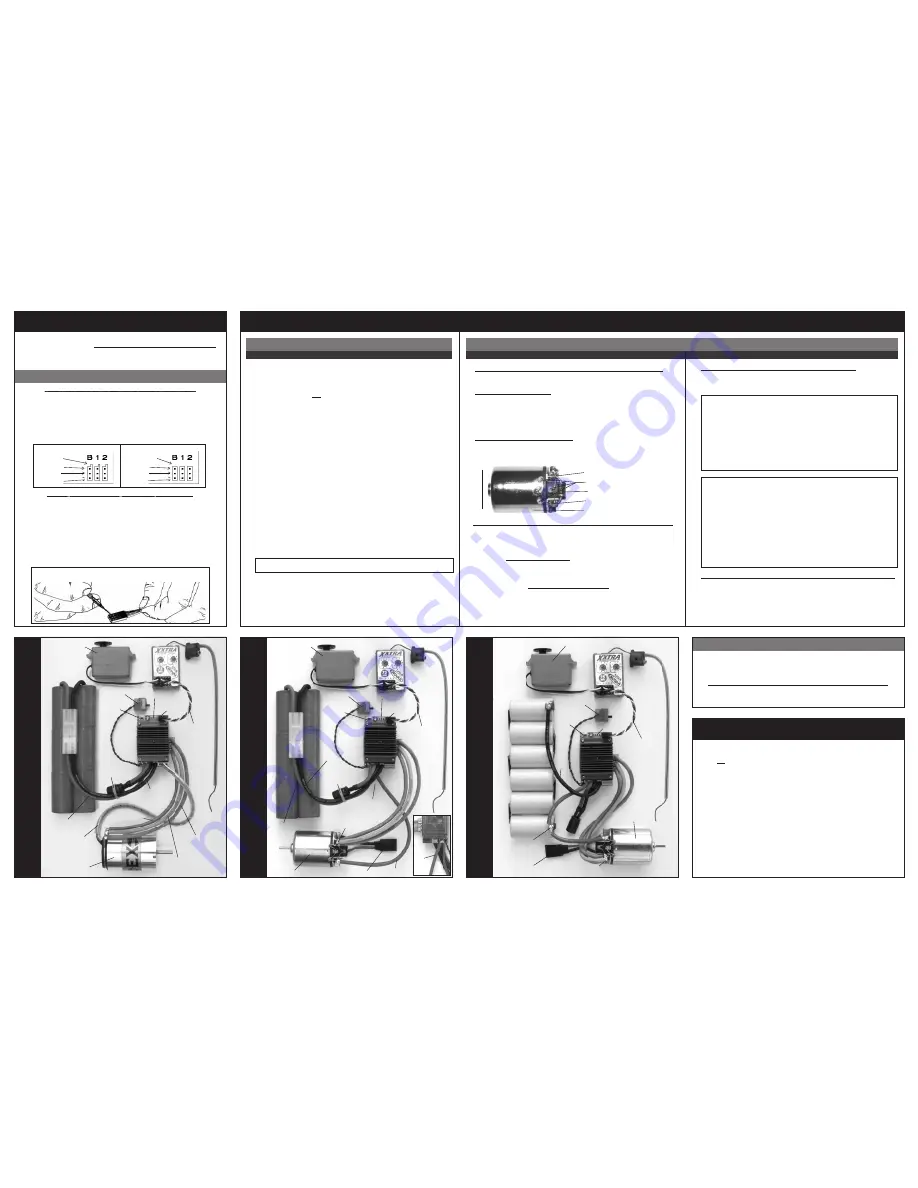
*If motor has no ground tab
(as shown here), solder the
capacitors to motor can.
The XBR Sport has the industry-standard receiver input connector on a user-
replaceable input harness &
works with all major radio brand’s new receivers
.
However, some very old receivers must have the wiring sequence in the plastic
3-pin connector housing changed.
This is important, because receiver & servo
electronics may be damaged if the sequence is incorrect.
JR • Hitec • Futaba • New KO • Airtronics Z
JR, Hitec, Futaba, new KO, & Airtronics Z receivers do not need input
harness re-wiring.
Airtronics Z receivers have blue plastic cases & new KO
cases have tabs on the input harness openings as in
Figure 1
.
• Plug one end of the input signal harness into the
THROTTLE CHANNEL (#2)
of
receiver with the
BLACK wire toward the outside edge
of receiver case.
