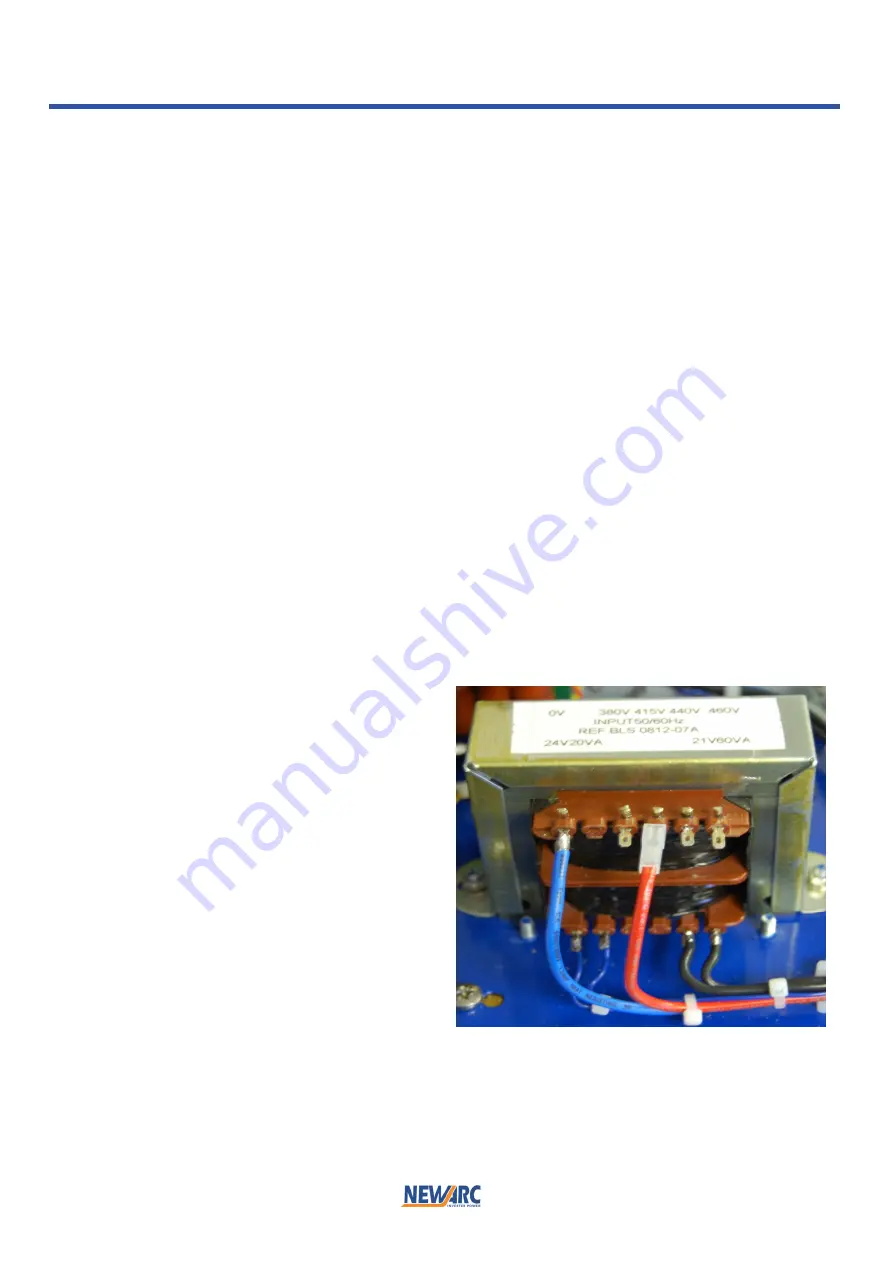
RT5/4000
6
SECTION 3 — INSTALLATION
3.1 Siting the RT4000/RT5000
•
Site the RT4000/RT5000 on a clean dry sur-
face, preferable above ground level.
•
Make sure there is at least 20cm clearance
at the front, rear and right side of the ma-
chine to allow good circulation of the cool-
ing air.
•
Protect the machine from heavy rain and if
used in hot climates, against direct sunlight.
•
Ensure that the machine is positioned in
such a way that particles created by grind-
ing and cutting operations do not enter the
machine.
Note! Damage caused by metal particles and
water entering the machine will not be cov-
ered under warranty.
3.2 Connecting to mains supply
WARNING! All electric shocks are potentially
fatal, a competent electrician should carry
out the fitting of the mains plug.
•
Make sure that the mains supply is of the
correct voltage and current capability for
the machine.
•
Make sure that any extension cables used
are of sufficient current carrying capacity.
•
Make sure that the mains plug and socket
(if fitted) are in good condition and are of
the correct current carrying capacity. If the
machine is wired directly to the mains sup-
ply then an isolator switch must be fitted.
Note! See the technical specifications page for
correct supply information
Primary cable length
Long cable lengths may reduce the perform-
ance of the machine, the welding arc may
become unstable, especially at higher cur-
rents. Ensure the mains cable is not coiled up
during welding as this will reduce the input
voltage to the machine and may cause over-
heating and degradation of the cable.
3.3 Setting supply voltage tapping
WARNING! All electric shocks are potentially fa-
tal, a competent electrician should carry out any
supply voltage tapping adjustments required.
•
To enable the setting of the supply voltage
tapping, the cover of the RT4000/RT5000 has
to be removed.
•
The photograph below shows the voltage tap-
ping set to 415V, with the red wire from the
fuse holder connected to the 415 terminal.
•
This connector can be moved to the required
voltage terminal to select the desired input
voltage.
Summary of Contents for RT4000
Page 2: ......
Page 11: ...RT5 4000 11 SECTION 6 ELECTRICAL DIAGRAMS 6 1 System Diagram ...
Page 15: ......