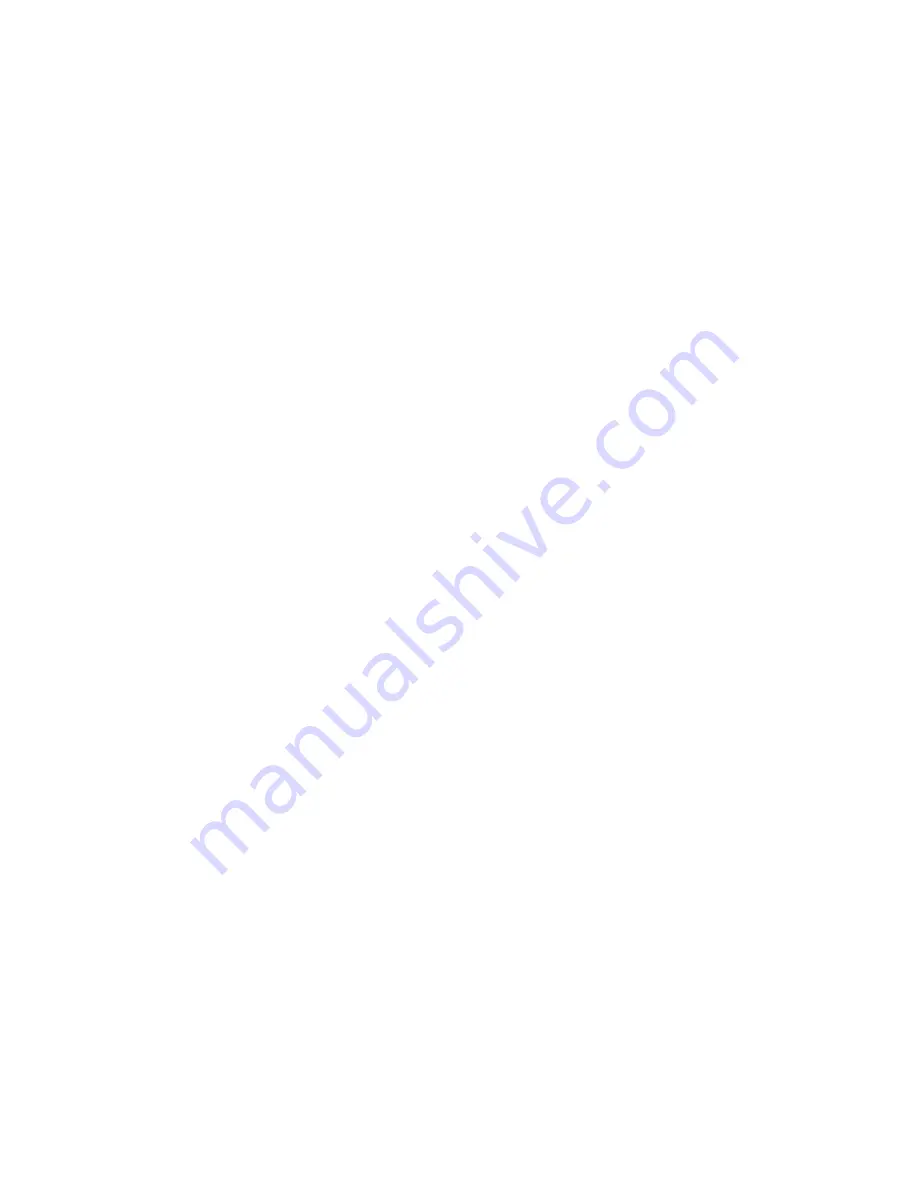
6
1.2. Operating the boiler
1.2.1. Switching on
• Open the gas stop cock
• Connect power mains to the boiler (no. 1 light on control
panel turns on)
• Choose boiler mode by setting no. 9 knob (pic. 1)
• Choose to activate or de-activate the AQUA PREMIUM
system through no. 13 switch (pic. 1)
• Adjust CH water temperature through no. 11 knob (pic. 1)
• Adjust DHW temperature through no. 10 knob (pic. 1)
• Set room temperature by means of the room thermostat
(when available)
• When CH is required, no. 8 light comes on (pic. 1)
WARNING:
should the boiler be left inactive for a long time,
particularly when boiler is fired by LPG, ignition might be
difficult. Before starting the boiler, switch on a different gas
fired device (e.g. kitchen range, oven, etc.). Beware that
even by following this procedure, the boiler might still expe-
rience some starting difficulties and shut down once or
twice. Reset boiler by acting on no.9 knob (pic. 1).
