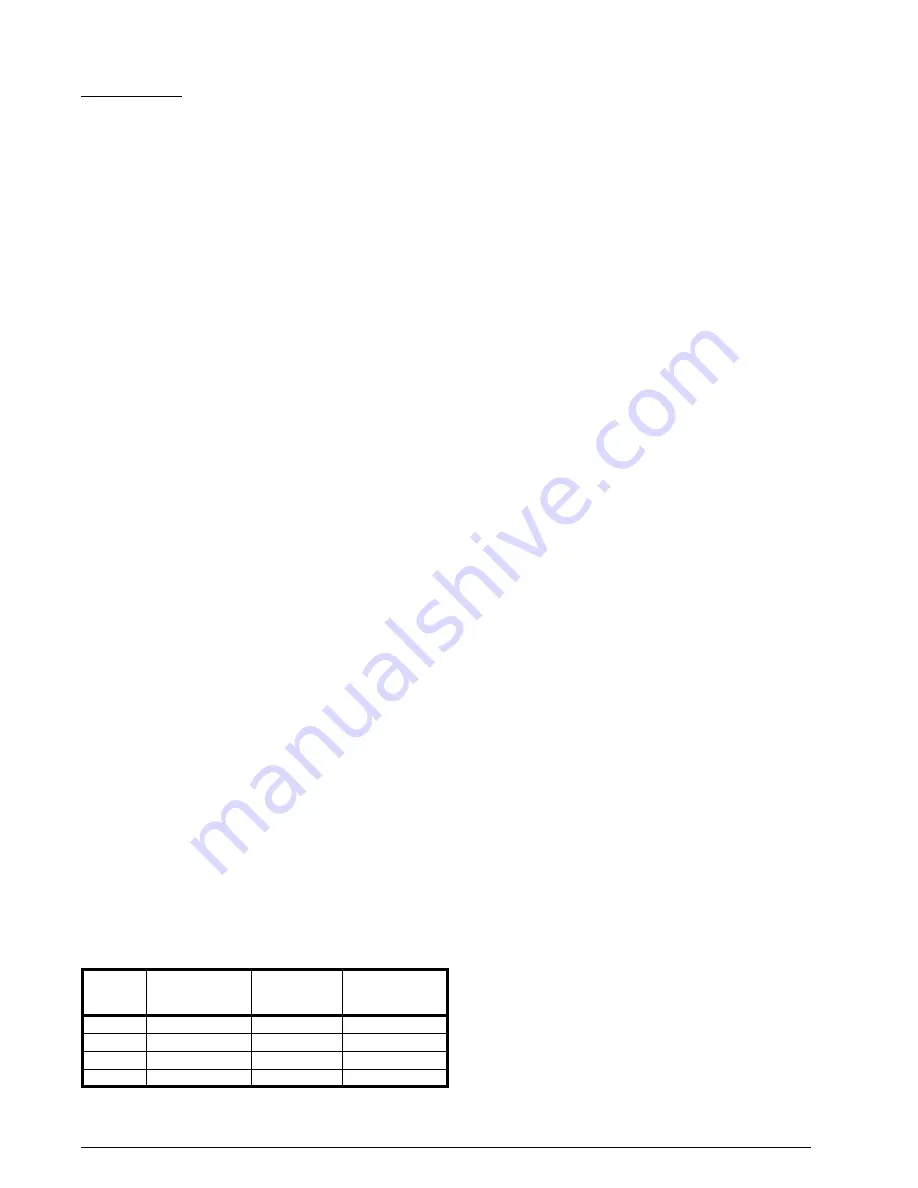
13
Delay Profile
The delay profile controls the start-up and shut-down
characteristics of the packaged heat pump unit. By varying
the start-up and shut-down characteristics of the packaged
heat pump unit, the system can be optimized for energy
efficiency, humidity control, and comfort.
The delay profile has a two-step ON delay. The blower
will begin operation at 31% airflow for 30 seconds. The
second step operation is 75% airflow for 30 seconds.
After the two-step ON delay has been completed, the
blower operation will be 100% until the thermostat has
been satisfied. There is also a 60 second OFF delay at
50% airflow.