• Plug the other end of the input harness into 3-pin header inside the ESC’s case
with the
WHITE wire toward the ‘S’ (signal) marking
on the ESC’s case above
the rectangular signal harness opening.
Old-style KO • Old-style Sanwa/Airtronics
If you have an older KO or Sanwa/Airtronics, you must change the sequence
of the ESC’s input harness wires--
Old Sanwa/Airtronics cases are black color &
Old KO cases do not have tab openings, as in
Figure 2
above.
• Using a small flat blade screwdriver,
remove the red & black wires
from the plastic
housing at the receiver end of the input harness as in
Figure 3
below.
•
Interchange the red and black wires
in the plastic 3-pin connector housing at
the receiver end of the input harness.
• Insert modified end of the harness into the
THROTTLE CHANNEL (#2)
of receiver
with the
RED wire toward the outside edge
of receiver case.
• Plug the other end of the input harness into the ESC with the
WHITE wire toward
the ‘S’ (signal) marking
on the ESC’s case.
FIGURE 3
With a small standard screwdriver, gently lift plastic prong
until wire and metal socket easily slide out of plastic housing.
changing wiring sequence
@
receiver end
FIGURE 1
FIGURE 2
New KO
(with tabs)
Old KO
(no tabs)
tabs
no tabs
black
red
red
white
black
white
P3
step
1
–
connect input harness
step
2
–
wirinG speed control, motor, & battEry
1. MOTOR CAPACITORS NOT NEEDED
Novak brushless motors do not require external motor capacitors.
2.
DO NOT USE SCHOTTKY DIODES IN BRUSHLESS-MODE
Schottky diodes must NOT be used with reversible ESCs (including brushless).
Schottky diode usage will damage the ESC & void warranty.
3. FACTORY-INSTALLED POWER CAPACITOR REQUIRED
The factory-installed Power Capacitor MUST be used with brushless &
brush-type motors.
If Power Capacitor becomes dented or damaged, ESC failure can
occur
--replace immediately
.
Longer Power Capacitor wires will decrease performance
.
4. CHECK FOR PROPER GEARING
Refer to the
‘PROPER GEAR SELECTION’
portion of the
PROGRAMMING/
GEARING
Sheet (Pg.5) to determine proper gearing & avoid overheating.
5. SOLDER MOTOR POWER WIRES TO MOTOR
*
Skip this step if installing complete system with ESC factory-wired to motor.
a.
Cut the
BLUE, YELLOW, & ORANGE
silicone motor power wires to the
desired length, and strip 1/8-3/16” of insulation from the end of each
wire. Tightly twist the exposed strands of wire, and tin the exposed end
section of each wire with solder with a good, high heat iron.
b.
Solder the ESC’s
BLUE Phase ‘A’
motor wire to the
motor’s phase ‘A’ solder
tab
. Apply heat to exposed wire with soldering iron, and add solder to
the tip of the iron & the wire--Add just enough solder to form a clean &
continuous joint from the solder tab up onto the wire.
IMPORTANT NOTE:
DO NOT OVERHEAT SOLDER TABS
Prolonged/excessive heating of solder tabs (motor or ESC) will cause damage.
c.
Solder the ESC’s
YELLOW Phase ‘B’
motor wire to the
motor’s phase ‘B’
solder tab
as described in Step 5B above.
d.
Solder the ESC’s
ORANGE Phase ‘C’
motor wire to the
motor’s phase ‘C’
solder tab
as described in Step 5B above.
Note: Make sure no wire strands have strayed to an adjacent solder tab, this will
result in short-circuiting & severe ESC damage, which will void the warranty.
6. CONNECT MOTOR’S SENSOR HARNESS TO ESC
Insert the 6-pin connector on the end of the motor’s Teflon sensor wires
into ESC’s sensor harness socket--the connector is keyed and will only go
together in one direction.
Spiral wrap can be used to protect sensor wires.
7. CONNECT SPEED CONTROL TO BATTERY PACK
Connect the speed control’s Tamiya-style JST battery connector to a charged
4 to 7 cell
(1.2VDC/cell)
or 2-cell LiPo battery pack.
step
3
–
ESC MOUNTiNG
Mount ESC with power wires away from other electronics & moving parts.
Select a location that allows airflow through heat sinks--
If the ESC gets air
flow, it will run cooler; and that means it will be more efficient, and you will go faster!
