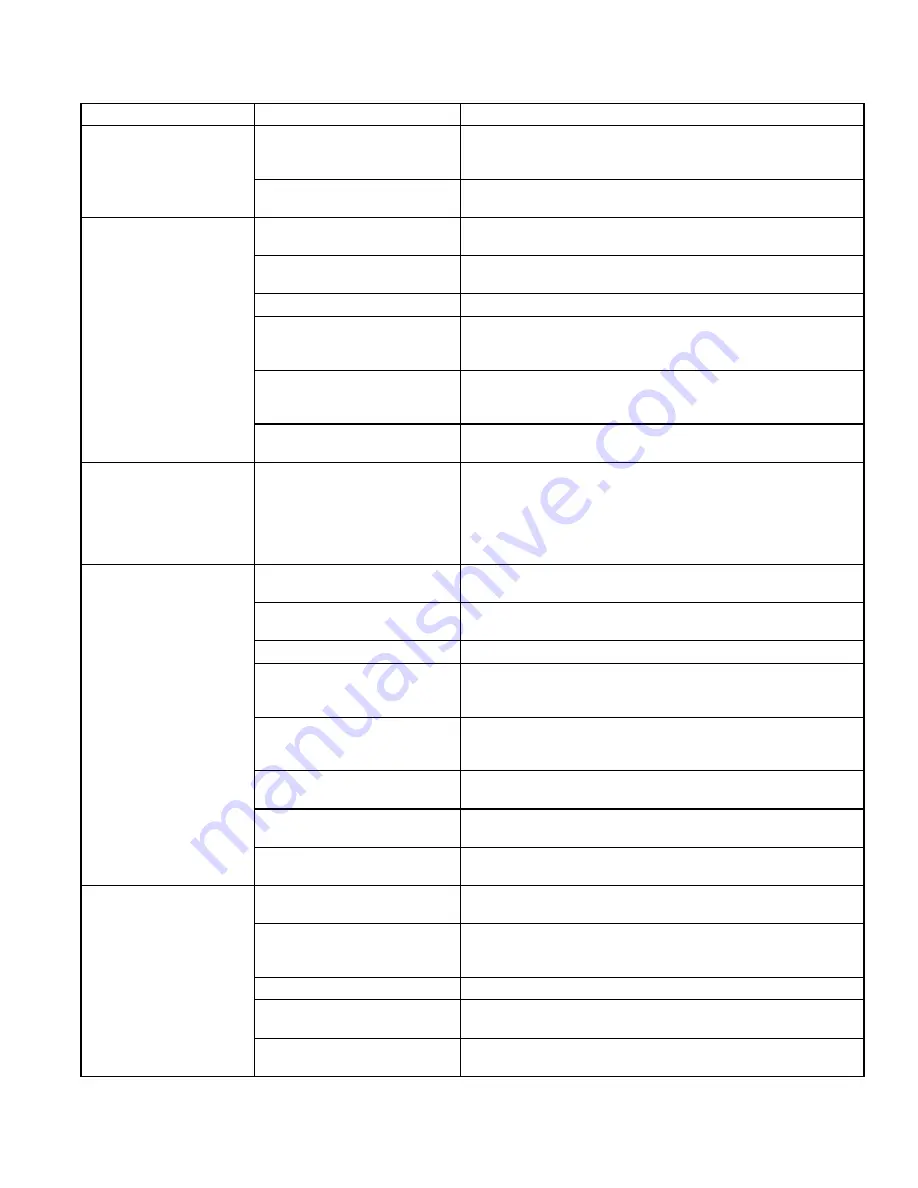
151B0801 R5 3/28/2006
26
Table C-4: System and General Troubleshooting
continued
Problem Possible
Cause
Remedy
Photo Cell wiring shorted or
room light leaking into photo
cell compartment
Check photo cell (cad cell) wiring for short circuits. Also, check
for room light leaking into cad cell compartment. Repair light
leak if necessary. See Table C-3.
Furnace will not start.
Open safety switch.
Check for open limit or auxiliary limit. Also, check internal wiring
connections; loose connectors, etc.
No fuel oil.
Check fuel oil supply. Check that all hand operated fuel oil
valves are in the open position. Fill oil storage tank if necessary.
Clogged nozzle.
Replace nozzle with high quality replacement. Use rating plate
or Tables in Appendix A as a guide.
Clogged oil filter.
Replace oil tank filter or in-line filter if used.
Low oil pump pressure.
Connect pressure gauge to oil pump. Adjust pump pressure, or
replace oil pump if necessary. Ensure that erratic pressure
readings are not caused by defective fuel oil line.
Air getting into fuel oil lines, or
fuel oil line dirty, clogged, or in
some manner defective.
Check fuel oil lines. Replace any compression fittings found with
high quality flared fittings. Check for any signs of oil leaks. Any
oil leak is a potential source of air or contaminants.
Furnace will not start
without first pushing oil
primary control reset
button.
(Happens on frequent
basis)
Defective burner motor.
Check burner motor. If burner motor is cutting out on over-load,
determine why. Replace if necessary.
Furnace starts, but cuts
out requiring manually
resetting the oil protector
reset button.
Photo Cell (Cad Cell)
defective.
If cad cell is dirty, clean it. (Determine why cad cell is getting
dirty). If cad cell is poorly aimed, realign it. NOTE: The photocell
should have a resistance of 100K
Ω
in absence of light; a
maximum of 1500
Ω
in the presence of light. Ensure that room
light is not leaking into the cad cell compartment. (See
diagnostic light section).
No fuel oil.
Check fuel oil supply. Check that all hand operated fuel oil
valves are in the open position. Fill oil storage tank if necessary.
Clogged nozzle.
Replace nozzle with high quality replacement. Use rating plate
or Tables in Appendix A as a guide.
Clogged oil filter.
Replace oil tank filter or in-line filter if used.
Low oil pump pressure.
Connect pressure gauge to oil pump. Adjust pump pressure, or
replace oil pump if necessary. Ensure that erratic pressure
readings are not caused by defective fuel oil line.
Air getting into fuel oil lines, or
fuel oil line dirty, clogged, or in
some manner defective.
Check fuel oil lines. Replace any compression fittings found with
high quality flared fittings. Check for any signs of oil leaks. Any
oil leak is a potential source of air or contaminants.
Defective burner motor.
Check burner motor. If burner motor is cutting out on over-load,
determine why. Replace if necessary.
Water or contaminants in oil.
Drain fuel oil storage tank, replace fuel oil. (Consult with fuel oil
supplier).
Furnace starts, but cuts
out requiring manually
resetting the oil protector
reset button.
Frozen oil line.
Gently warm oil line. Insulate oil line. (Outdoor piping size may
require increased diameter).
Electrodes out of adjustment
or defective.
Check electrode settings. Check electrodes for dirt build-up or
cracks in porcelain.
Poor transformer high voltage
connections or defective
transformer.
Check contacts between the igniter and electrodes. If OK,
replace the igniter
Fuel oil filter clogged.
Replace fuel oil storage tank filter and / or fuel oil in-line filter.
Defective oil pump.
Check burner motor / fuel oil pump coupling. Check oil pump
pressure. Replace fuel oil pump if necessary.
Oil burner sputtering at
nozzle
Fuel oil line partially clogged or
contains air.
Bleed air from oil line. If problem persists, replace oil line.
Continues on next page