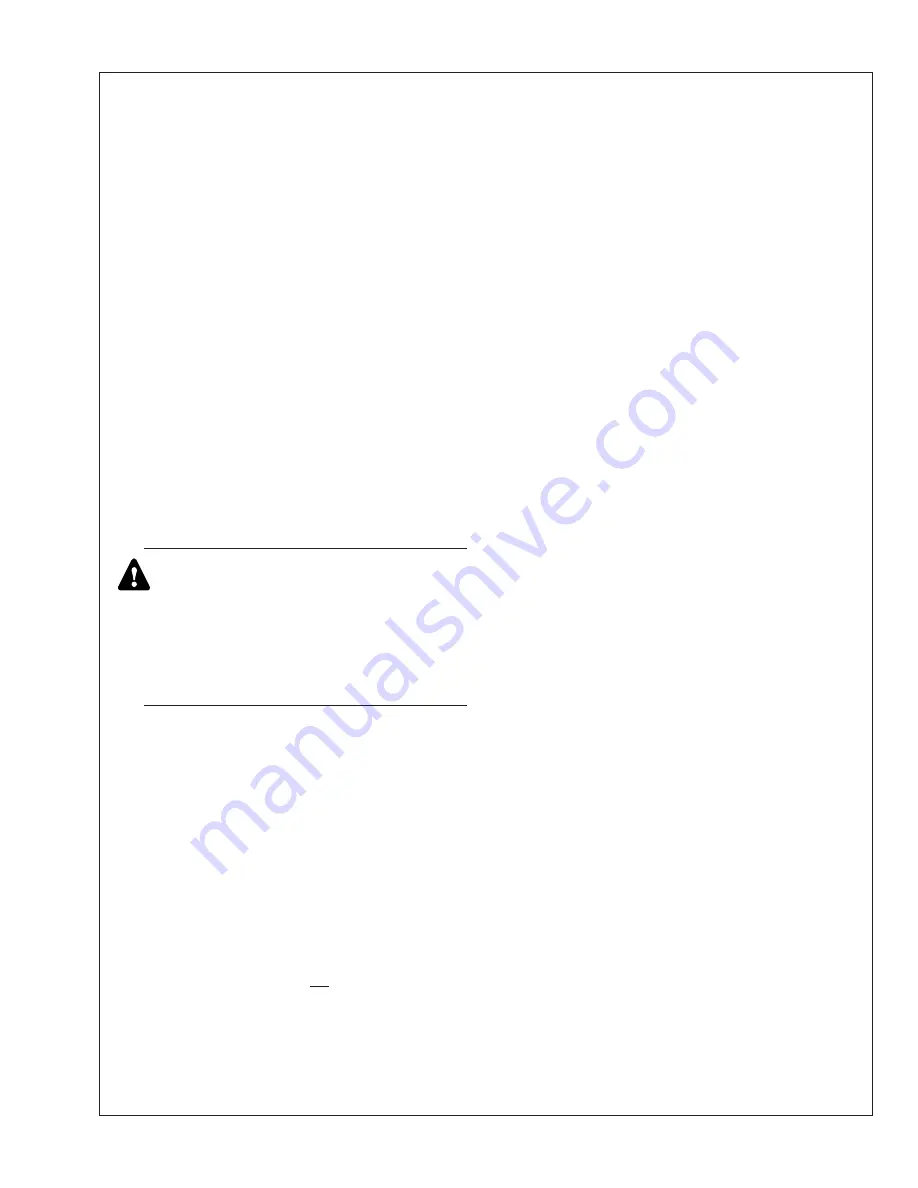
OM944T 2/11
23
Servicing
SP14. TURBOCHARGER
1. Check
for air leaks every 250 hours. Air leakage will
lower engine output and may cause black exhaust
smoke and soot.
2. Listen along air line while the engine is running. A
whistling or hissing sound indicates leakage.
3. Leakage on the pressure side, between turbo and
engine, can be found by applying soapy water to the
air line.
4. Tighten the hose clamps and replace hoses or gaskets
as required.
5. Check to see that the lubrication and cooling lines
are tight and without leaks.
COOLING SYSTEM - GENERAL
NOTE: Be sure to close the sea-cock before working
on the engine cooling system.
CAUTION: The cooling water in the engine
reaches extremely high temperatures. You must use
extreme caution when working on hot engines to
avoid burns. Allow the engine to cool before
working on the cooling system. Open the fi ller
cap carefully, using protective clothing when the
engine is warm.
SP16. CHECK THE COOLANT LEVEL
1. Check the coolant level each day before starting the
engine.
a. Check the water level by removing the pressure
cap from the expansion tank. In order to give the
cooling water an opportunity to expand, the level
should be about 1 in. (2.5 cm) below the fi ller cap
sealing surface when the engine is cold.
b. Soft water with about a pH about 6.5 to 8.5
combined with an antifreeze in a 30% to 50%
(maximum) solution should be used.
c. The antifreeze should not contain amine, silicate,
or
borate.
SP17. COOLING SYSTEM FLUSHING
1. Flush the cooling system every 2000 hours or every
12 months, whichever comes fi rst.
2. Remove fi ll cap and open drains on engine block.
The engine block drain is on the service side of the
engine above the dipstick, next to the fl ywheel
housing.
3. Pour clean water into the engine until water coming
from engine is clear of discoloration. Close drains
and refi ll the engine with recommended coolant
mixture.
4. Use 50% water / 50% (maximum) ethylene glycol
antifreeze mix. Antifreeze mixture is recommended
as a good year-round coolant.
5. Coolant capacity is approximately 3 gal. (11.4
liters).
6. Check hoses and connections and repair any
leakage.
7. Start the engine and check for leaks. Run the engine
for fi ve minutes, then shut it down. Let engine cool,
and then check the coolant level in the engine. Add
coolant as needed.
NOTE: Be sure to open the sea-cock after working
on the engine cooling system and starting the
engine.