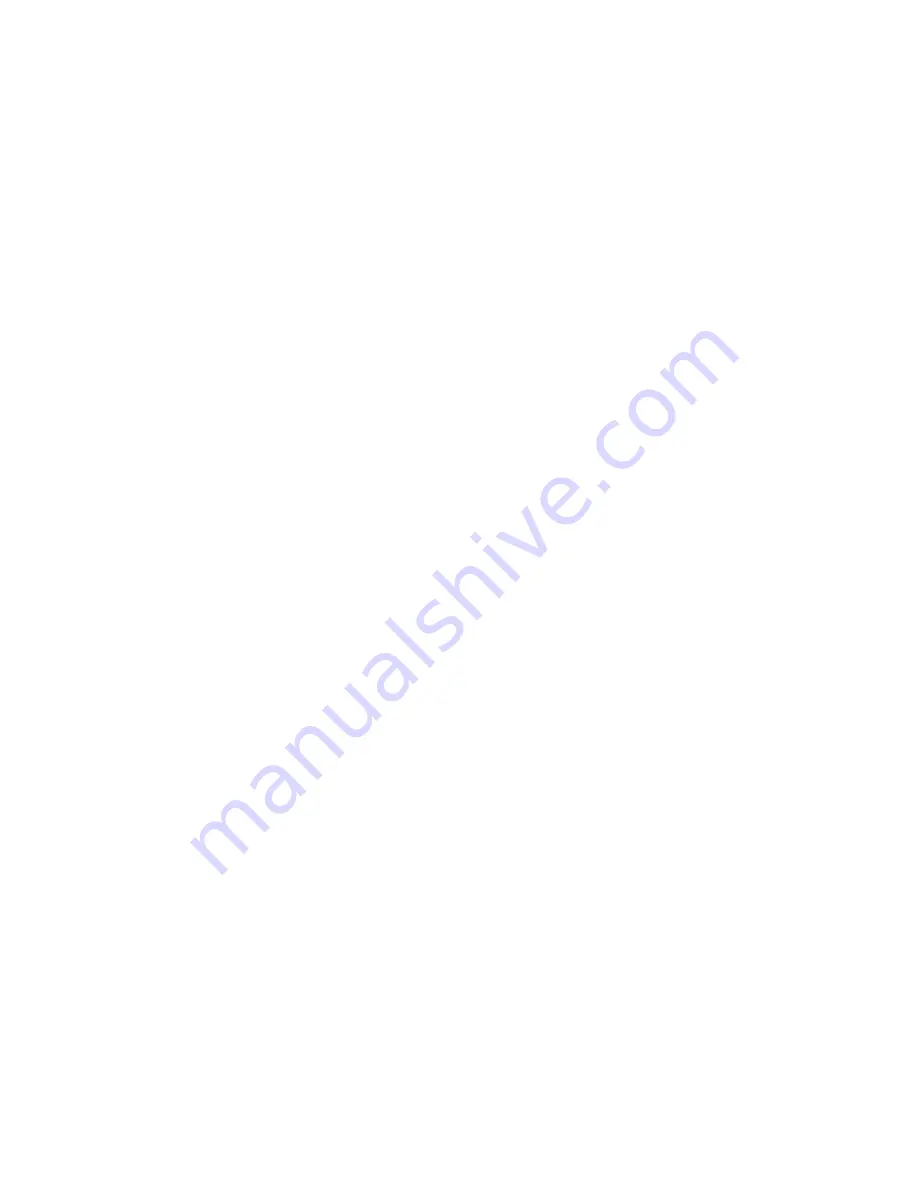
9
Built in aluminium profile, the frame is light and resistant.
Cutting head (3)
Jig-welded steel console. Console supports the electric motor and the blade guard. The balancing of
the cutting head is achieved using a heavy-duty spring. A depth-locking device fixed to cutting head
and frame enables the operator to set the cutting head to desired or to maximum cutting depth.
Blade guard (4)
Jig-welded steel construction with 350mm-diameter blade capacity, which offers maximum operator
protection and increased visibility of the work piece. Incorporated in the blade guard is an outer
metal cover, which can be easily hinged opened. This allows easy access to shaft for inspection and
blade replacement when motor is switched off, while fully protecting the blade when in operation.
Down feed and cutting depth adjustment (5)
The spring-loaded cutting head, activated by hand with the grip on the blade guard ensures smooth
lowering of the cutting head for shock-free penetration of the work piece and improved control of the
cutting pressure.
Conveyor cart (6)
Large, heavy-duty conveyor cart fitted with water flow-control vents, mounted on 4 rollers to give
maximum stability and smooth movement. The conveyor cart is equipped with graduated scale on
the backstop and with a guide-a-cut device.
Water cooling system (7)
The coolant system comprises:
•
A powerful, submersible electric water pump.
•
Plastic suction pipe delivering the water from the water pan to the cutting head.
•
A removable large capacity aluminium water pan supplied with drain plug.
•
A water-tap, fitted to the blade guard, permitting controlled water flow.
•
Two water nozzles located on the blade guard ensure adequate flow of water to both sides of
the cutting blade.
•
A water curtain, fixed to head axle restricts water spray and minimises water loss.
•
The pump switch is located on the right side of the main switch.
Electrical Motor (8)
Leroy-Somer motor. Low voltage trigger (NVR) built in the switch prevents the motor to restart for
example after a power cut. The electric motor has an overload protection. Thermal overload tripping
can occur for two reasons:
a. tripping under light load
If connection is incorrect
b. tripping under heavy load
If motor has been overloaded
The ON-OFF switch also serves as emergency stop.
Anti-tipping device (9)
Two sheaves located on each side of the conveyor cart stabilise the cart while its usage. It also
prevents the cart from tipping from the frame.
Blocking device (10)
The cart can be fixed on the frame to allow the machine to be transported without danger.
Summary of Contents for clipper CHW Series
Page 1: ...CHW OPERATING INSTRUCTIONS...
Page 2: ...2...
Page 4: ...4...
Page 18: ...18 7 3 Circuit diagram 230V Motor...
Page 19: ...19 115V Motor...
Page 22: ...22...