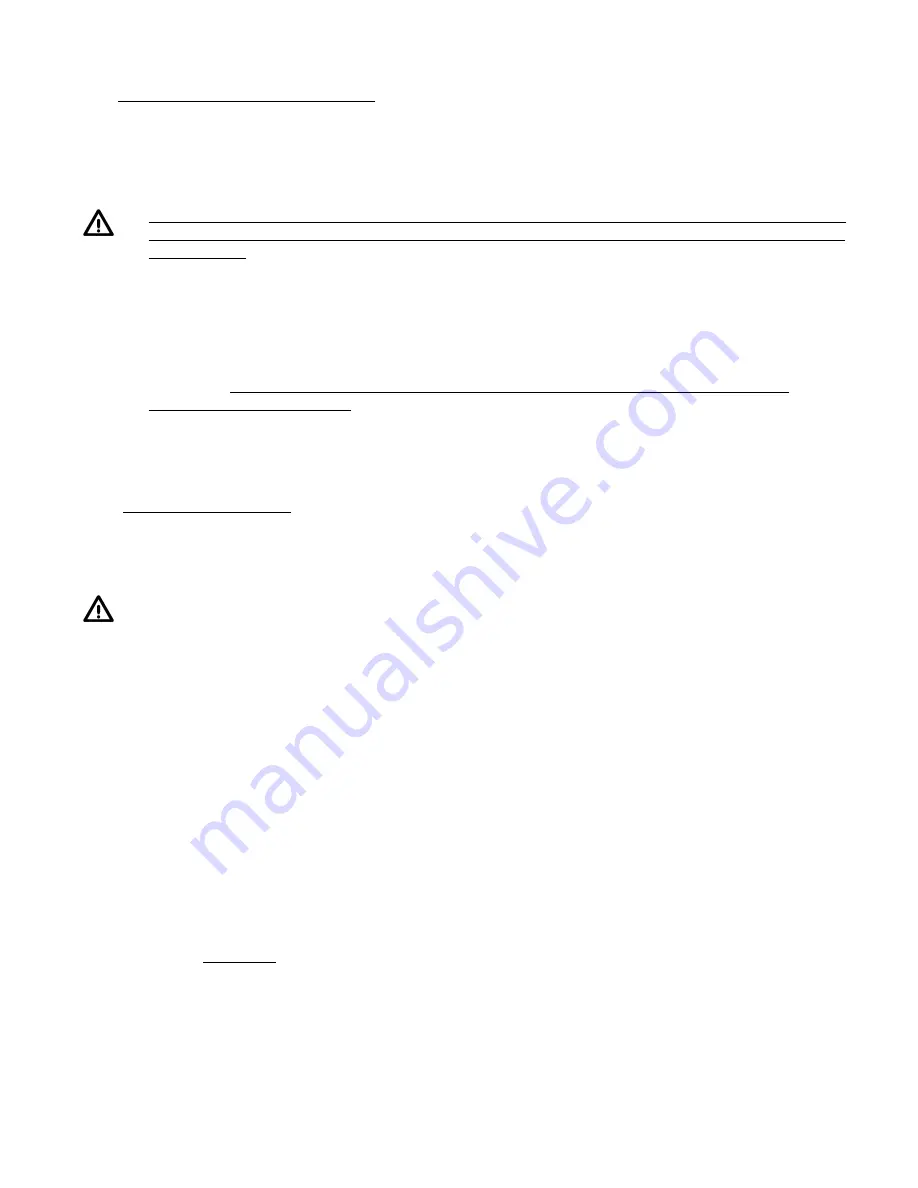
II. Machine Preparation (continued)
B.
Filling the Propane Fuel Cylinder
Nilfisk-Advance uses the 20 lb. capacity aluminum fuel cylinder which meets the D.O.T. 4E240
standards. These cylinders are also listed by U.L.. Filling should ONLY be done by a qualified propane
dealer. A properly filled cylinder should not exceed 80% of the rated capacity.
DO NOT attempt cylinder repair. Return the cylinder to your propane dealer if repair is necessary.
Please note that D.O.T. regulations prohibit shipping of cylinders after the cylinder has been filled
with propane.
C.
Installing the Fuel Cylinder
Strap the cylinder in place by clamping the toggle assembly to the cylinder band. Adjust the toggle
assembly by screwing in or out in order to keep the tank firmly secured. Connect the fuel hose coupling
to the service valve by turning right (clockwise).
HAND TIGHTEN ONLY.
Make sure coupling is not
cross threaded and check for leakage by noting any odors of propane immediately after cylinder is
connected. (It is sometimes easier to install if the connection to the service valve is made before
strapping the cylinder in place.
To remove cylinder, reverse above procedure. Always connect or change cylinders in a well ventilated
area.
III. Operating Instruction
A.
Starting Instructions
1.Check oil and fuel levels.
2.Check and clean engine air filter.
NEVER RUN CONTINUOUSLY FOR MORE THAN 1 HOUR WITHOUT CLEANING OR
CHANGING ENGINE DUST FILTER.
(See Scheduled Maintenance)
3.
Check carburetor air filter. Change if necessary.
(See Scheduled Maintenance).
4.Turn propane service valve on the fuel cylinder counter-clockwise to open.
5.Allow machine to tilt backward (pad off floor) and move the throttle to the
SLOW
position.
6.Plug electric cord into 110 volt wall receptacle and onto starter switch.
7.Engage starter by pushing the button on starter switch.
Note:
Do not engage starter for more than 10 seconds. Allow a 60 second cool down period for
each 10 second start-up cycle. If the starter overheats an internal overload switch will prevent it
from operating until cooled. Wait 15 or 20 minutes before trying again.
8.After engine starts, adjust the throttle to the proper speed.
B.
Operation
1.After engine has started, allow approximately 30 seconds for the engine to "warm up" then
advance the throttle to operating speed.
2.Lower the burnishing head to the floor while moving the machine forward.
CAUTION!
! Do not run the machine without moving. If allowed to run in one spot damage to the
floor may occur.
3.To stop burnishing, push down on handle raising the burnishing head off the floor.
2
WARNING
WARNING