the case.
If a second room is to be served remove the appropriate weak-
ened area from the case, and, working from the inside fit the the
subsidiary inlet spigot by passing it through the case and turning
quarter of a turn to lock in position.
d)
Offer up the casing to the mounting frame feeding the
supply cable through the entry hole. Engage the outlet
spigot(s) in the ductwork and fix the casing to the frame
using the three screws supplied.
e)
Connect the wiring to the internal terminal block / socket.
Fig.3. Selecting bracket length.
Fig. 4. Mounting frame assembly.
f)
Fit the fan module to the case, mating it's plug fully with
the internal socket. Secure in position with the two spring
clips.
g)
Fit the front cover to the unit using the four screws sup
plied. Insert the filters into the rebates in the cover.
Test / run the unit.
Adjusting the run on timer .
Remove cover. Locate the Time Delay adjustmewnt screw on
the plastic box found directly between and under the fan scroll
mouldings (see fig 5). integral with the fan module. Reset
against the graduated scale. Refit the cover.
Fig. 5. Timer adjustment.
Installing the unit into flatduct.
It is assumed that the flatduct is already fitted with a plenum
section incorporating 100mm dia. spigot in the area of the
proposed extract fan.
a)
Proceed as in steps (a), (b) & (c) above.
b)
Feed the 100mm flexible ducting (supplied) through the
rear of the mounting frame and fit to the spigot on the flat
duct plenum.
c)
Offer up the casing to the mounting frame and join the
other end of the flexible ducting to the outlet spigot using
tape (not supplied). Fig. 6.
Feed the electrical supply cable through the entry hole and
fix the case to the mounting frame using the three screws
supplied.
Continue as in (e) to (h) above.
Fig. 6 Installation
into flatducting
Mounting frame
Flexible
ducting
9" x 1"
flatduct
Timber
battens
Wall fixings
through mtg
frame
Side bracket