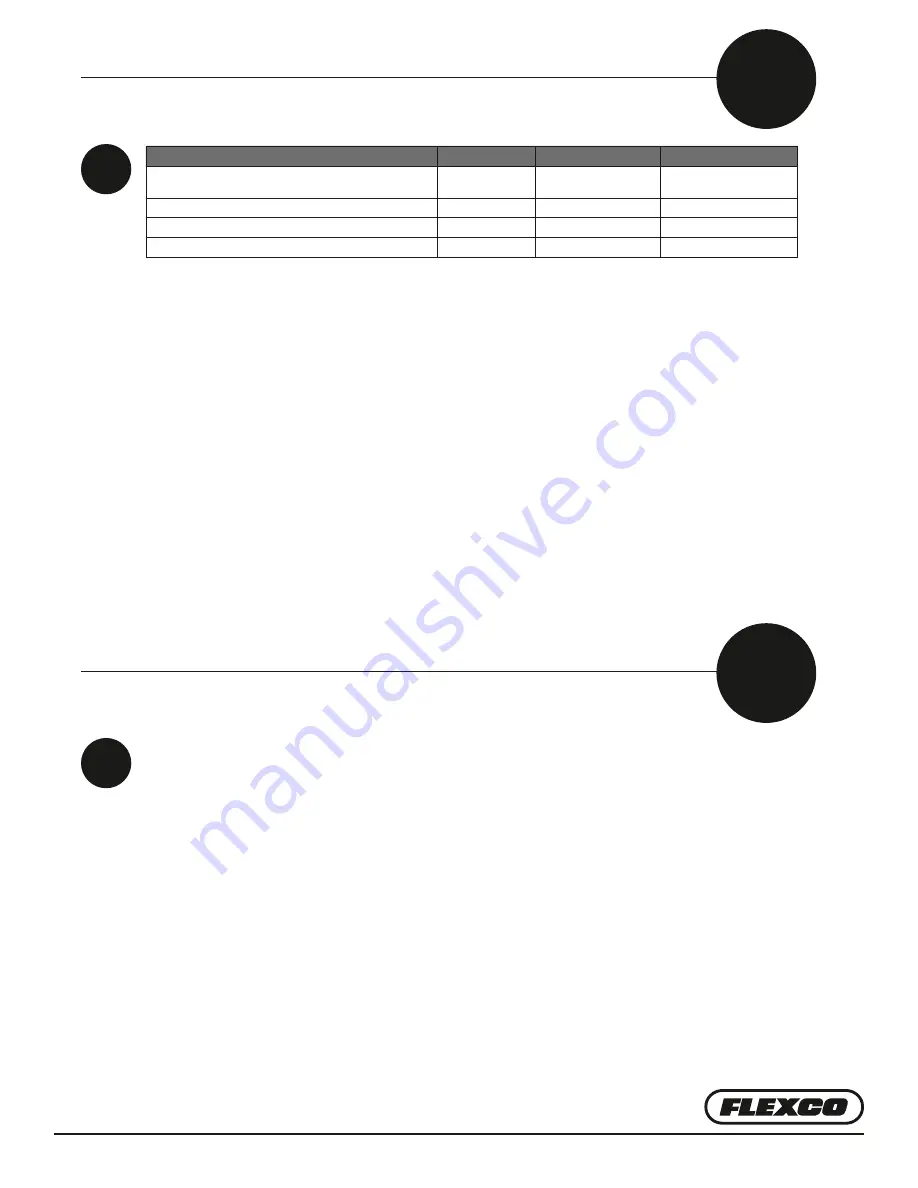
—17—
B
B1
Inspection Items
Inspection Task
Every Cycle
Every 100 Cycles
Every 1000 Cycles
Inspect press connector bolt condition and replace if condition is
degraded.
X
Inspect platen condition and clean (G2) or replace as needed.
X
Inspect extrusion and head plates for any signs of fatigue.
X
Inspect power connector pins for signs of arcing or wear.
X
To clean the top and bottom platens, place an all-purpose cleaner on a clean cloth and wipe platens.
For area requiring further cleaning use a nylon abrasive pad.
C
C1
How to Clean the Platens