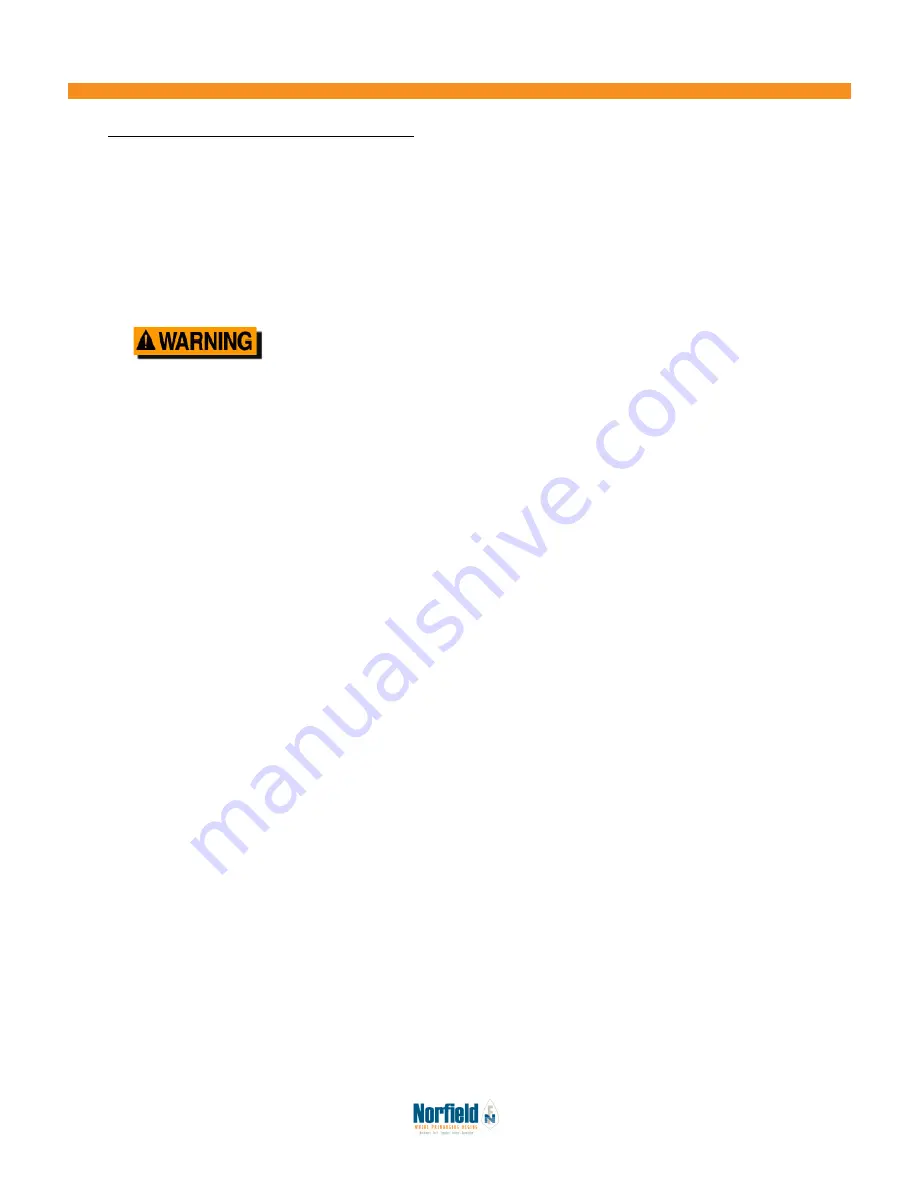
19
MAINTENANCE
SECTION 4 MAINTENANCE
4-1 GENERAL MAINTENANCE
It is the machine owner’s responsibility to insure that the machine is properly maintained and that per
-
sonnel are adequately trained to safely perform the maintenance function.
A program of routine and preventive maintenance that is strictly adhered to will keep expensive “down
time” to a minimum and give maximum life to the machine. Please read and use the following checklist
for daily and weekly procedures.
ALWAYS LOCK AND TAG OUT THE ELECTRICAL AND PNEUMATIC
POWER SOURCES TO THE MACHINE BEFORE STARTING INSPECTION
OR PERFORMING MAINTENANCE.
4-2 DAILY CHECKS: (EVERY 6-8 HOURS OF OPERATION)
1. Inspect the machine for loose fasteners. Check the pneumatic system for leaking fittings or tubing or
kinked tubing.
2. Clean the entire machine with an air hose.
3. Run a test jamb to insure that all adjustments are accurate.
4-3 WEEKLY CHECK: (EVERY 30-40 HOURS OF OPERATION)
1. Clean all moving parts on the router assembly with a not-flammable, non-oil based cleaning solvent
to remove any pitch build-up.
4-4 GENERAL MAINTENANCE COMMENTS
A clean machine is essential for superior performance and reduced maintenance.
As the seals in valves and cylinders will take a “set” when not operating, the manufacturers of those
components strongly recommend that the valves and cylinders be cycled at least twice before starting the
days work. This pre-cycling allows the seals to retain natural sealing ability and will lengthen the life of
the valves and cylinders considerably.
Never use oil, silicon or graphite to lubricate any bearing surface or chrome slide rod. Any lubricants
such as those mentioned above will collect fine sawdust and dirt particles that will wear the bearings very
quickly. If any assembly is binding and you have kept everything clean, the problem is most likely that
the parts are not properly aligned or have become excessively worn.
Clean, dry air is a must. Moisture or solid contaminants in the air supply will shorten the life of air com
-
ponents considerably. We recommend you make it a common practice to inspect your compressor and air
system regularly. Drain the compressor tank and all moisture traps daily. Keep the compressor’s crank
-
case full and change the oil at thee recommended intervals.
Maintain an adequate air supply to the machine. Regulator pressure should not drop during operation.
If it does, check the condition of the filters. Clean or replace them as required.