1. MOUNT SPEED CONTROL IN VEHICLE
Use the included double-sided tape to mount ESC in vehicle
(do not glue)
.
Avoid contact with side walls or other components to minimize vibration
.
Be sure receiver & antenna are mounted as far from ESC, power wires, battery,
& servo as possible--these components all emit RF noise when throttle is
applied. On graphite or aluminum chassis vehicles, it may help to place
receiver on edge with crystal & antenna as far above chassis as possible.
Note: Mount antenna as close to receiver as possible--trail any excess wire off top
of antenna mast (cutting or coiling excess antenna wire will reduce radio range).
2. SECURE POWER CAPACITOR TO CHASSIS
Use included double-sided tape, or a tie-wrap, to mount Power Capacitor
to the vehicle’s chassis or shock tower.
Capacitor can also be tie-wrapped
along the power wires--this requires less space on the chassis
.
3. INSTALL ON/OFF SWITCH
Use a screw or the included double-sided tape, and mount the switch
where it will be easy to access--be sure to select a position where it will
not get damaged or get switched OFF during a crash or roll-over.
NOvak bRuSHlESS mOtOrS
(Fig.4)
Amber LED flashes 4 times at start-up when transmitter signal is present
bRuSH-typE mOtOrS
(Fig.5-8)
Red LED flashes 4 times at start-up when transmitter signal is present & ESC is is Brush-Mode
1. DISCONNECT BRUSHLESS MOTOR SENSOR HARNESS
The XBR automatically switches to Brush-Mode when the ESC power is switched
ON and no brushless sensor harness is connected.
2. MOTOR CAPACITORS
Electric brush-type motors generate RF noise that causes interference. The
included 0.1µF (50V) non-polarized, ceramic capacitors must be used on all
motors to reduce motor noise & prevent ESC damage.
Note: Some motors come with built-in capacitors. If your motor only has 2 capacitors,
you need to install a capacitor between the positive & negative motor tabs––If you
experience radio interference with built-in capacitors only, install external ones.
Solder 0.1µF (50V) capacitors between:
• POSITIVE (+) & NEGATIVE (–) motor tabs.
• POSITIVE (+) motor tab & GROUND tab*.
• NEGATIVE (–) motor tab & GROUND tab*.
Negative (–) motor tab
0.1µF Capacitors
Schottky diode
Positive (+) motor tab
Ground / motor can
3. INSTALLING OPTIONAL SCHOTTKY DIODE
(Brush-Mode Only)
The XBR Sport does not require an external Schottky diode under most brush
motor conditions.
Note that an external Schottky will optimize the ESC’s braking
and motor performance in applications with heavy or repeated braking
(lap after
lap)
, or when using lower turn modified motors.
• If using an axial lead Schottky diode as shown in the photo above
(older Novak
style--35V/8A min.)
, solder lead
CLOSEST to the silver stripe
on the Schottky
diode’s body to the
POSITIVE (+) Motor Tab
. Solder the lead
OPPOSITE the
silver stripe
on the body to the
NEGATIVE (–) Motor Tab
.
• If using the Novak Racing Schottky Motor Module
(this is the best performing
Schottky diode available)
, solder the
RED wire
from the module to the
POSITIVE
(+) Motor Tab
. Solder the
BLACK wire
from the Schottky module to the
NEGATIVE (–) Motor Tab
.
If Schottky diode is installed backwards it will be destroyed. Replace only with
Schottky diodes with a minimum rating of 35 volts/8 amps.
FIGURE 5
4. SPEED CONTROL’S RED WIRE CONNECTION
To use the XBR Sport with brush-type motors, the
RED
power wire going to
Battery POSITIVE (+)
, must also go to the
POSITIVE (+) Motor Tab
. There
are two ways of doing this, as decribed below:
This method allows you to continue using stick pack batteries with the factory-
installed connector, but can also be used with hard-wired installations. (Figure 6)
a.
Strip about 1/4” of insulation from the end of the included extra piece
of
RED
silicone power. Tin the exposed section of wire with solder.
b.
Solder this wire to the bottom of the ESC’s
Battery POSITIVE (+)
solder
tab
, as shown in Figure 7 inset photo.
Be sure no strands of wire or
solder short-circuit over the gap to the battery negative solder tab.
c.
