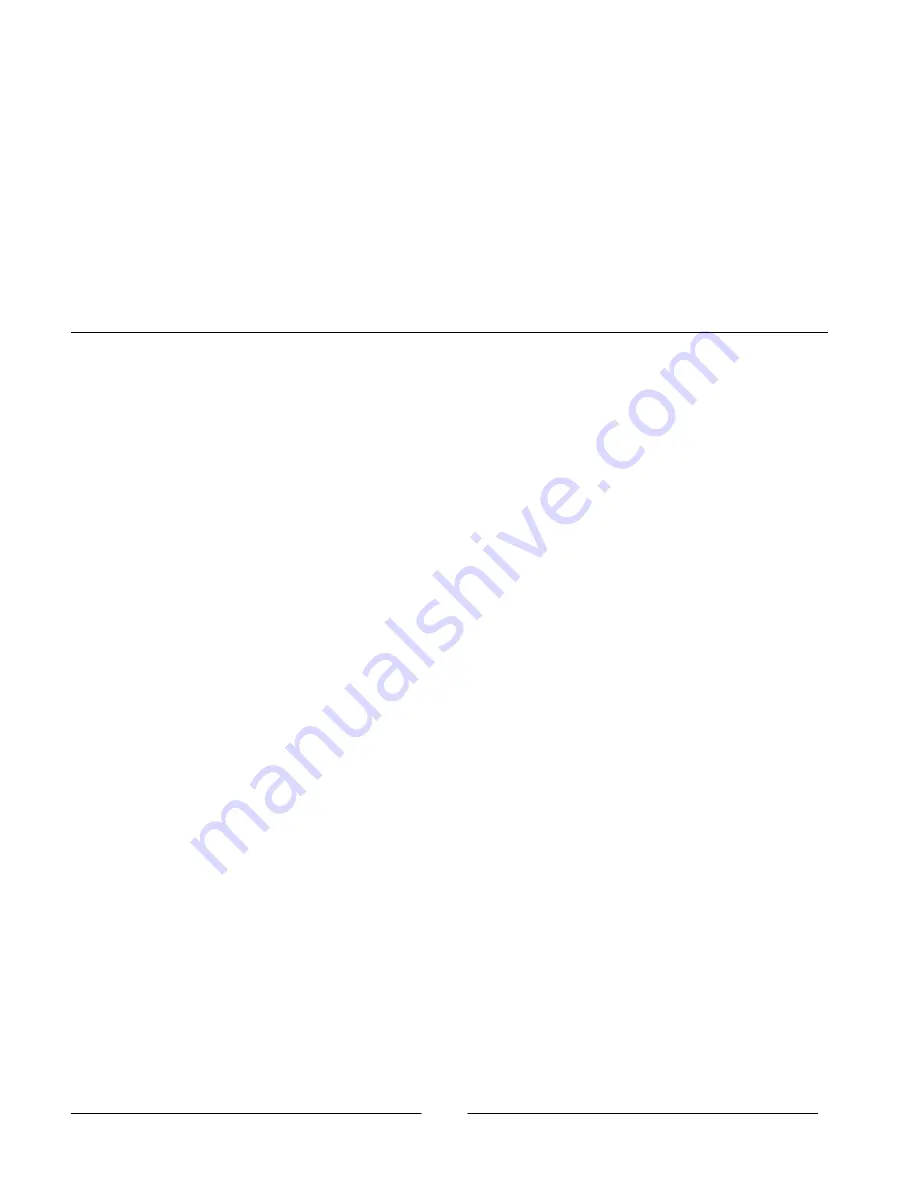
4
Weekly
S
Perform the daily maintenance procedures.
S
Remove the rear shroud and check the valve
weep holes. Coating material, solvent, or cleaning
solution in the weep holes indicates that the valve
seals are leaking and may need replacing. Refer
to the valve instruction sheets for repair
information.
Periodically
S
Perform resistance checks on your system
components. Refer to the
RA-20R Rotary
Atomizer
manual for instructions and resistance
values.
S
Check the continuity of all equipment grounds in
the spray area. Make sure the coating material
supply and waste container (if used) are grounded.
S
Check the resistance between the workpieces and
ground. Resistance must not exceed one
megohm. For best transfer efficiency, resistance
should be less than 300 ohms. Strip workpiece
hangers regularly.
Operating Requirements
Fluid Pressure and Flow
Fluid pressure:
0.34
−
7 bar (5
−
100 psi)
Flow rate, maximum:
1500 cc/min at 7 bar
(50 oz/min at 100 psi)
130 centipoise material at 7 bar (100 psi),
0.080 orifice:
270 cc/min
NOTE:
130 centipoise is approximately
S
53 seconds on Zahn 2
S
15 seconds on Zahn 3
S
43 seconds on Ford 4
S
64 seconds on Fisher 2
Turbine Speed
45,000 RPM maximum (continuous operation) for
2 and 2.5-in. cups.
50,000 RPM maximum (continuous operation) for
1.5-in. cup.
Air Pressure
Bearing air pressure:
Minimum
4.8 bar (70 psi)
Recommended
5.5
−
7 bar (80
−
100 psi)
Brake air pressure:
Plant supply pressure
Air Consumption
Bearing air:
70 l/min at 5.5 bar
(2.5 scfm at 80 psi)
Turbine air (unloaded):
283 l/min (10 scfm) at
40,000 rpm
Vector air
254 l/min at 2.7 bar
(9 scfm at 40 psi)
510 l/min at 5.5 bar
(18 scfm at 80 psi)
Air Quality
Clean and dry, with 99% of 0.1 micron contaminants
removed.
Spray Pattern Size
203
−
609 mm (8
−
42 in.)
NOTE:
Pattern size is dependent on fluid pressure,
turbine speed, material viscosity, and many other
variables.
Electrostatic Voltage
Internal Power Supply (IPS):
100 kV maximum
EPS6 and IFC-100 cable:
60 kV maximum