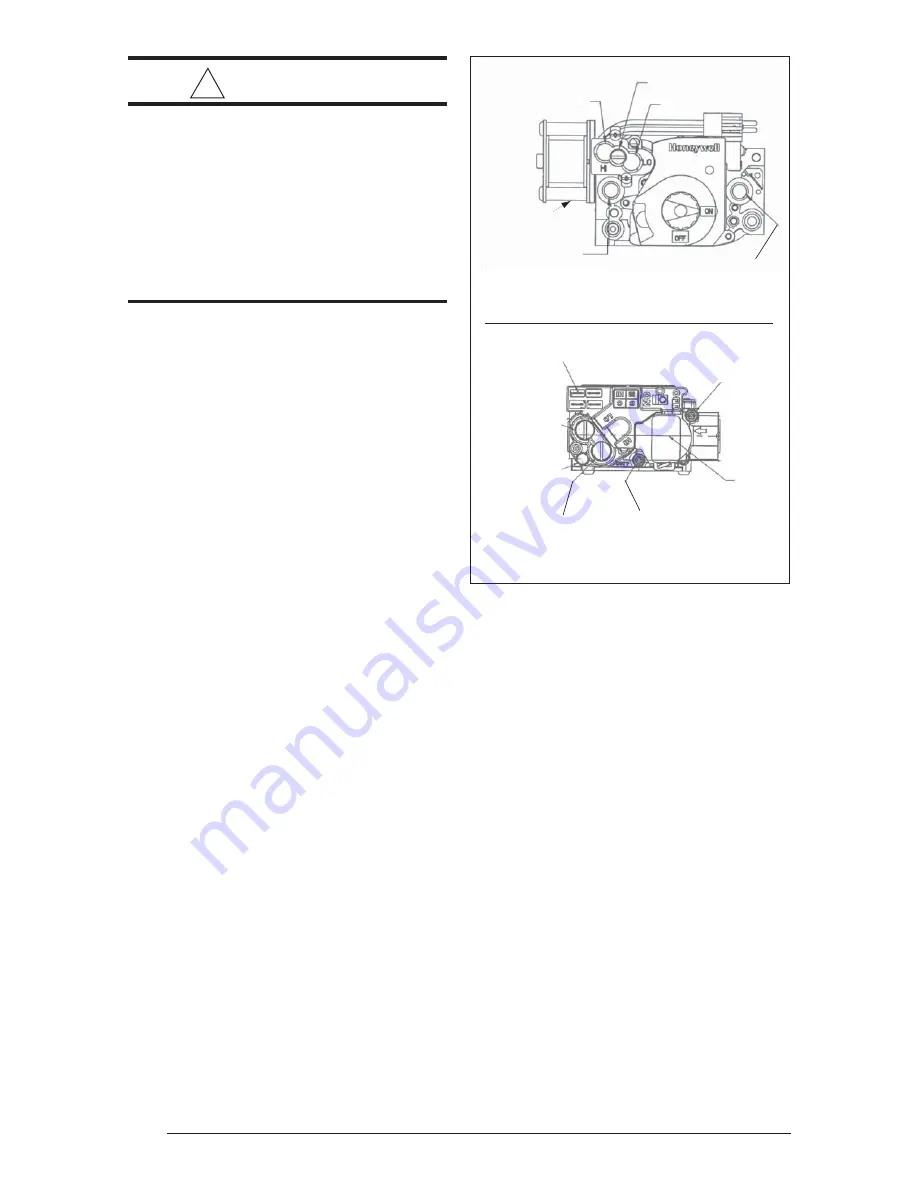
24
Figure 20. Gas Valve
(Honeywell shown)
(White Rodgers shown)
(4) QUICK DI
S
CONNECT TERMINAL
S
1
S
T
S
TAGE
REGULATOR COVER
REGULATOR ADJU
S
T
BENEATH THI
S
S
CREW
VENT (.
33
0 DIA.
+DFT. PO
S
T)
ACCEPT
S
5/16” HO
S
E
CONNECTION
2ND
S
TAGE
REGULATOR COVER
REGULATOR ADJU
S
T
BENEATH THI
S
S
CREW
OUTLET PRE
SS
URE
PO
S
T
S
ET
S
CREW:
3
/
3
2
”
HEX HEAD (.
33
9 DIA. +DFT.)
ACCEPT
S
5/1
8”
HO
S
E CONNECTION
CONTROL
LABEL
INLET PRE
SS
URE PO
S
T
S
ET
S
CREW:
3
/
3
2
”
HEX HEAD
(.
33
9 DIA. +DFT.)
ACCEPT
S
5/1
8”
HO
S
E CONNECTION
VENT FITTING FOR 90 PLU
S
EFFICIENT APPLIANCE
S
LOW
S
TAGE ADJU
S
TMENT
UNDER VENT CAP
HIGH
S
TAGE ADJU
S
TMENT
UNDER VENT CAP
OUTLET PRE
SS
URE TAP
1/
8
NPT
INLET PRE
SS
URE TAP
1/
8
NPT
2-
S
TAGE
OPERATOR
value based on sea level can be obtained from
your local gas utility. The heating value of gas
at high altitude is always lower than the sea level
heating value. The heating values used in Tables
10 and 11 are based on sea level values.
Pressure Switch Conversion for
High Altitude Applications
These units are factory equipped to operate
between zero and 8000 feet above sea level. For
higher altitude applications, you may need to
replace the vent pressure switch in addition to the
main gas burner orifices.
Natural Gas High Altitude
Conversion
All factory shipped furnaces are ready to operate
between zero and 4999 ft. above sea level. For
higher altitudes (between 5000 and 10,000 ft.
above sea level), conversion can be achieved
simply by adjusting the furnace manifold
pressure as shown in Tables 6 and 7.
!
WARNING:
This furnace was equipped at the fac-
tory for use with natural gas only. A
special kit, supplied by the manufac-
turer, is required to convert the fur-
nace to operate on LP/propane gas.
Failure to use the proper conversion
kit can cause fire, explosion, property
damage, carbon monoxide poisoning,
personal injury, or death.
MANIFOLD PRESSURE
ADJUSTMENT
Manifold pressures for low and high stages are
independently adjustable. Adjustment tap
locations on the valve are shown in Figure 20.
Manifold pressure would be adjusted below
procedure:
-
Turn off gas shut off valve outside furnace.
-
Install manometer on the gas valve at the
outlet pressure tap.
-
Turn on the shut off. Run furnace at high
fire and set manifold pressure. Also set
manifold pressure while running at low fire
(refer to Tables 6 and 7.)
-
Ensure plug is tight after removing
manometer.
Conversion
Conversion of this furnace to use LP/propane
gas must be made by qualified service
personnel, using
only
approved parts.
IMPORTANT NOTE: When converting a low
NOx furnace from Natural Gas to LP/Propane
Gas, it is necessary to remove the NOx
baffles from the furnace.
HIGH ALTITUDE CONVERSION
High Altitude Application
Conversion of this furnace to replace the pressure
switch or to utilize LP/propane gas must be made
by qualified service personnel, using factory
authorized or approved parts. High altitude
applications with this furnace can be field
performed by a simple adjustment of manifold
pressure, and if necessary changing the orifices
and the vent pressure switch. The changes
required depend on the installation altitude and
the heating value of the gas. The gas heating