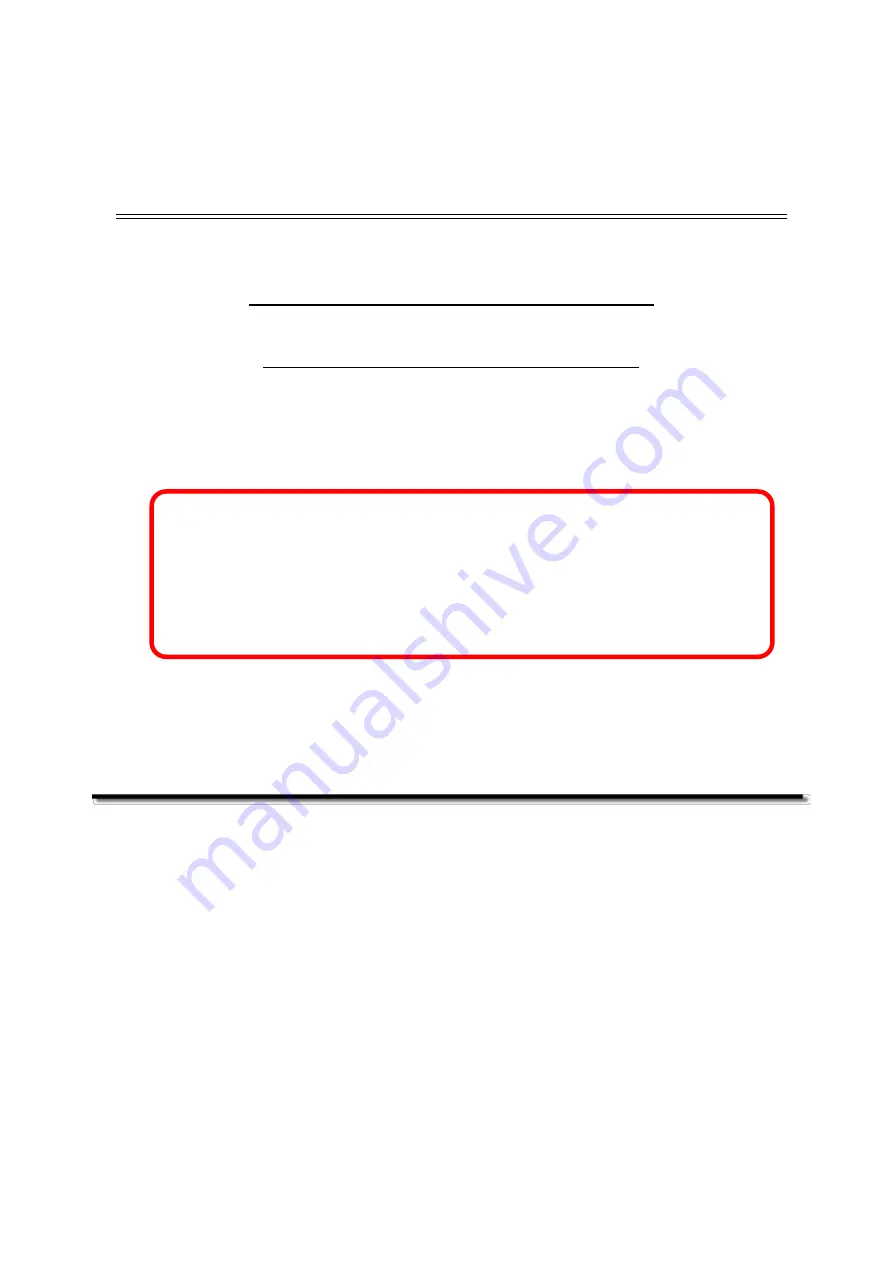
INSTRUCTION MANUAL
Automatic Tool Changer
NITTAOMEGA type L
Nitta Corporation
Osaka HQ:
4-4-26 Sakuragawa, Naniwa-ku, Osaka, Osaka 556-0022
Tel: +81 6-6563-1273
FAX: +81 6-6563-1274
Tokyo Branch: 8-2-1 Ginza, Chuo-Ku, Tokyo 104-0061
Tel: +81-3-6744-2708
FAX: +81-3-6744-2709
Nagoya Branch: 1-17-23 Meieki-Minami, Nakamura-ku, Nagoya 450-0003
Tel: +81-52-589-1310
FAX: +81-52-586-5707
Nabari Plant:
1300-45 Yabata, Nabari, Mie 518-0494
Tel: +81-595-64-2916
FAX: +81 595-63-9527
Issued: April 2021
Revised:
Ver. No.: rev.0
Printed in Japan
type L-ENOUG-00
NOTICE
For use of this document:
Please keep this document always readily available to those who use
the product. If you need an additional copy, please download the
document from our website: http: //www.nitta.co.jp/
Summary of Contents for NITTAOMEGA L
Page 28: ...4 Part Names 20 4 Part Names Fig 3 Part names ...
Page 53: ......