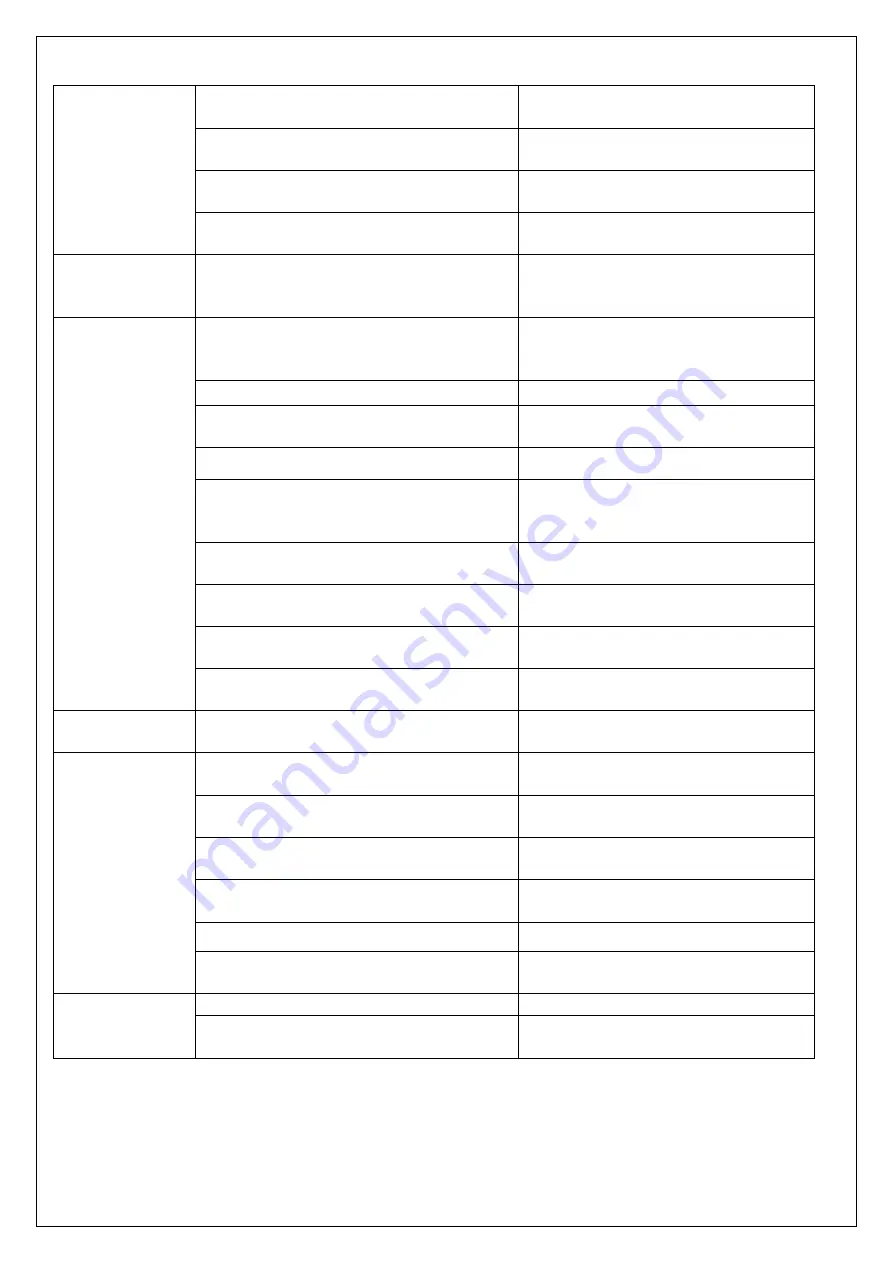
24
Oil leakage
Repair the hoses and/or the
sealing of the cylinder
Lifting stops at
71”
Move the protective arms into the
downside position
Lifting stops at
71”
Check the sensor for the protective
arm
Height sensor for 71” height defect
Check the height sensor on the
mast
Oil leakage
from air
breathing
Excessive quantity of oil. Reduce
oil
quantity.
Stacker not
starts operating
Battery is charging
Charge the battery completely and
then remove the main power plug
form the electrical socket.
Battery not connected
Connect the battery correctly
The fuse is faulty
Check and eventually replace
fuses
Battery discharged
Charge the battery
Combined emergency switch is
activated
De-activate the combined
emergency switch by insert and
pull the knob.
Tiller in the operating zone
Move the tiller firstly to the braking
zone.
Protective arms in the upright position,
platform folded upright
Move the protective arms into the
downside position
Foldable platform or protective arms in
one of the allowed positions
Check the proximate sensors for
the arms and platform
Foldable platform or protective arms
not in one of the allowed positions
Check the correct function of the
arms and/or platform
Only travelling
in one direction
The accelerator and the connections
are damaged.
Check the accelerator and the
connections.
The stacker
only travels
very slowly
The battery is discharged.
Check the battery status at the
discharge indicator
The electromagnetic brake is
engaged.
Check the electromagnetic brake
The relating tiller cables are
disconnected or damaged
Check the tiller cables and
connections.
Defective height sensor for reduced
speed at
12” height
Check the sensor
Electric system overheated
Stop using and cool down the truck
Defective heat sensor
Check and if necessary replace the
heat sensor
The stacker
starts up
suddenly
The controller is damaged.
Replace the controller.
The accelerator not moves back to its
neutral position.
Repair or replace the accelerator.
If the truck has malfunctions and can’t be operated out of the working zone, jack the truck up and go with
a load handler under the truck and safe the truck securely. Then move the truck out of the aisle.