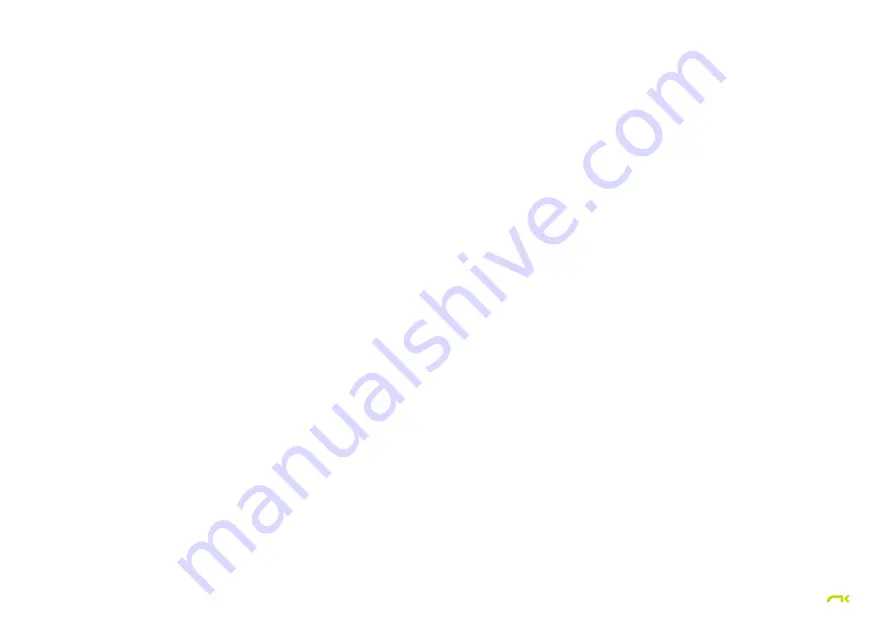
5
corrective decisions even in strong thermal conditions.
When pushed out, the speedbar is an efficient implement for a smooth,
stable and yet strong acceleration throughout the whole travel range and
hence producing an excellent sink rate as a result. The glider turns more
precisely and effortlessly. Having it all under control you can then, make
better decisions to truly enjoy the flight.
1.4 ASSEMBLY, MATERIALS
The ARTIK 4 has all the technological innovations as used on other
Niviuk gliders. Furthermore it is full of small details destined to enhance
the pilots’ comfort and to improve the performance of the SLE, RAM,
DRS and 3 liner.
SLE.- The SLE allows reinforcement of the leading edge preventing any
deformation during turbulence. The airflow is also vastly improved over
the entire front span of the glider.
RAM.- The RAM air intake allows for optimal air intakes positioning
(below the glider’s leading edge aligned with the intrados), turbulent air
buffering at the front of the wing, bringing more consistency in variable
speeds, and increasing performance while assuring maximum safety.
DRS.-The trailing edge has been reinforced with small ribs that make
thispart flatter in order to spread the pressure out evenly. It means
better air-flow and less drag on this important part of the glider. The
addition of theseribs gives exceptional handling (better and more efficient
whenturning) and more control and precision.
3LT.- Its powerful profile, a detailed internal architecture structure and the
useof high-tech strength materials make possible a significant reduction
of thetotal length of suspension lines in order to reduce the parasite
resistance andthe weight of the glider to gain efficiency.
A whooping 8,77% in weight reduction demonstrates the effort and
accomplishment made to reduce the glider inner bulk and profile
resulting, more performance, enhanced safety and comfort.
The ARTIK 4 lines are made of Dyneema Liros for the upper cascades
and Vectram Cousin for main and middle cascades. This is the same
material combination found in top gliders.
Both Dyneema and Vectram are unsheathed lines, which are slightly
more exposed to normal wear and tear. It is strongly recommended for
all the lines to be thoroughly inspected every 100 hours of flight. Keep
in mind that we are using materials with great performance of a rigorous
check before each flight.
Not a single millimetre of error is possible in the manufacturing process
from Olivier’s computer to the cutting of the fabric. An automatic process
controlled by a laser-cutting program cuts each of the sections that
compose the different parts of the wing. This program not only cuts the
pieces of fabric but it also paints the guideline marks that will aid the
assembly; it also numbers the separate pieces of material. All this is
carried out before human handling of the pieces begins. So we eliminate
possible and understandable errors that may occur during this delicate
procedure.
The lines are semi-automatically manufactured and all the sewing is
finished under the supervision of our specialists. The jigsaw puzzle of the
assembly process is made easier using this method. We minimize the
processes while making the quality control more efficient. All the different
parts of the canopy are cut and assembled under the strict conditions
induced by the automation of the whole process.
It is strongly recommended that all lines are thoroughly checked by the
pilot prior to every flight and ultimately checked by a service centre or
Niviuk dealer after every 100 hours of flight. We should not forget that we
are using materials with great performance but that they need a rigorous