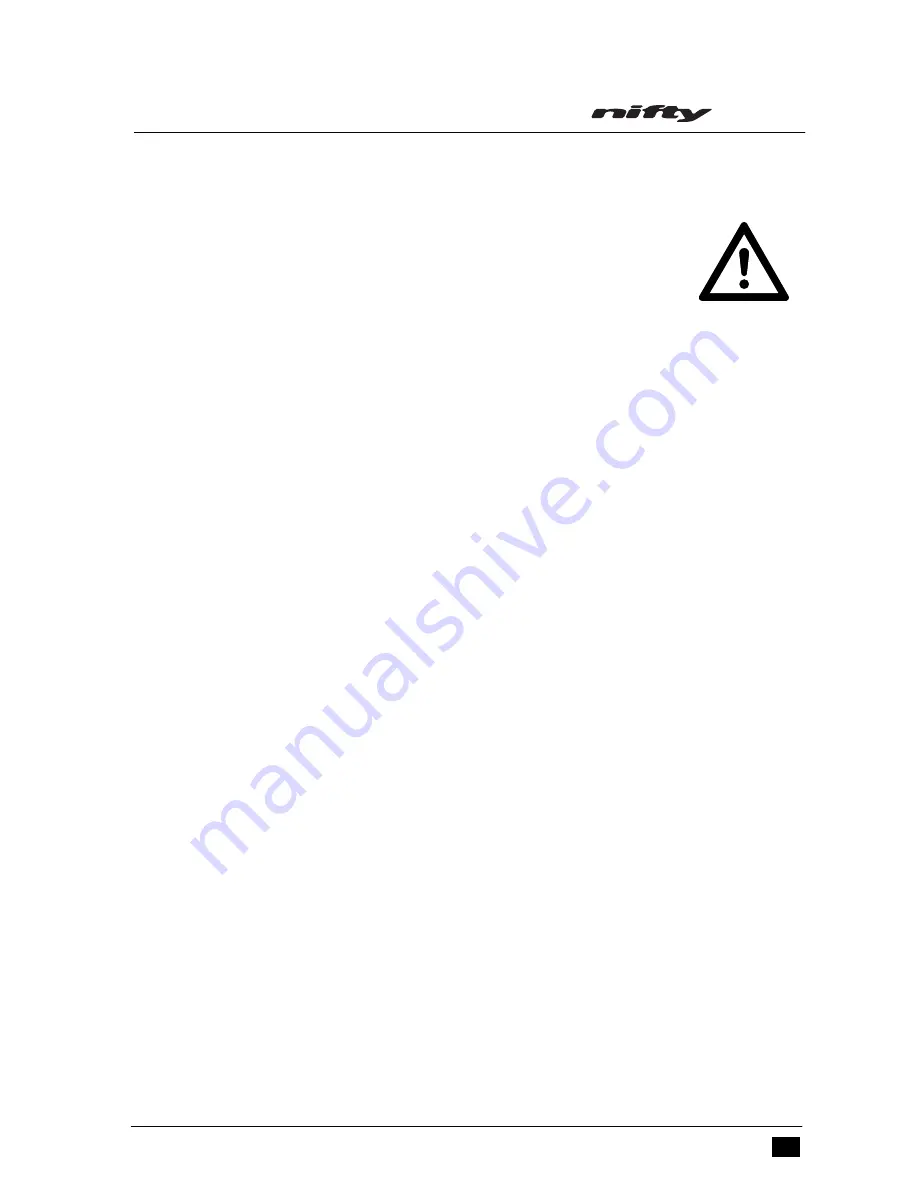
SD Series
Operating & Safety Instructions
English/USA 09/03
25
4.3
GROUND CONTROL OPERATION
ALWAYS ALLOW THE ENGINE TO WARM UP BEFORE OPERATING.
4.3.1
GROUND CONTROL INSTRUCTIONS
ALL MODELS
1)
Ensure all red emergency stops are out.
2)
Turn key switch at ground control station to ground (i.e. fully down).
3)
Ensure selector hand valve (if applicable) is turned to platform position (i.e. fully up).
4)
Battery electric models go to step 11.
DIESEL ENGINE OR BI-ENERGY MODELS
5)
For a cold engine start, go to step 6) or for a warm engine go to step 7).
6)
COLD ENGINE:
- turn the main engine ignition switch (located beneath the front cover)
through “ON” to “GL”. This engages the glow plug pre-heat system. Hold for 3-5 seconds
then turn key fully to “ST” (start) position and the engine will fire.
7)
WARM ENGINE:
- turn the main engine ignition switch (located beneath the front cover)
through “ON” to “ST” (start) position and the engine will fire.
Note – Unless the diesel engine is running, the 170SD will automatically default to the primary
power source (usually battery)
PETROL (GASOLINE) ENGINE OR PETROL (GASOLINE)/ELECTRIC MODELS
8)
For a cold engine start, go to step 9) or for a warm engine go to step 10).
9)
COLD ENGINE:
- turn the engine fuel tap on and engage the choke lever. Turn the main
engine ignition through “ON” to “ST” (Start) and the engine will fire. Return the choke lever
to its normal running position after the engine is started.
10)
WARM ENGINE:
- turn the engine fuel tap on and turn the main engine ignition through “ON”
to “ST” (start) position and the engine will fire.
Note – Unless the diesel engine is running, the 170SD will automatically default to the primary
power source (usually battery)
ALL MODELS
11) Push and hold green power button.
12) Select function and operate hand levers in full accordance with manufacturers Operating and
Safety manual. Note: all outriggers must be down before booms can be operated.
13) To return control to platform turn key fully clockwise to up position.
14) When not in use return machine to stowed position, fully raise and stow all outriggers, turn
the key to the centre off position, remove key and chock wheels.
Summary of Contents for 170SD series
Page 2: ......