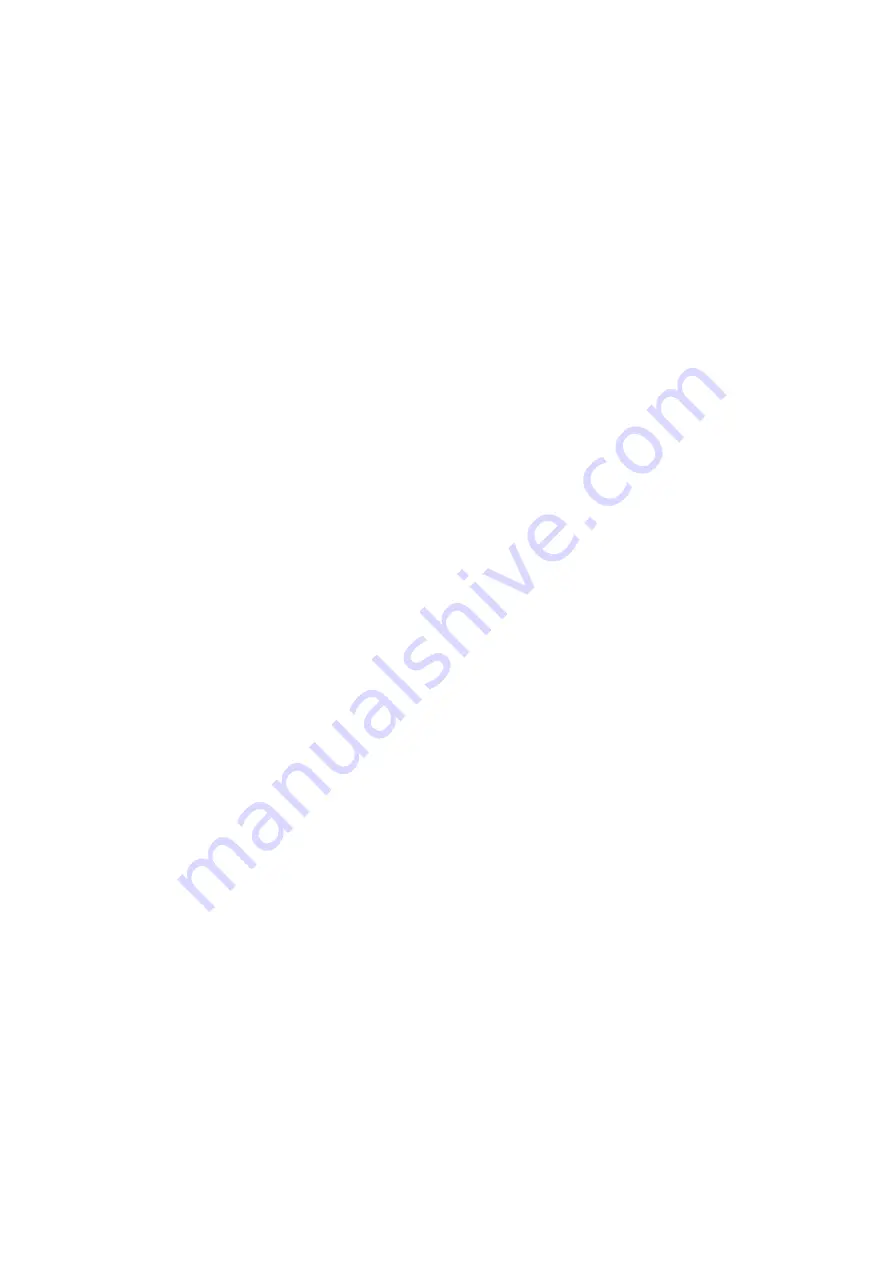
BURNER GAS CONTROLS
Low Gas Pressure Switch
The low gas pressure switch is
located on the inlet side of the gas
valve. It is required to monitor inlet
gas pressure during burner operation.
The low gas pressure switch is wired
in series with the appliance
controlling instruments and in the
event of gas pressure failure will
cause the burner to effect a safety
shut down.
Isolate the burner and remove the
gas pressure switch cover. Switch
on the electrical supply and allow the
burner to establish main flame. Slowly
turn the adjustment dial on the gas
pressure switch clockwise until the
flame is extinguished and the burner
shuts down. Turn the dial slowly
anticlockwise one division at a time
until the burner restarts and
establishes main flame. Recheck the
performance and then turn the dial a
further two divisions anticlockwise.
Switch off the burner and replace the
gas pressure switch cover.
Gas Valve Multibloc - Single
Stage (On/Off)
The gas valve is of the multibloc type
incorporating start rate, safety and
main valves and pressure governor.
Valve adjustments are detailed in the
Gas Controls and Adjustments
section.
SG10060602
Two Stage (High/Low)
The gas valve is of the multibloc type
incorporating start rate, safety and two
stage valve and pressure governor.
Valve adjustments are detailed in the
Gas Controls and Adjustment section.
FLAME MONITOR
Probe
The flame probe (flame rectification
probe) is located on the burner head
and is required to supervise the safe
operation of the burner under all
working conditions.
UV
As an option burners can be fitted
with an ultraviolet cell (UV) cell to
detect the presence of the flame.
BURNER OPERATING
SEQUENCE
Single Stage (On/Off) Burners
The operating sequence begins with
a pre-purge on full air, then start rate
gas flame which when proved allows
the burner to operate on main flame,
then to the “OFF” position after the
heat input is satisfied. The operation
is determined by demand of the
appliance control instruments.
GENERAL INSTRUCTIONS continued......
Two Stage (High/Low) Burners
The sequence begins with an air pre-
purge on full air, followed by start rate
gas flame which when proved allows
the burner to operate on High/Low/
Off. The operation is determined by
the demand of the appliance control
instruments.
FLUE AND CHIMNEY
REQUIREMENTS
The top of the Chimney/Flue should
be above all roofs within a radius of
10 metres.
Check that it is suitable for use with
gas fired appliances. Reference
should be made to Local Authority
and other regulations governing such
installations.
Ensure that the flue pipe from the
appliance does not protrude into the
chimney beyond the wall thickness
and is sealed throughout its run.
If more than one appliance is
connected to a common flue/
chimney, ensure that the cross
section of the flue/chimney is
adequate for the total volume of flue
gases from all the appliances.
PLANT ROOM VENTILATION
An adequate supply of dust free,
fresh air is required for the burner at
both high and low level in accordance
with the appropriate standards.
GAS SUPPLY
The gas supply to the burner must
be constructed and installed to
comply with local conditions and
appropriate Codes and Standards. It
should be of sufficient size to satisfy
the pressure/volume requirements of
the burner to ensure its operation.
It is essential that a 90° manual shut-
off is fitted upstream of the burner
gas train for the isolation of the burner
during servicing and maintenance.
The valve size must not be less than
the burner valve train or create
restriction to gas flow.