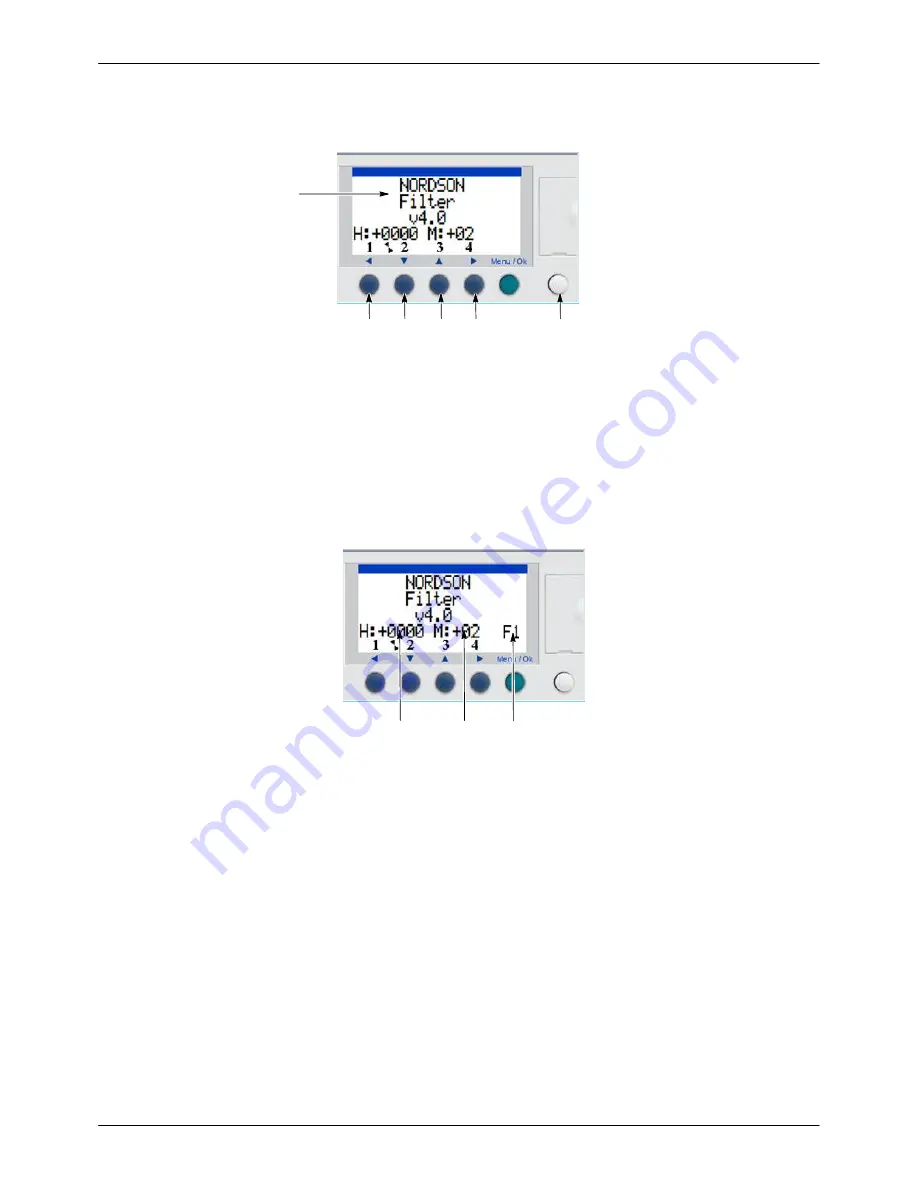
EcoMax
8
Part
7593428_01
E
2019 Nordson Corporation
Control Screen
16
17
19
20
21
18
Figure 3
Control Screen Button Identification
16. Display screen
17. Scroll LEFT
18. Scroll DOWN
19. Scroll UP
20. Scroll RIGHT
21. Button not used
Control Screen
−
Operation
22
24
23
Figure 4
Control Screen Display Identification
22. Working hours
23. Working minutes
24. Current filter being cleaned
Filter currently being cleaned (for example F1) appears on the screen.
The working hours counter is running when the programme is in operation mode and the machine is turned
on. When the counter reaches 60 minutes, it will increase the counter of working hours by 1, the minute
counter resets to 0. The counter of operating hours has a maximum of 9999 hours, then it resets to 0.
When the system is turned on, the controller always starts in the operating mode. You can adjust the time
delay (PAUSE TIME) between filter cleaning pulses and the duration (PULSE TIME) of the pulse.