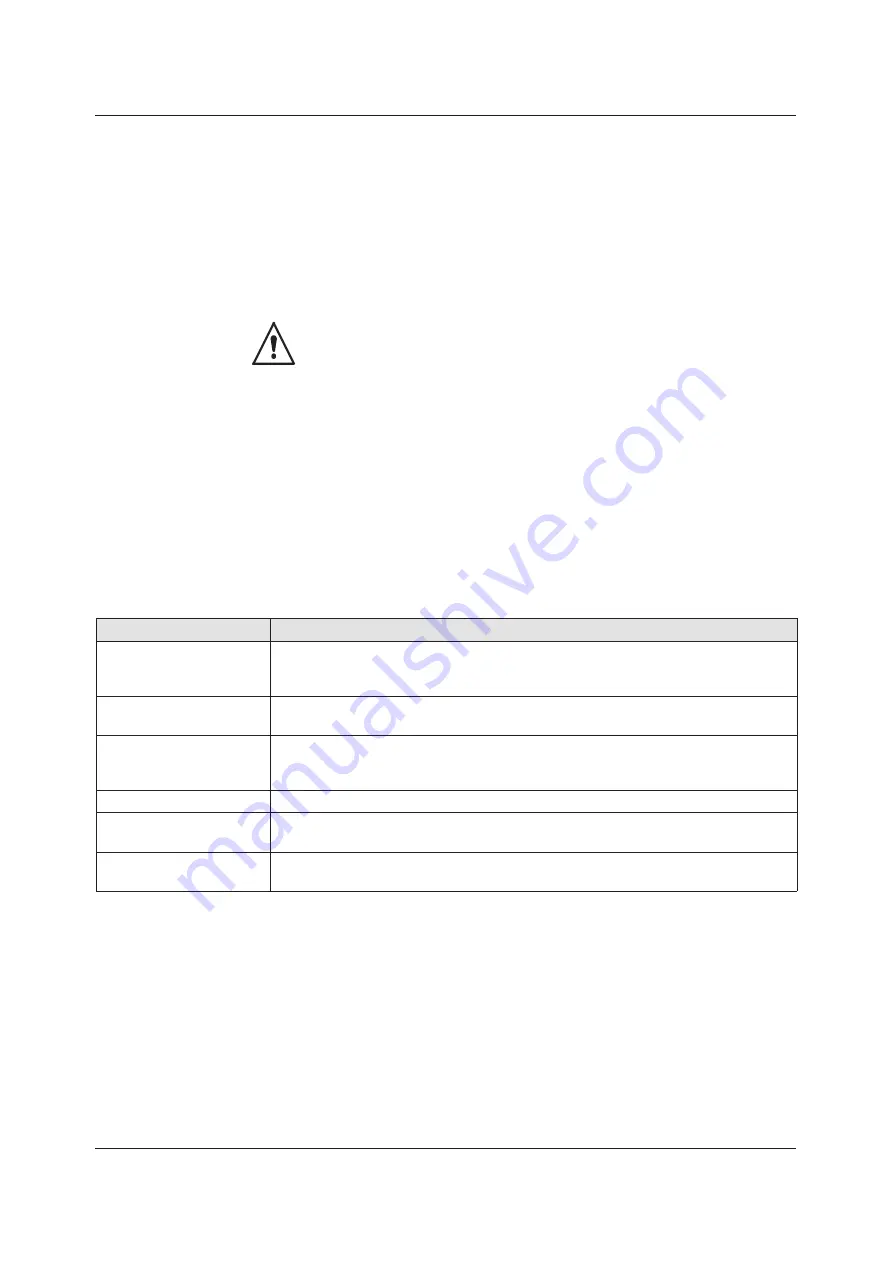
Maintenance
5-1
Part
E
2012 Nordson Corporation
Section 5
Maintenance
WARNING:
Allow only qualified personnel to perform the following tasks.
Follow the safety instructions in this document and all other related
documentation.
NOTE:
Maintenance procedures given here are for the feed center only.
Refer to your system component manuals for maintenance procedures for
all other system equipment.
Daily Maintenance
NOTE:
You may need to perform these procedures more or less often,
depending on your application requirements.
Table 5-1 Daily Maintenance Procedures
Component
Maintenance Procedure
Sieve
Disassemble and clean the sieve and screen. Inspect the sieve screen and
replace it if powder is fused to it or it is damaged. Make sure the ground clip is
installed.
Cables, Tubing, and
Feed Hoses
Check all external cables, powder hoses, and air tubing for damage. Repair or
replace as necessary.
HDLV Transfer Pumps
Purge the pumps. Inspect the pinch valve body for signs of powder leakage. If
powder is present in the pinch valve section, replace the pinch valves. Refer to
the Prodigy HDLV High-Capacity pump manual for repair procedures.
Powder Supply
Check the powder supply level regularly and add powder as necessary.
Compressed Air
Supply
Check the compressed air dryers and filters. Drain filters if needed. Perform
maintenance as necessary.
Enclosure
Clean the interior and exterior of the Spectrum HD feed center. Check all
equipment ground connections.