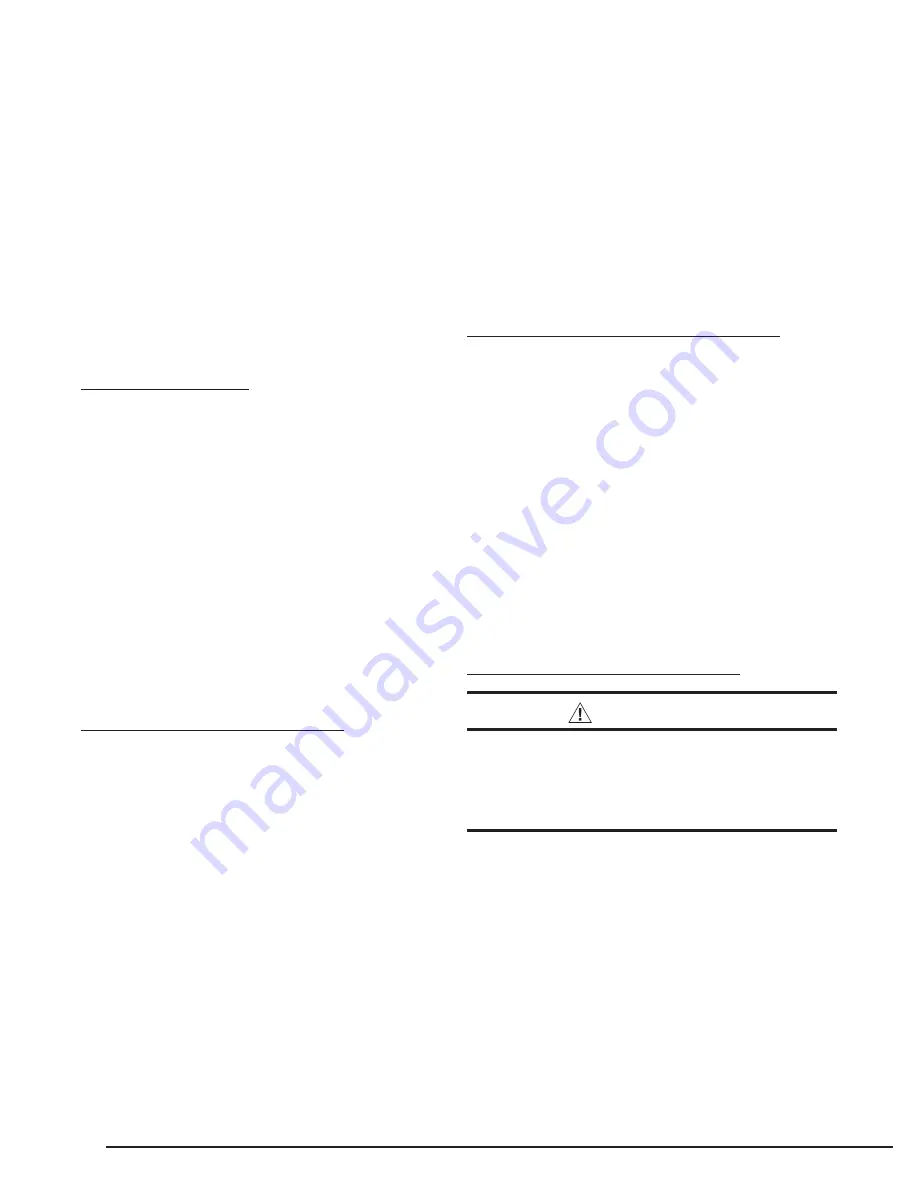
18
5. Set the thermostat above room temperature to begin
the heating cycle of the furnace.
6. Check that the furnace ignites and operates properly.
7. After ignition, visually inspect the burner assembly to
ensure that the flame is drawn directly into the center of
the heat exchanger tube. In a properly adjusted burner
assembly, the flame color should be blue with some light
yellow streaks near the outer portions of the flame.
NOTE:
The ignitor may not ignite the gas until all air is
bled from the gas line. If the ignition control locks out,
turn the thermostat to its lowest setting and wait one
minute then turn the thermostat above room temperature
and the ignitor will try again to ignite the main burners.