Determine the proper length for this new
RED
power wire to reach the
POSITIVE (+) Motor Tab
and cut it to this length. Strip & tin the end
of the wire and solder it to the POSITIVE (+) Motor Tab.
This method requires a hard-wired installation & has lower voltage losses. (Figure 7)
a.
Strip 1/4-3/8” piece of insulation from the mid-section of the ESC’s
RED
silicone power wire where you will solder it to either
Battery Pack
POSITIVE (+)
or the
POSITIVE (+) Motor Tab
(whatever component is
in the middle)
. Tin the exposed section of wire with solder.
b.
Solder the exposed section of the ESC’s power wire to
Battery Pack
POSITIVE (+)
or the
POSITIVE (+) Motor Tab
(component in middle)
.
c.
Strip & tin the end of the ESC’s
RED
power wire
(after the first
connection)
, and solder it to the final component--either
Battery Pack
Positive (+)
or the
Positive (+) Motor Tab
.
D.
Strip & tin the end of the ESC’s
BLACK
power wire, and solder it to
Battery Pack Negative (–)
.
5. PREP & SOLDER ESC’S BLUE, YELLOW, & ORANGE WIRES
With brush-type motors, the XBR Sport’s
BLUE, YELLOW, & ORANGE
motor
phase power wires must all go to the
NEGATIVE (–) Motor Tab
.
a.
Strip 1/4” of insulation from the end of the
BLUE, YELLOW, & ORANGE
motor phase wires. Twist & tin the end of each of the wires.
b.
Solder all of the motor phase wires (
BLUE, YELLOW, & ORANGE)
to the
NEGATIVE (–) Motor Tab
.
If you are going to use connectors, we suggest low-loss connectors
(do not use crimp type)
like
Dean’s Ultra. To prevent cross-connection of motor phase wires, we do not recommend
using connectors on the motor power wires of sensor-based brushless motors.
• Use polarized connectors. Reverse voltage will damage the ESC & void warranty.
• Use a female connector on battery packs to avoid shorting.
When wiring the vehicle’s electronics, short wires & clean/neat installations will give
you better performance, higher efficiency, & less radio problems (glitching, etc.). Try
your best to keep power wires away from signal wires & receiver/antenna.
BRUSH-MODE SET
-UP PHOTO 1
‘Y’ Method (FIGURE 6)
BRUSHLESS-MODE SET
-UP PHOTO
(FIGURE 4)
BRUSH-MODE SET
-UP PHOTO 2
Single W
ire Method (FIGURE 7)
Blue, Yellow, and Orange motor phase
wires connect to motor negative
ON/OFF
Switch
User-replaceable
input signal
harness (Ch.2)
Black power wire
(batter
y negative)
Trail excess wire off top of antenna mast
Red power wire
(battery positive)
Blue power wire
(motor phase ‘A’)
(–)
(+)
4 to 6 cell batter
y pack or 2-cell LiPo
Yellow power wire
(motor phase ‘B’)
Orange power wire
(motor phase ‘C’)
Sensor Harness
bundled with
spiral wrap
Servo plugged into
steering ch. (#1)
Novak sensor-based
brushless motor
down to 8.5 turns
P2
‘Y’ connection of
Red power wire
(battery & motor)
brush-type motor
One-Touch
button
Power Cap
tie-wrapped
to wires
Racing Schottky Module
Blue, Yellow, and Orange motor phase
wires connect to motor negative
(–)
(+)
brush-type
motor
(–)
(+)
Racing Schottky
Module
In-Line connection
of Red power wire
(battery & motor
positive)
‘y’
wiring method
single wire method
CONNECTORS & wiring hintS
Status LEDs
Fan power
output pins
(–)
(+)
ON/OFF
Switch
User-replaceable
input signal
harness (Ch.2)
Black power wire (batter
y negative)
Red power
wire (battery
positive)
(–)
(+)
4 to 6 cell batter
y pack or 2-cell LiPo
Servo plugged into
steering ch. (#1)
One-Touch
button
Power Cap
tie-wrapped
to wires
Status LEDs
Fan power
output pins
ON/OFF
Switch
User-replaceable
input signal
harness (Ch.2)
Black power wire (batter
y negative)
Trail excess wire off top of antenna mast
4 to 6 cell batter
y pack or 2-cell LiPo
Servo plugged into
steering ch. (#1)
One-Touch
button
Status LEDs
Extra Red wire soldered to tab
Extra Red wire
soldered to motor