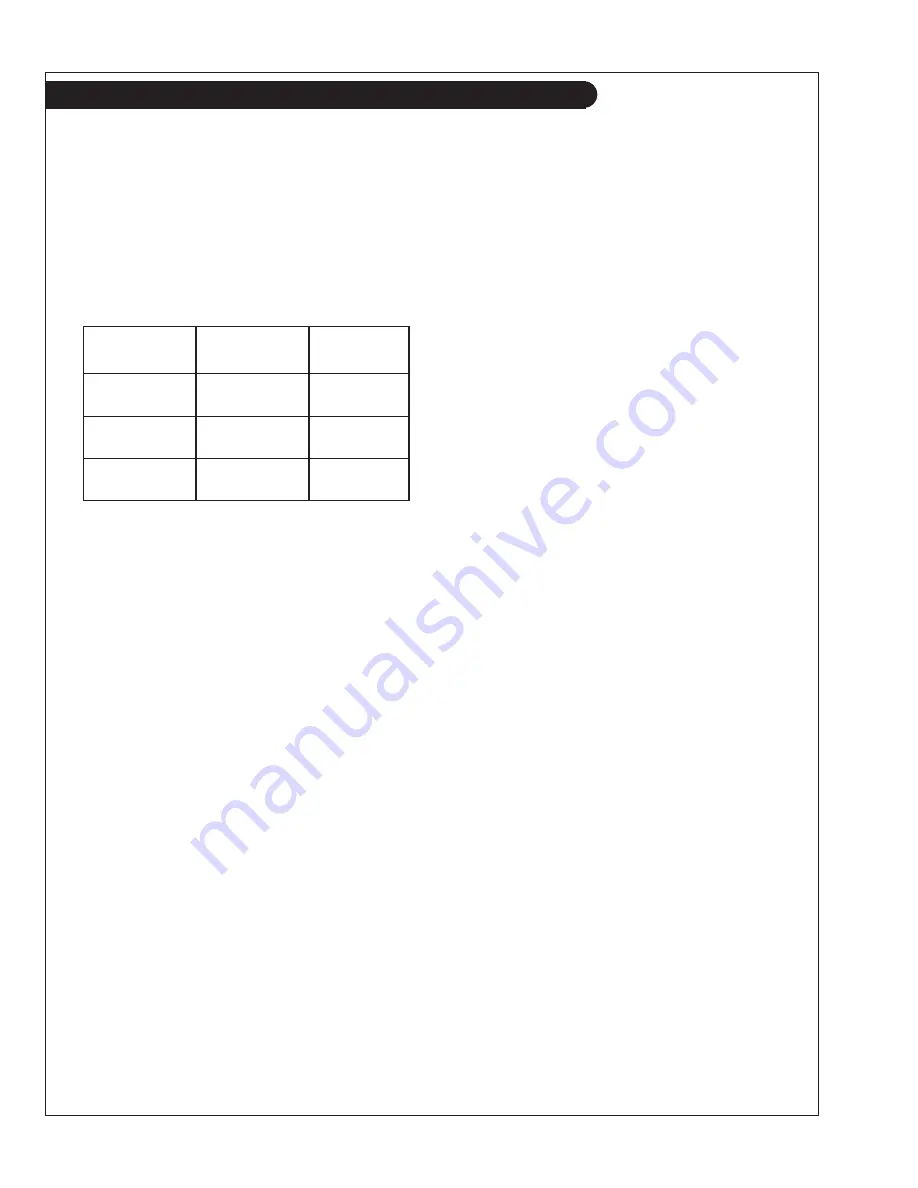
ONL753W2 10/09
12
Servicing
LUBRICATION - GENERAL
1. Use only clean, high quality lubricants stored in
clean containers in a protected area.
2. These lubricants are acceptable:
a. API Service CC/CD/CE single viscosity oils.
b. API Service CC/CD/SF multi-viscosity oils.
3. Use the proper weight oil for your average operation
temperature.
Figure 4: Lube Oils
4. Some increase in oil consumption may be expected
when SAE 5W and SAE 5-20W oils are used. Check
oil level frequently.
5. Never put additives or fl ushing oil in crankcase.
SP1. CHECKING OIL LEVEL
1. Check the oil level in the crankcase with the dip-
stick. The oil level must be in the waffl ed area
on the stick. Never allow the level to go below this
area. Follow the lubrication recommendations above.
SP2. OIL CHANGES
1. The set is delivered with special break-in oil.
Change the engine oil and oil fi lter after 50 hours
of operation. Use Service CC 30 weight oil during
the fi rst 100 hours.
2. Change the oil and fi lter again at 100 hours using the
oil recommended in Figure 4. After this, change oil
and fi lter every 250 hours.
3. During intermittent cold weather operation, change
oil every 100 hours or six weeks, whichever comes
fi rst.
4. Change oil at any seasonal change in temperature
when a new viscosity of oil is required.
5. Change oil when engine is warm.
6. Dispose of waste oil in an approved manner.
7. Never use a fl ushing oil.
8. Loosen the clamp on the oil change tube. Remove
cap. Drain oil. Replace the cap and tube.
9. Refi ll engine with recommended oil.
10. Engine capacity with new oil fi lter is:
3.7 quarts (3.5 liters)
SP3. CHANGING LUBE OIL FILTER
1. Change the lube oil fi lter every 250 hours.
2. Use
a
fi lter wrench to remove old fi lter. Dispose of
fi lter in approved manner.
3. Make sure the gasket from the old fi lter is removed
and discarded. Clean mount face.
4. Spread a thin fi lm of engine oil on the rubber gasket
on the new fi lter and screw it on nipple until gasket
meets the sealing surface.
5. Using hands only – no wrench – tighten fi lter
one-half turn farther. Overtightening can do
damage
to
fi lter housing.
6. Fill engine with recommended oil. Start engine and
check for leakage. Stop engine, wait 3 minutes, and
check oil level. Add additional oil if necessary.
7. The
oil
fi lter part number is:
#24-02001
Air
Single
Multi-
Temperature
Viscosity
Viscosity
Above
32°F
SAE 30W
SAE 15-40W
(0°C)
-10 to 32°F
SAE 10W
SAE 10-30W
(-23 to 0°C)
Below
-10°F
SAE 5W
SAE 5-20W
(-23°C)
Summary of Contents for Lugger ONL753W2
Page 11: ...ONL753W2 10 09 11 Service Record Notes...
Page 26: ...ONL753W2 10 09 26...