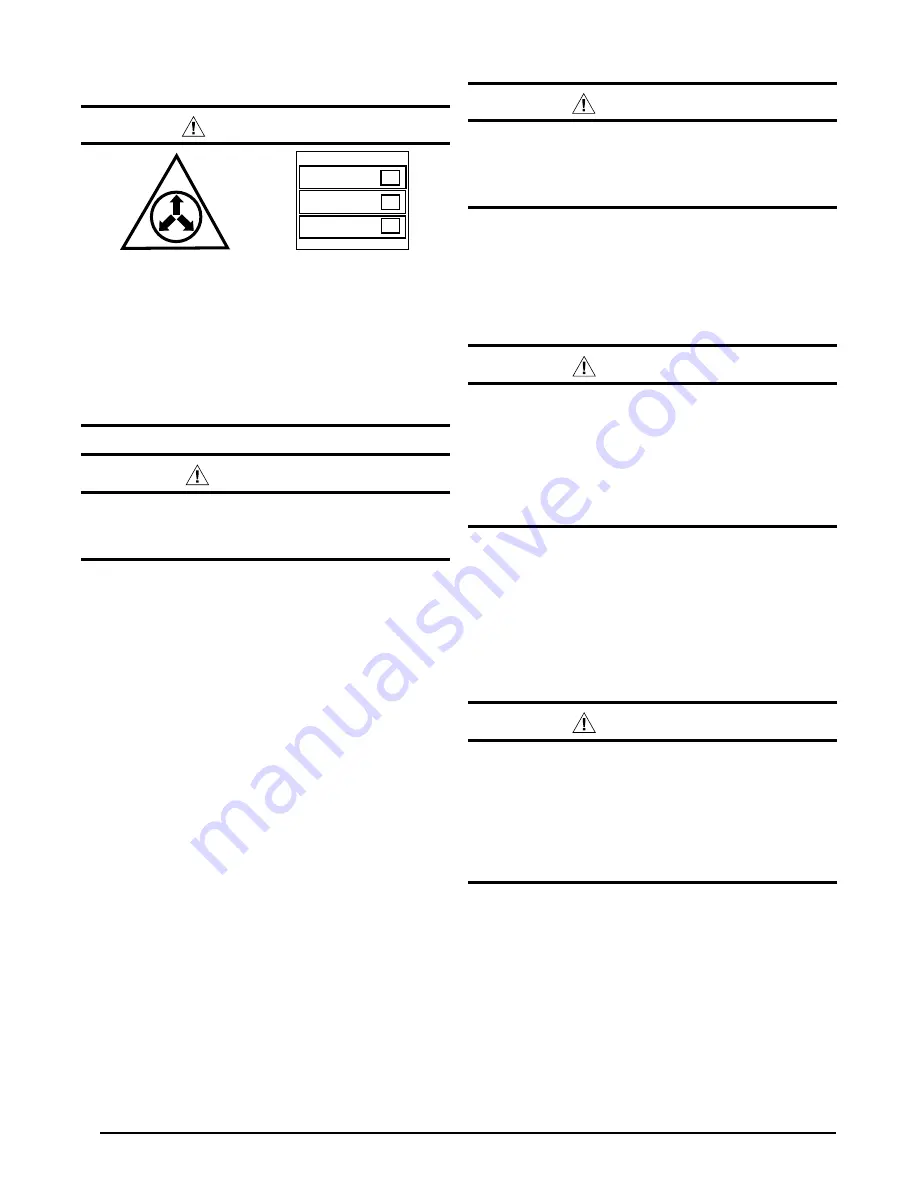
8
CAUTION:
Before brazing the air handler, remove the core
from the service port. Failure to comply may
result in leakage at the service valve. Replace
the core and cap once brazing is complete.
•
B4VM-E Series air handlers are charged through service
valves on the end of the liquid tube for each circuit.
These must be removed before brazing the line sets.
Refrigerant Line Connections
WARNING:
The coil in the air handler is factory shipped with
a nitrogen charge. Avoid direct face exposure
or contact with valve when gas is escaping.
Always ensure adequate ventilation is present
during the depressurization process. Address
any uncertainties before proceeding. Failure
to comply with this warning could result in
equipment damage, personal injury, or death.
NITROGEN
HEALTH
FLAMMABILITY
REACTIVITY
0 Minimal Hazard
1 Slight Hazard
1
0
0
CAUTION:
This unit uses refrigerant R-410A. DO NOT use
any other refrigerant in this unit. Use of another
refrigerant will damage the unit.
• The installer should make every effort to ensure the
field installed refrigerant containing components of the
system have been installed in accordance with these
instructions and sound installation practices for reliable
system operation and longevity.
• The air handler coil does not contain a refrigerant charge.
Refer to the installation instructions supplied with the
outdoor unit for refrigerant charge information.
• Always refer to the installation instructions supplied with
the outdoor unit for piping requirements. The suction
and liquid lines must be sized in accordance with the
condensing unit specifications. See Table 3 (page 14)
for liquid and suction line locations.
• When connecting refrigerant linesets together, it is
recommended that dry nitrogen be flowing through the
joints during brazing. This will prevent internal oxidation
and scaling from occurring.
• Refrigerant tubing should be routed in a manner that
minimizes the length of tubing and the number of bends
in the tubing. It should be supported in a manner that
prevents it from vibrating or abrading during system
operation. Tubing should be kept clean of foreign debris
during installation.
• If precise forming of refrigerant lines is required, a copper
tubing bender is recommended. Avoid sharp bends and
contact of the refrigerant lines with metal surfaces.
• Refrigerant lines should be wrapped with pressure
sensitive neoprene or other suitable material where
they pass against sharp sheet metal edges.
Connecting the Linesets
1. Remove grommets from line set holes.
CAUTION:
To protect the Thermistor and EXV, it is
recommended that a wet rag be wrapped
around the suction line in front of the close
off plate before applying heat. Failure to keep
components cool during brazing may result
in structural damage, premature equipment
failure, or possible personal injury.
2. Unbraze and remove the cap on the suction line.
3. Route and cut both lineset tubes to proper length in
accordance with the outdoor unit specifications. Verify
the ends are round, clean, and free of any burrs.
4. Position grommet on line set with sufficient distance away
from brazing area. Brazing processes can permanently
damage grommets.
5. Connect the suction and liquid lineset tubes.
CAUTION:
To protect the Thermistor and EXV, it is
recommended that a wet rag be wrapped
around the suction line in front of the close
off plate before applying heat. Failure to keep
components cool during brazing may result
in structural damage, premature equipment
failure, or possible personal injury.
6. Braze the individual connections with dry nitrogen
flowing through the joints. NOTE: This will prevent
internal oxidation and scaling from occurring.
7. Wrap the refrigerant lines with pressure sensitive
neoprene or other suitable material especially where
the lines enter the opening in the sheet metal.
8. Evacuate the system of moisture and non-condensables
to prevent low efficiency operation or damage to the
unit. The suggested range of evacuation is 250 - 500
microns.