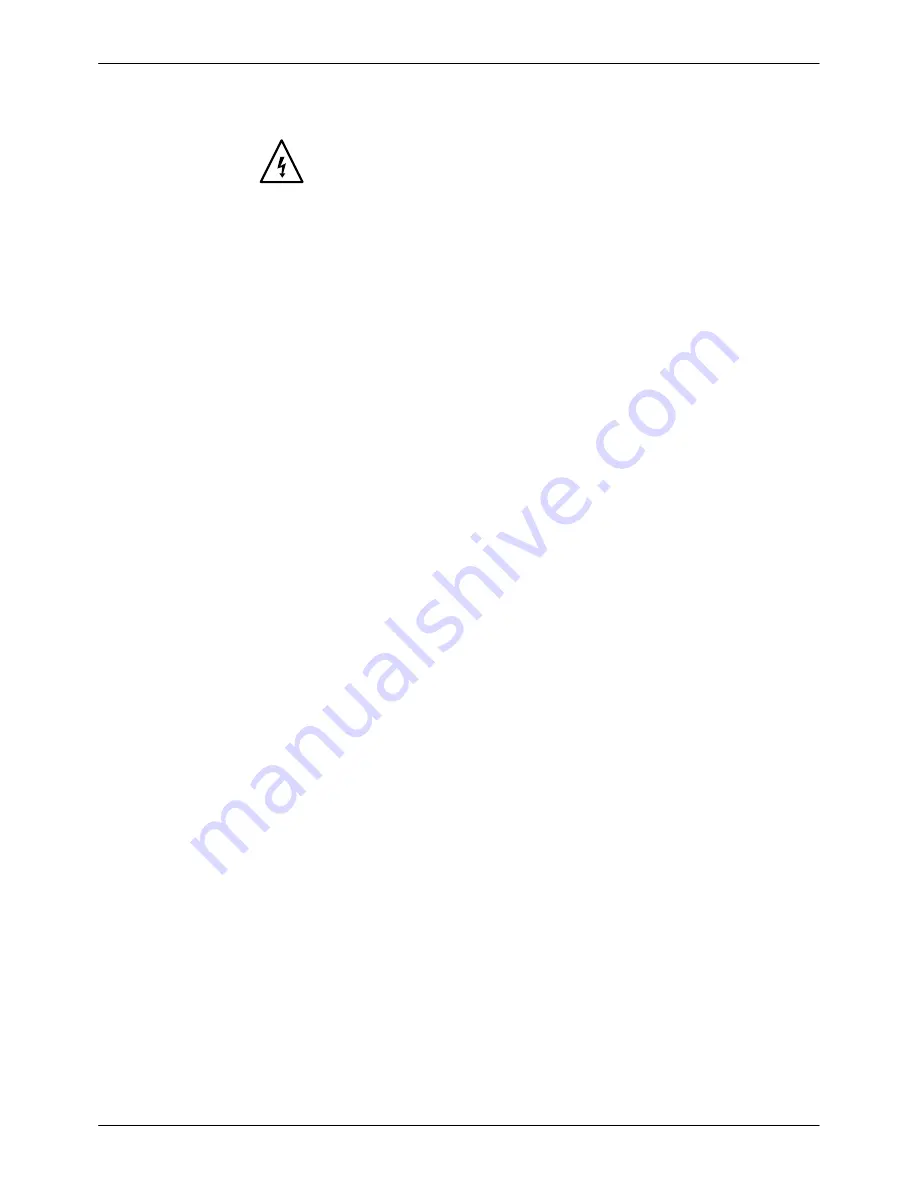
Waste Big Bag
3
Part
7093466
E
2021
Nordson Corporation
Grounding
WARNING:
Operating faulty electrostatic equipment is hazardous and can
cause electrocution, fire, or explosion. Make resistance checks part of your
periodic maintenance program. If you receive even a slight electrical shock
or notice static sparking or arcing, shut down all electrical or electrostatic
equipment immediately. Do not restart the equipment until the problem has
been identified and corrected.
Grounding inside and around the booth openings must comply with
EN50050
−
2, EN50177, EN16985, latest conditions. See Installation section
−
page 6
−
for enclosure grounding points.
S
All electrically conductive objects in the spray areas shall be electrically
connected to ground with a resistance of not more than 1 ohm when
measured with an appropriate instrument.
S
Equipment to be grounded includes, but is not limited to, the floor of the
spray area, operator working area platforms, hoppers, photoeye
supports, and blow-off nozzles. Personnel working in the spray area
must be grounded.
S
There is a possible ignition potential from the charged human body.
Personnel standing on a painted surface, such as an operator platform,
or wearing non-conductive shoes, are not grounded. Personnel must
wear shoes with conductive soles or use a ground strap to maintain a
connection to ground when working with or around electrostatic
equipment.
S
After servicing equipment, reconnect all disconnected equipment,
ground cables and wires.
Action in the Event of a Malfunction
If a system or any equipment in a system malfunctions, shut off the system
immediately and perform the following steps:
S
Disconnect and lock out electrical power. Close pneumatic shutoff
valves and relieve pressures.
S
Identify the reason for the malfunction and correct it before restarting the
equipment.
Disposal
Dispose of equipment and materials used in operation and servicing
according to local codes.