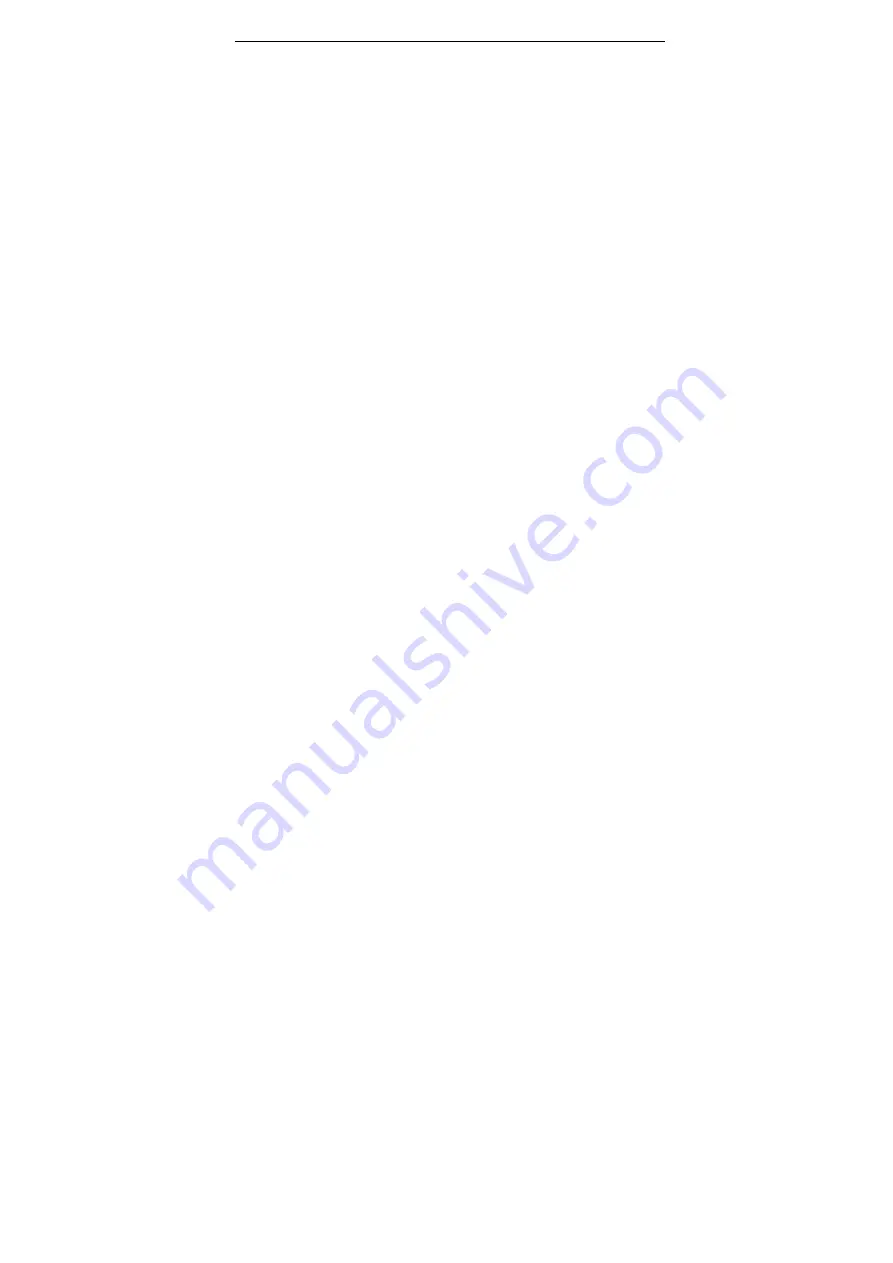
2.8.5 N-method Installation
This method is rarely used.
2.9 Installation Checkup
After completion of the transducer installation, the user should check the following items: the
receiving signal strength, the signal quality Q value, the delta time (traveling time difference
between the upstream and the downstream signals), the estimated liquid sound speed, the
transit time ratio, etc. As such, one can be sure that the flowmeter is working properly and the
results are reliable and accurate.
2.9.1 Signal Strength
Signal strength indicates the amplitude of receiving ultrasonic signals by a 3-digit number.
[000] means there is no signal detected and [999] refers to the maximum signal strength that
can be received.
Although the instrument works well when the signal strength ranges from 500 to 999, stronger
signal strength should be pursued, because a stronger signal means a better result. The
following methods are recommended to obtain strong signals:
(1) If the current location is not good enough for a stable and reliable flow reading, or if the
signal strength is lower than 700, relocate to a more favorable location.
(2) Try to polish the outer surface of the pipe, and apply more couplant to increase the signal
strength.
(3) Tenderly adjust the position of the two transducers, both vertically and horizontally, while
checking the signal strength. Stop at the position where the signal strength reaches to
maximum. Then, check the transducer spacing to make sure it is the same as or very close
to what window M25 shows.
2.9.2 Signal Quality
Signal quality is indicated as the Q value in the instrument. A higher Q value would mean a
higher Signal to Noise Ratio (short for SNR), and accordingly a higher degree of accuracy
able to be achieved. Under normal pipe condition, the Q value is in the range of 60-99, the
higher the better.
Causes for a lower Q value could be:
(1)
Interference from other instruments and devices nearby, such as a power frequency
transverter which could cause strong interference. Try to relocate the flowmeter to a
new place where the interference can be reduced.
(2)
Bad sonic coupling between the transducers and the pipe. Try to polish the pipe surface
again, clean the surface and apply more couplant, etc.
(3)
The selected pipe section is difficult to conduct the measurement. Relocate to a more
favorable pipe line.
21