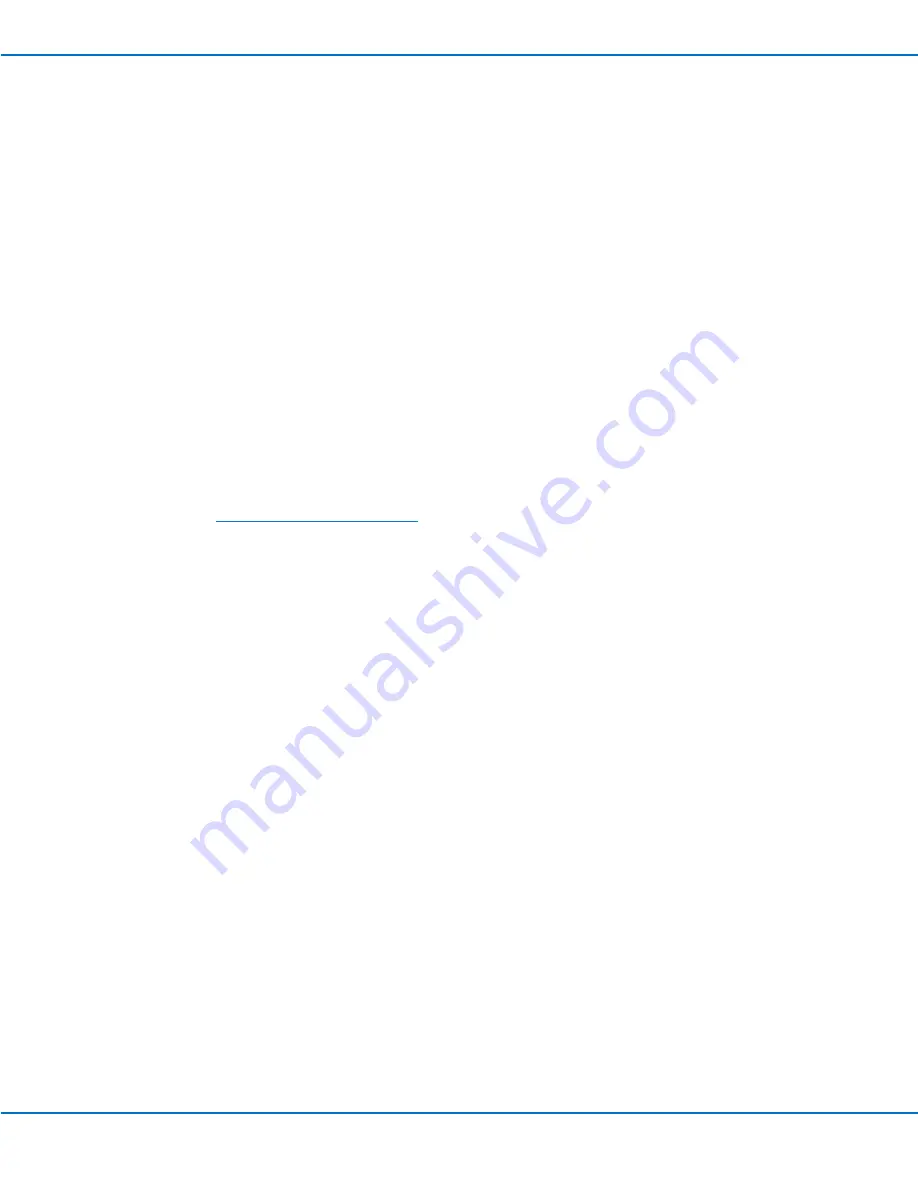
ProcessMate 6500 Temperature Control Unit
2
www.nordsonefd.com [email protected]
+1-401-431-7000 Sales and service of Nordson EFD dispensing systems are available worldwide.
Welcome to the ProcessMate
™
Temperature Control Unit, the most efficient process environmental
control system on the market.
This manual will help you maximize the usefulness of your new ProcessMate.
Please spend a few minutes to become familiar with the controls and features. Follow our recommended
testing procedures. Review the helpful information we have included, which is based on more than
50 years of industrial dispensing experience.
Most questions you will have are answered in this manual. However, if you need assistance, please do
not hesitate to contact EFD or your authorized EFD distributor. Detailed contact information is provided
on the last page of this document.
The Nordson EFD Pledge
Thank You!
You have just purchased the world’s finest precision dispensing equipment.
I want you to know that all of us at Nordson EFD value your business and will do everything in our power
to make you a satisfied customer.
If at any time you are not fully satisfied with our equipment or the support provided by your Nordson
EFD Product Application Specialist, please contact me personally at 800.556.3484 (US), 401.431.7000
(outside US), or
.
I guarantee that we will resolve any problems to your satisfaction.
Thanks again for choosing Nordson EFD.
Tara Tareso, General Manager
Tara