This process may have to be repeated several times
before the burners will ignite. After the burners are lit,
check all gas connections for leaks again with the soap
and water solution.
Verifying System Heating
(2-Stage Heating)
1. Set the thermostat to the lowest setting.
2. Follow the procedures given on the operating instruction
label, in this manual or attached inside the louvered
control access panel.
3. Set the thermostat one degree above room temperature
and verify the Operating Sequence (
4. Verify that the compressor and outdoor fan motor are
not energized.
5. After determining the system is running (1-2 minutes),
raise the thermostat’s setpoint an additional 3-4 degrees
until the heating system moves into 2nd stage or high
heat operating mode. The gas valve will energize to high
heat mode while the induced draft motor and indoor
blower motor both increase in speed.
6. After the unit has run for approximately five minutes,
set the thermostat below room temperature and verify
the shutdown sequence; steps 10 -12 in the Operating
Verifying & Adjusting Temperature Rise
Verify the temperature rise through the unit is within the
range specified on the unit data label and in
. Temperature rises outside the specified range could
result in premature heat exchanger failure.
1. Place thermometers in the return and supply air stream
as close to the unit as possible. The thermometer on the
supply air side must be shielded against direct radiation
from the heat exchanger to avoid false readings.
2. Adjust all registers and duct dampers to the desired
position. Run the unit for 10 to 15 minutes before
taking any temperature readings. The temperature
rise is the difference between the supply and return air
temperatures.
NOTE:
For typical duct systems, the temperature rise will
fall within the range specified on the data label (with the
blower speed at the factory recommended setting) see
in
. If the measured temperature rise
falls outside the specified range, it may be necessary to
change the blower speed. Lowering the blower speed
increases the temperature rise and a higher speed
decreases the temperature rise.
The unit is equipped with an ECM type motors. Speed
selection is made by setting the switches on the motor
NOTE:
For
change in blower speed selection to take effect, system
power must be cycled off then restored after 10 seconds.
Refer to the Blower Speed section (
) for
additional information.
The integrated control starts the circulating air blower 22
seconds after the gas valve is opened. The control board
is factory set to turn the blower motor off 120 seconds
after the gas valve is closed.
Gas Supply Pressure Verification & Adjustment
1. Turn OFF the gas supply at the manual valve located
on the outside of the unit.
2. Using a 3/16” Allen wrench, remove the plug from the
inlet pressure tap (INLET side of gas valve). See
3. Install an 1/8” NPT pipe thread fitting, that is compatible
with a Manometer or similar pressure gauge.
4. Connect the Manometer or pressure gauge to the Inlet
Pressure Tap.
5. Turn ON the main gas supply at the manual valve.
6. Check and adjust the incoming gas line pressure to 4.5-
10.0 inches Water Column for Natural gas or 11.0-14.0
inches Water Column if converting unit to LP/Propane
gas.
7. Turn OFF the gas supply at the manual valve.
8. Disconnect the Manometer or pressure gauge.
9. Remove the NPT fitting and reinstall the INLET pressure
tap plug. Hand tighten the plug first to prevent cross
threading. Tighten with 3/16 Allen wrench.
Verifying the Firing Rate of the Appliance
WARNING:
Do not attempt to drill the gas orifices. If the orifice
size must be changed, use only factory supplied
orifices. Improperly drilled orifices may cause
fire, explosion, carbon monoxide poisoning,
personal injury or death.
The firing rate must be verified for both LOW and HIGH
fire for each installation to prevent over-firing of the unit.
The firing rate must not exceed the rate shown on the
unit data label. To determine the firing rate, follow the
steps below:
1. Obtain the gas heating value (HHV) from the gas supplier.
2. Shut off all other gas fired appliances.
3. Start the unit in LOW heating mode and allow it to run
for at least 3 minutes.
4. Measure the time (in seconds) required for the gas
meter to complete one revolution.
5. Convert the time per revolution to cubic feet of gas per
hour using
6.Multiply the gas flow rate in cubic feet per hour by the
heating value of the gas in Btu per cubic foot to obtain
the firing rate in Btu per hour. See