1.2.2. Operation
CH water temperature can be adjusted within a 35°C to
78°C range.
In order to prevent too frequent ON and OFF ignition se-
quences in CH mode, the boiler has a 4 minute waiting time
between subsequent ignitions. Should water temperature
in the system fall below 40°C, waiting time procedure is
cancelled and boiler reignites.
Boiler electronics always gives priority to DHW demand
over CH water supply.
DHW temperature can be adjusted within a 35°C to 57°C
range.
The boiler is equipped with patented AQUA PREMIUM sy-
stem.
1.2.2.1. AQUA PREMIUM system
The boiler is equipped with a 25 l. stratification water tank
and a secondary plate heat exchanger.
The boiler can either function as a standard instantaneous
boiler, when the water tank is deactivated, or through the
innovative AQUA PREMIUM system when the water tank is
switched ON.
Water tank activation and deactivation can be operated by
the user via the switch on the control board (no. 13 in
pic. 1).
When the water tank is switched ON (AQUA PREMIUM
mode), the flow switch detects the water stream from the
water mains; the boiler ignites, the cut-off valve is opened
and the DHW pump is turned ON (the pump flow rate is
fixed).
When DHW demand is smaller than DHW pump flow rate,
DHW to the tap is supplied by the secondary exchanger
only and the excess DHW produced is deviated to the wa-
ter tank.
When DHW demand is larger than DHW pump flow rate,
DHW produced by the secondary exchanger is joined by
DHW from the water tank; the combined DHW flow rate is
larger than the one that can be produced by instantaneous
boilers of identical thermal output or standard system boi-
lers with same capacity water tank.
The boiler can also be operated as a standard instanta-
neous boiler, when the water tank is disabled.
1.2.2.2. Instantaneous DHW production
While the water tank is disabled, the boiler operates as a
standard instantaneous boiler: the cut-off valve is closed
and the DHW pump is always off. In this instance DHW
supply is granted by the secondary heat exchanger only
and maximum available DHW flow rate depends exclusi-
vely on the boiler thermal output.
DHW flow rate in liters per minute relies upon the boiler
thermal output and water mains supply temperature, ac-
cording to the following formula:
K
l = DHW in liters per minute = --------
∆T
K represents:
- 341 for BTFS 24 model
- 407 for BTFS 28 model
- 449 for BTFS 32 model
∆T = DHW temperature – water mains supply temperature
E.g. In BTFS 24 model, should water mains supply tempera-
ture be 8°C and DHW required to 38°C, the value of ∆T is:
∆T = 38 °C – 8 °C = 30 °C
and DHW liters per minute available at the required tempe-
rature of 38°C are:
341
l = ----------- = 11,4 [liters per minute] (mixed water to the
30
tap)
The boiler is fitted with anti-freezing protection system,
which is active in all boiler operation modes.
When CH water temperature sensor detects a water tem-
perature of 5°C the boiler turns on to minimum thermal ou-
tput until the temperature of CH water reaches 30°C or 15
minutes have elapsed.
Should the boiler shut down, pump operation is still gran-
ted.
Please Note: the anti-freezing function only protects
the boiler and not other components of the heating sy-
stem.
CH heating system protection is to be achieved via a
room thermostat, which is disabled when no. 9 knob
(pic. 1) is set to the anti-freezing position.
CH system can be effectively protected from frost by means
of specific anti-freezing addictives suitable in multi-metal
systems. Do not use automotive anti-freezing products,
and periodically check anti-freezing additive effectiveness.
The anti-freezing function also protects the water tank.
When the water tank temperature sensor detects a water
temperature of 5°C the boiler turns on to minimum thermal
output until the temperature in the water tank reaches 10°C
or 15 minutes have elapsed.
Should the boiler shut down, pump operation is still gran-
ted.
Should the boiler be inactive and connected to power
mains, the pump and cut-off valve are operated for 6 se-
conds each 24 hours, in order to prevent blockage.