Demand Defrost Control
The demand defrost board controls the defrost cycle
in response to ambient temperature, outdoor coil
temperature and accumulated compressor run time. The
heat pump is allowed to operate in the heating mode
until the combination of outdoor ambient and outdoor
coil temperatures indicate that defrosting is necessary,
based on the programmed defrost curve. There are four
preprogrammed defrost curves on the board.
• The defrost board is equipped with a 5 minute Anti-Short
Cycle Delay (ASCD). The outdoor unit remains off for
the 5 minute delay if the thermostat call is interrupted
or there is a loss of power to the unit.
• A jumper pin is used to switch between the different
curves. The default jumper position is curve 1 and is the
recommended setting for most standard applications.
See Table 5 for additional defrost curves settings.
•
The factory default setting does not include a 30 second
compressor delay function and has a 40 ° F defrost
terminate temperature. If additional defrost time is
needed, a higher terminate temperature is available
by selecting a different demand curve. NOTE: The
30 second compressor delay function is optional and
based on the demand curve selected.
• The standard defrost cycle will terminate after 13
minutes and 39 seconds or when the coil temperature
reaches its terminate temperature, whichever occurs
first.
• The control contains a forced - defrost feature, which
places the system into defrost mode every 6 hours
and 4 minutes, unless the coil temperature is above
the selected terminate temperature.
• The system can be manually forced into defrost mode at
any time by shorting the TEST terminals on the demand
defrost board together for more than 9 seconds. The
coil temperature sensor does not need to be cold when
the unit is forced into defrost. After the TEST input
Table 5. Demand Defrost Curve Profiles
Jumper
Position
Minimum Time
between Defrosts
(min)
Terminate
Temperature
(° F)
Compressor
Delay Function
1
20
40
NO
2
20
40
YES
3
20
75
NO
4
20
75
YES
is removed, the defrost mode will terminate in 13.7
minutes, if the coil temperature is above the terminate
set-point, or when the Y input is removed, whichever
occurs first.
NOTE: If a demand curve is selected which has a 30
second compressor time delay in defrost, the delay is
reduced to 10 seconds in TEST mode.
Ambient Sensor Mounting
For optimum performance of the heat pump system, the
ambient sensor must be mounted on the outside of the
unit. See Figure 6 (page 14).
1. Remove the mounting bracket wire tied to the control
bracket and all hardware included in the packet.
2. Remove star bushing from 7/8” hole in corner panel of
the unit. See Figure 7 (page 14).
3. Route the ambient sensor through the 7/8” hole in the
corner panel of the unit, and then through the 7/8” hole
in the mounting bracket.
4. Route the sensor through the star bushing. Use the star
bushing to secure the mounting bracket to the unit.
5. Secure the ambient sensor inside the plastic clip and
secure it to the mounting bracket with the screw and
nut provided.
6. Install one spacer nut between the plastic clip and
mounting bracket.
7. Bend the mounting bracket into position and screw the
mounting bracket to the corner panel.
Optional Humidistat
An optional humidistat may be installed in the return
air duct for humidity control (when needed), maximum
system capacity and energy efficiency. The humidistat
senses when humidity in the return air stream is above
a preset level and sends a signal to the motor to reduce
airflow. This allows more moisture to be removed until
the humidity level drops. NOTE: The indoor blower motor
of this packaged unit is pre-programmed for humidistat
operation. Remove the Red jumper wire between the R
and DEHUM terminals on the ignition control board.
If installing a humidistat, install it in the return air duct
as directed in the installation instructions included with
the kit. Wire the humidistat through the low-voltage wire
entrance in the packaged unit to the screw terminals
marked R & DEHUM.
Wire the humidistat to open on
rise in humidity.
When the HI/LO Dehumidify Green LED status light is
ON, it signals Low Humidity and keeps 24V supplied to
the motor for normal airflow requirements. If the humidity
level of the conditioned space increases the humidistat
will open. Loss of the 24V signal to the indoor blower
motor allows the motor to reduce to approximately 75%
of normal airflow selected until the humidity level drops.
The Green LED is OFF during high humidity conditions.
Check all factory wiring to the units wiring diagram. Inspect
the factory wiring connections to be sure none loosened
during shipping or installation.