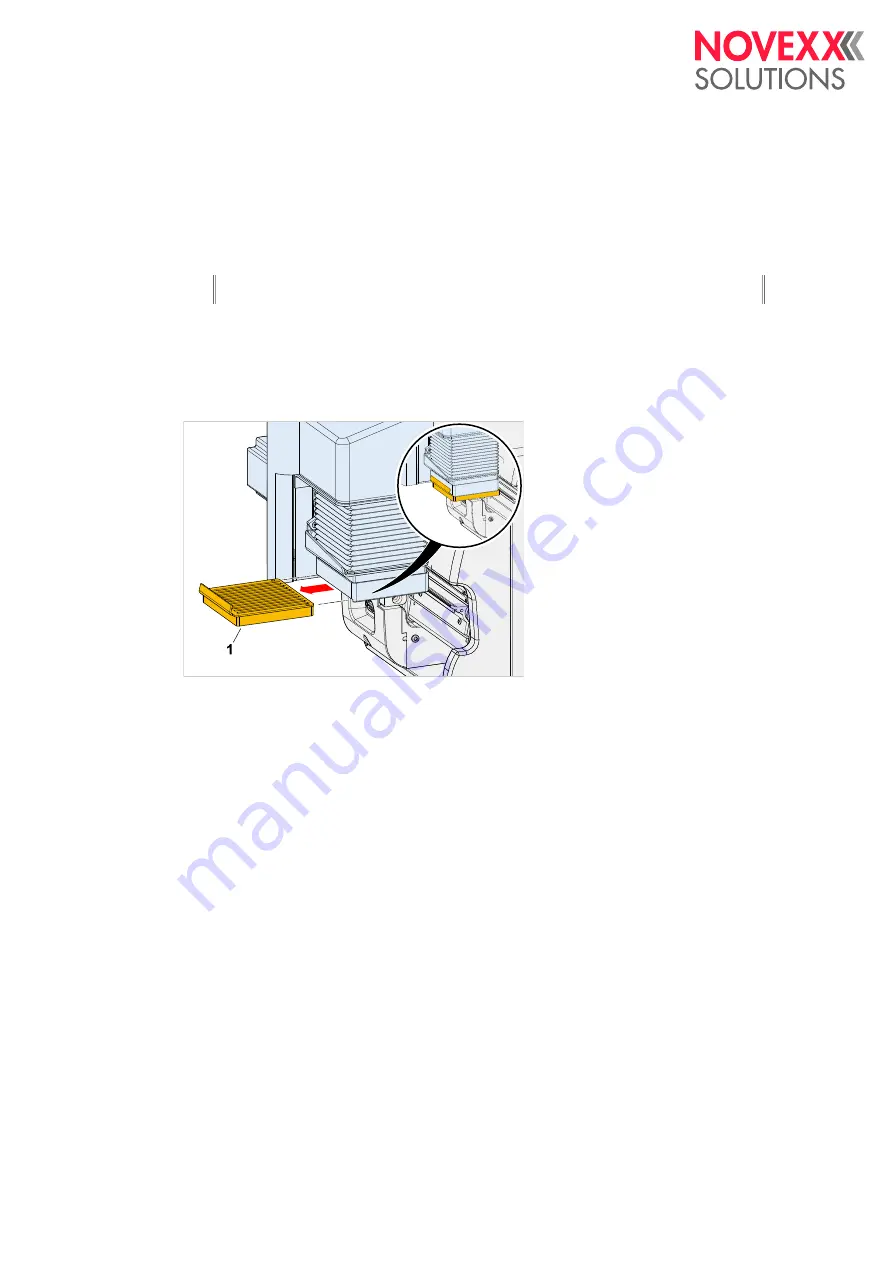
Operating manual
LTSA LTMA
REPLACING THE PRESSURE PLATE
About this task
When the foam pad on the pressure plate has become so worn that the function of the applicator is im-
paired, the pressure plate has to be replaced.
Application of labels to moving products places a greater burden on the pressure plate than applica-
tion to stationary products.
Procedure
1.
Switch off the printer.
2.
Push pressure plate (1) forwards out of the applicator foot.
3.
Insert a new pressure plate.
Item no.: A4487
REMEDYING MALFUNCTIONS
Status messages
Malfunctions in the applicator generally have one of the following causes:
• The applicator is prevented from moving
• The sensors that limit the movement of the applicator are defective, soiled or not correctly connected
• The printer is not correctly adjusted
Edition 02 - 7/2021
28
Operation / Malfunctions / Cleaning
Replacing the pressure plate