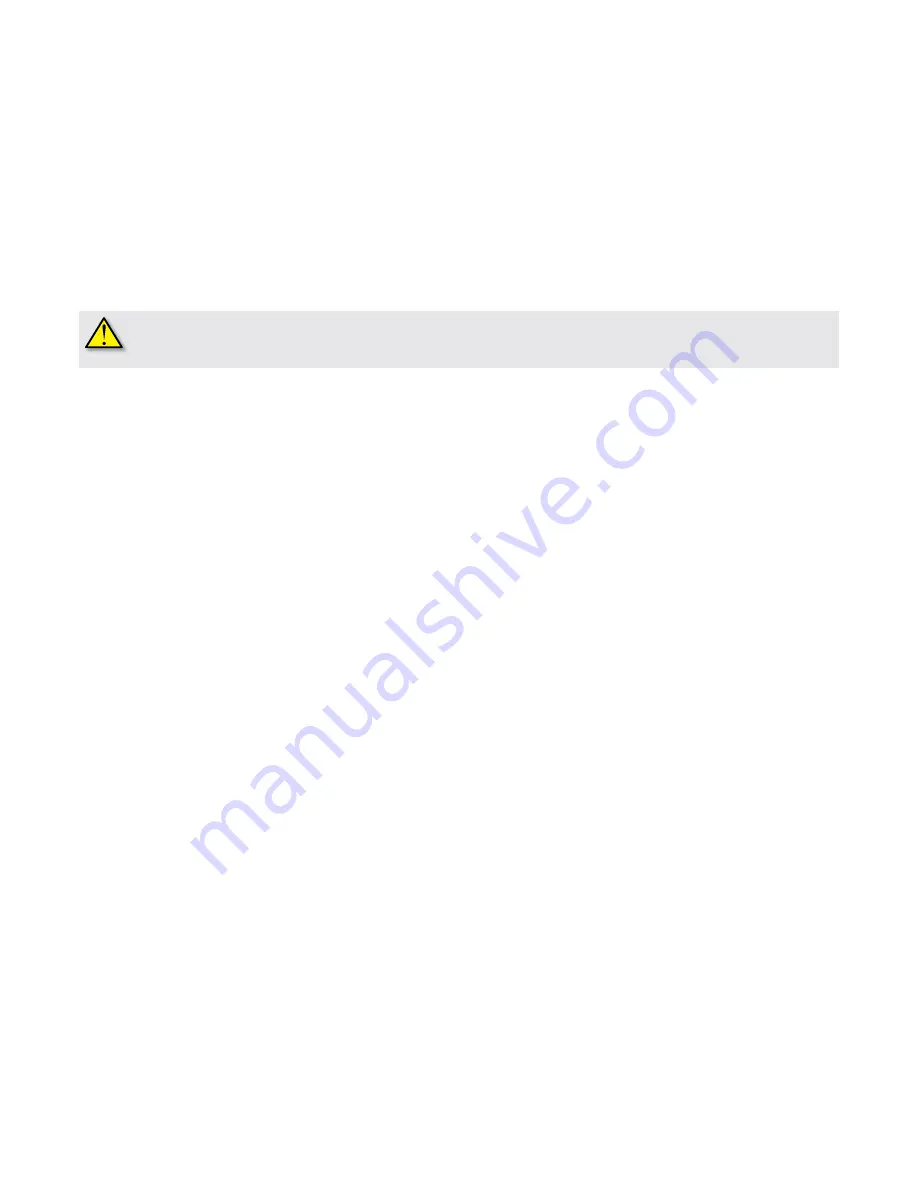
25
3.2.10.
Power mains connections
The boiler is supplied with a three-poled power cable, already connected to the electronic board and it is provided with an anti-ruptu-
re firming clamp.
The boiler is to be connected to a 230V-50Hz electric power supply.
Comply with phase / neutral polarity sequence when power connecting the boiler.
Installation standards must be complied with and they are considered as an integral part of this booklet.
An easily accessible two-poled switch, with a minimum 3 mm distance between contacts, is to be installed outside of the boiler. The
switch is to allow power supply cut-off in order to safely perform maintenance and service procedures.
Power supply to the boiler must be fitted with a differential magnetic-thermal automatic switch of suitable disconnection capacity.
Electric power supply must be properly earthed.
The above mentioned safety measure must be verified. If in doubt, ask a qualified technician to thoroughly check the power network.
WARNING
The manufacturer shall not be held responsible for any damage due to failure in grounding the system: gas,
hydraulic, or CH system pipes are not suitable for grounding power networks.
3.2.11. Room thermostat connection (optional equipment)
The boiler is designed to be connected to an ambient thermostat (not supplied with the boiler).
Room thermostat contacts must be properly sized in compliance with a load of 5 mA load at 24 Vdc.
Ambient thermostat wiring must be connected to the relevant terminal board (see electric layout), after removing the
jumper supplied as standard with the boiler.
The ambient thermostat wirings are NOT to be grouped together with power mains supply cables.
3.3. Loading the system
Once all boiler connections have been completed, CH system can be filled.
The procedure is to be cautiously carried out, following each step:
- open the air purging valves on all radiators and verify the boiler automatic valve operation;
- gradually open the relevant loading tap (pic. 2), checking all automatic air purging valves installed in the system properly work;
- close all radiator air purging valves as soon as water starts coming out;
- check boiler water pressure gauge not to exceed 1 / 1.3 bars reading;
- shut the loading tap and bleed any air out again, by opening the air bleeding valves on radiators;
- start the boiler and bring the system to working temperature, stop the boiler and wait for the pump to stop, then repeat the air blee-
ding procedures;
- allow the system to cool and restore water pressure to 1 / 1.3 bars.
WARNING
As far as domestic heating systems treatment of water is concerned, in order to optimize performance and safety, to
preserve these conditions over time, to ensure long-lasting regular operation of auxiliary equipment as well, and to minimize
energy consumption, thereby integrating current local laws and standards it is advisable to use specific products that are
suitable for multi-metal plants.
WARNING
The safety low water pressure switch will not give electric consensus to the burner turn on procedure when water pressure
is below 0,4/0,6 bar. CH water pressure is not to be less than 0,8/1 bar. Restore proper value as needed, via the loading tap
which is provided as standard with the boiler (pic. 2). The procedure is to be followed while the system is cold. The pressure
gauge fitted on the boiler control panel indicates the pressure in the CH system.
WARNING
After long inactivity of the boiler has its pump may be stuck. Before starting up the boiler, make sure that the pump is operati-
ve, by the following procedure:
- remove the boiler casing;
- unscrew the protective cap at the centre of the pump motor;
- put a screwdriver into the hole and manually rotate the pump shaft clockwise;
- once the unblocking operation is completed, screw the protective cap back on and check for water leaks.
When the protection cap is removed, some water may flow out. Before re-installing the boiler casing, make sure all internal
surfaces are dry.