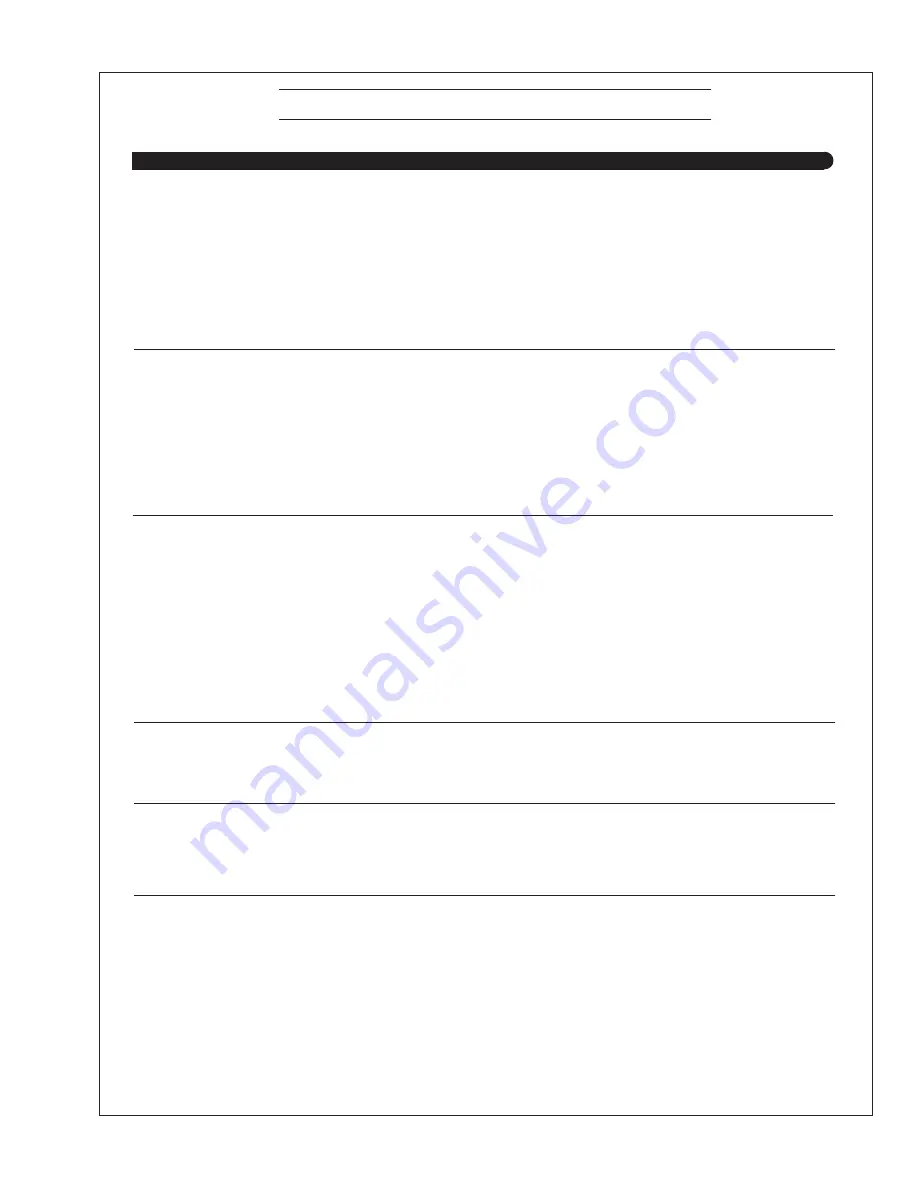
ONL844T4E 3/18
29
ENGINE
PROBLEM
POSSIBLE CAUSE
RECOMMENDATION(S)
Engine Overheats
Low coolant level
• Fill tank or radiator to proper level.
• Check hoses for loose connections
and leaks.
Cooling system needs flushing
• Flush cooling system.
Defective thermostat
• Remove and check thermostat.
Defective temperature gauge
• Check water temperature with thermometer
and replace gauge if necessary.
Engine Knocks
Insufficient oil
• Contact your dealer.
Injection pump out of time
• Contact your dealer.
Below normal engine temperature • Check your thermostats.
• Check water temperature to see if
temperature gauge is working properly.
Engine overheating
• See “Engine Overheating” section.
High Fuel Consumption
Improper type of fuel
• Use correct fuel for temperature.
Clogged or dirty air cleaner
• Service air cleaner.
Improper valve clearance
• Contact your dealer.
Injection nozzles dirty
• Contact your dealer.
Injection pump timing off
• Contact your dealer.
Engine not at proper temperature • Check your thermostats.
• Check water temperature with thermometer
and replace gauge if necessary.
Below Normal
Thermostat not working properly • Check thermostat.
Engine Temperature
Temperature gauge
• Check water temperature with thermometer.
not working properly
Low Oil Pressure
Low oil level
• Fill crankcase to proper level.
Improper type of oil
• Drain and fill crankcase with correct oil.
Partially plugged oil filter
• Replace filter.
High Oil Consumption
Break-in period
• Oil consumption decreases after break in.
Crankcase oil too light
• Use proper viscosity oil.
Oil leaks
• Check for leaks in lines around gaskets
and drain plug.
If you cannot correct problems with these procedures, see your
Northern Lights
dealer.
Troubleshooting