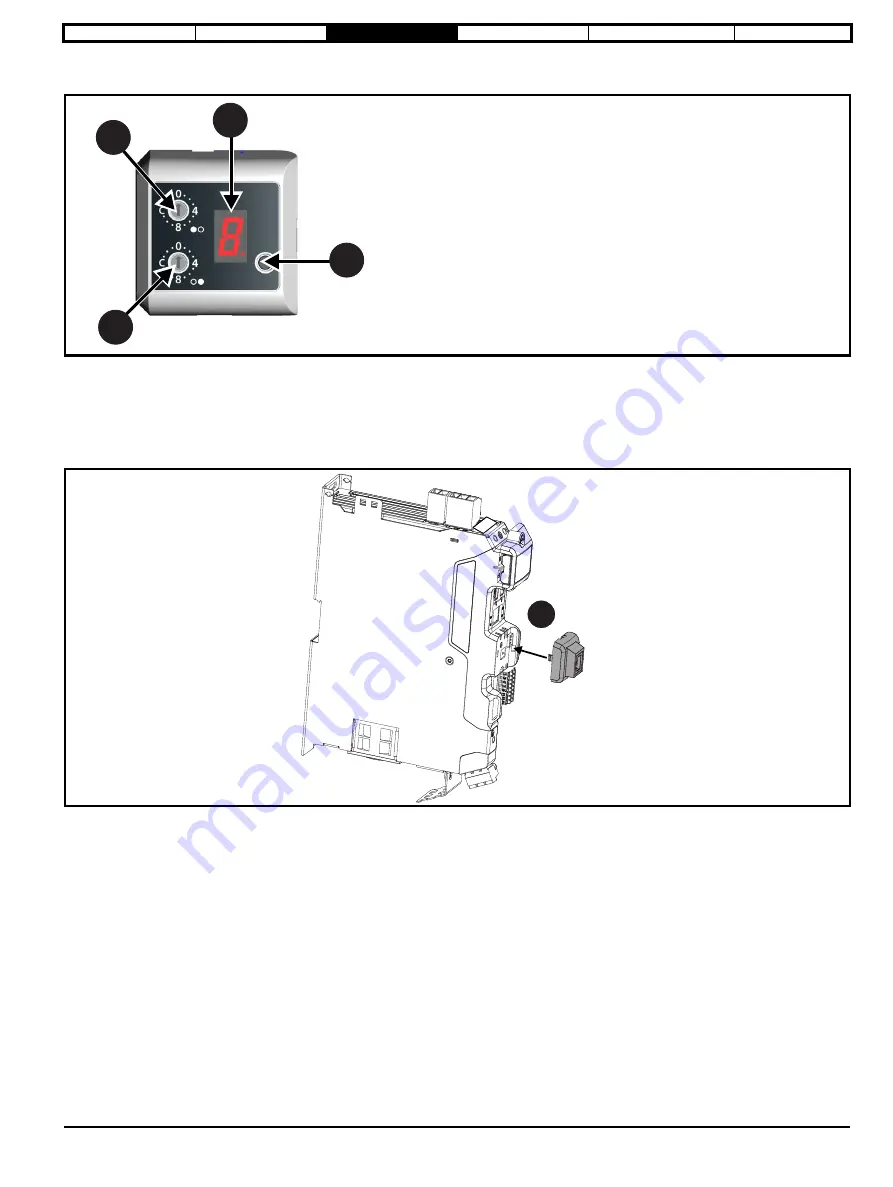
Digitax HD M75X Series Installation and Technical Guide
21
Issue Number: 5
3.4.1 Drive state representation
Figure 3-6 KI-Compact display
Refer to the relevant Digitax HD M75X Control User Guide for more information.
3.5 KI-Remote Keypad Adaptor installation
The Digitax HD M75X Remote Keypad Adaptor provides an EIA-485 port for permanent connection to a KI-Remote Keypad or the temporary
attachment for PC tool connection. The KI-Remote Keypad Adaptor is available from the supplier of the drive. Refer to section 2.8
Figure 3-7 Installing the KI-Remote Keypad Adaptor without display fitted
1.
Align the KI-Remote Keypad Adaptor to the display housing and push on until it clicks into place.
1
2
3
4
1
. Single Character display.
2
. Reset switch.
3
. Rotary dial for node address setting (least significant).
4
. Rotary dial for node address setting (Most significant).
1
Summary of Contents for Digitax HD M75 Series
Page 115: ......
Page 116: ...0478 0395 05...