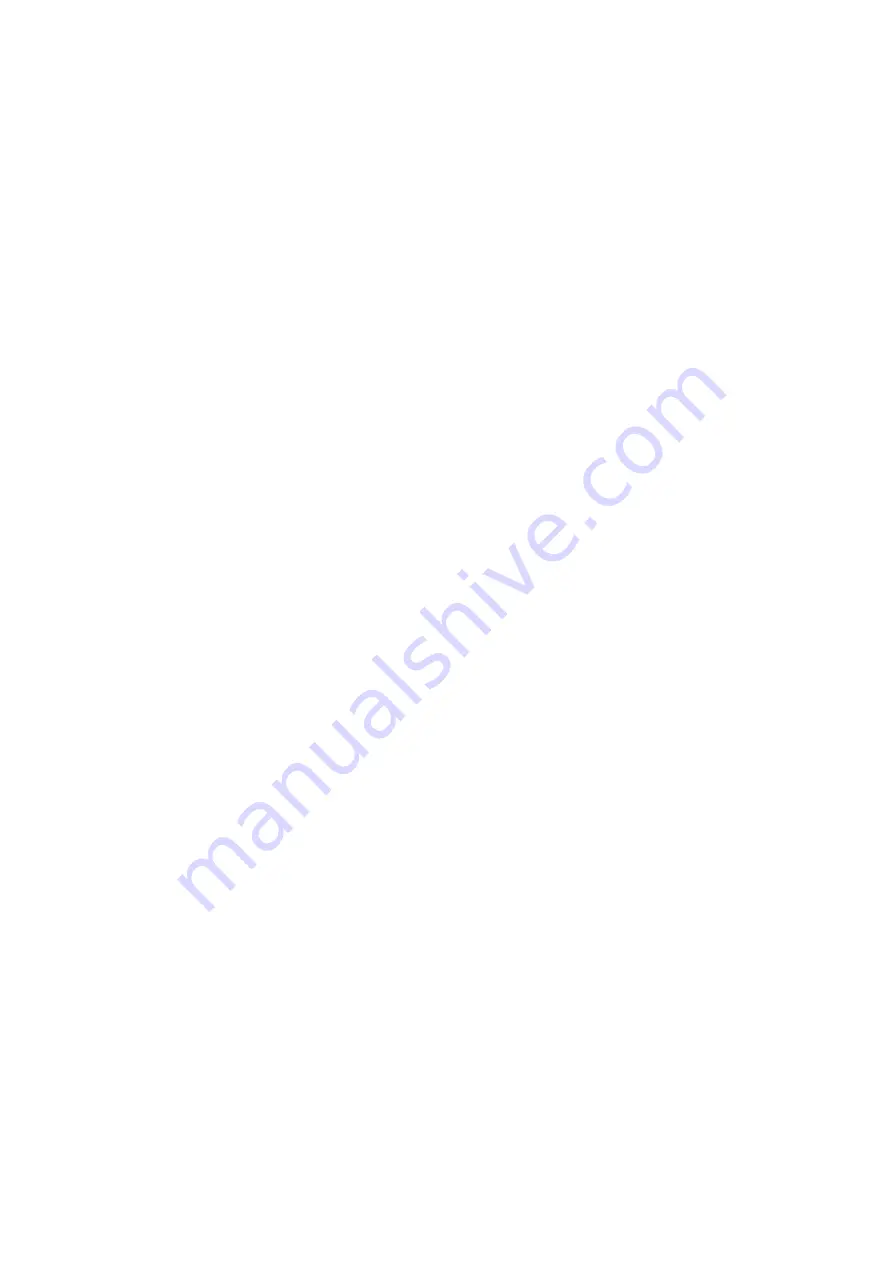
SITE CONDITIONS AND SERVICES
Flue and Chimney Requirements
It is important that:
- The flue pipe from the appliance and the joint between this flue and the chimney are sealed to
prevent leakage of combustion products.
- The flue pipe from the appliance does not protrude into the chimney beyond the inside wall.
- The top of the flue or chimney shall be higher than any roof within a radius of 10 metres.
- Checks are made to ensure that the chimney is suitable for gas and oil fired appliances and that
the proposed installation complies with all Local Authority and other regulations covering such
installation.
- The flue must be balanced at the appliance outlet.
- If more than one appliance is connected to a common flue or chimney, the cross-section of this
flue or chimney should be adequate for the total volume of combustion products from the
appliances.
Plant Room Ventilation
The burner must be supplied with dust-free air at sufficient rates for all firing conditions, in
accordance with the appropriate Standards.
Combustion Chamber Conditions
When the burner is fitted to an appliance designed to work under balanced or negative combustion
chamber pressure conditions the over-fire draught must not exceed 0.25 mbar.
Gas Supply
The gas supply pipework to the burner must be appropriate to local conditions and must be
constructed and installed in compliance with appropriate Codes and Standards. It shall be of
sufficient size to satisfy the pressure and volume flow requirements of the burner under all firing
conditions. Checks should be made to ensure that all meters and other components are
appropriately rated for the maximum gas flow rate anticipated.
It is essential that a 90° manual isolation valve is fitted upstream of the gas control train to allow the
burner to be isolated for maintenance. The size of this valve should not be less than that of the
burner control train in order to avoid any restriction in gas flow.
Gas Boosters
When a gas booster is used, the gas pressure at the booster inlet must not fall below 10 mbar under
any conditions. A low gas pressure switch must be fitted on the upstream side of the booster to
prevent it starting if the supply pressure is insufficient.
An additional pressure switch should be used to monitor the pressure downstream of the booster and
prevent the burner going to high fire if the pressure is insufficient.
The booster should be installed as near to the burner as possible. It should be noted that CE marked
burners fitted with a low gas pressure switch will not run if the gas pressure from the booster is
insufficient. This is due to the low gas switch being set to safeguard combustion quality at the high
fire setting. In this situation the booster outlet pressure switch will have no bearing on the burner
control, but can only be used to indicate booster failure.
The booster should be installed as near to the burner as possible. It should be positioned on a firm,
flat, horizontal surface using anti-vibration mountings. All connecting pipework should be well-
supported and accurately positioned in order to avoid stressing the booster casing. Flexible
connectors, which reduce both pipework stresses and transmitted noise, must be fitted. The gas
supplier should be asked to recommend the size of pipework between the meter and the booster to
ensure that the required pressure and flow are available.
MDFL 3300 & MDFL 4000 Issue 2 08/08
Page 6
Summary of Contents for MDFL 3300
Page 16: ...MDFL 3300 MDFL 4000 Issue 2 08 08 Page 15 VALVE PROVING SYSTEM LDU 11 Standard fitting...
Page 30: ...MDFL 3300 MDFL 4000 Issue 2 08 08 Page 29 MODULATING CAM BOX...
Page 43: ...Electrode Setting Details MDFL 3300 MDFL 4000 Issue 2 08 08 Page 42 All dimensions in mm...
Page 48: ...NOTES MDFL 3300 MDFL 4000 Issue 2 08 08 Page 47...