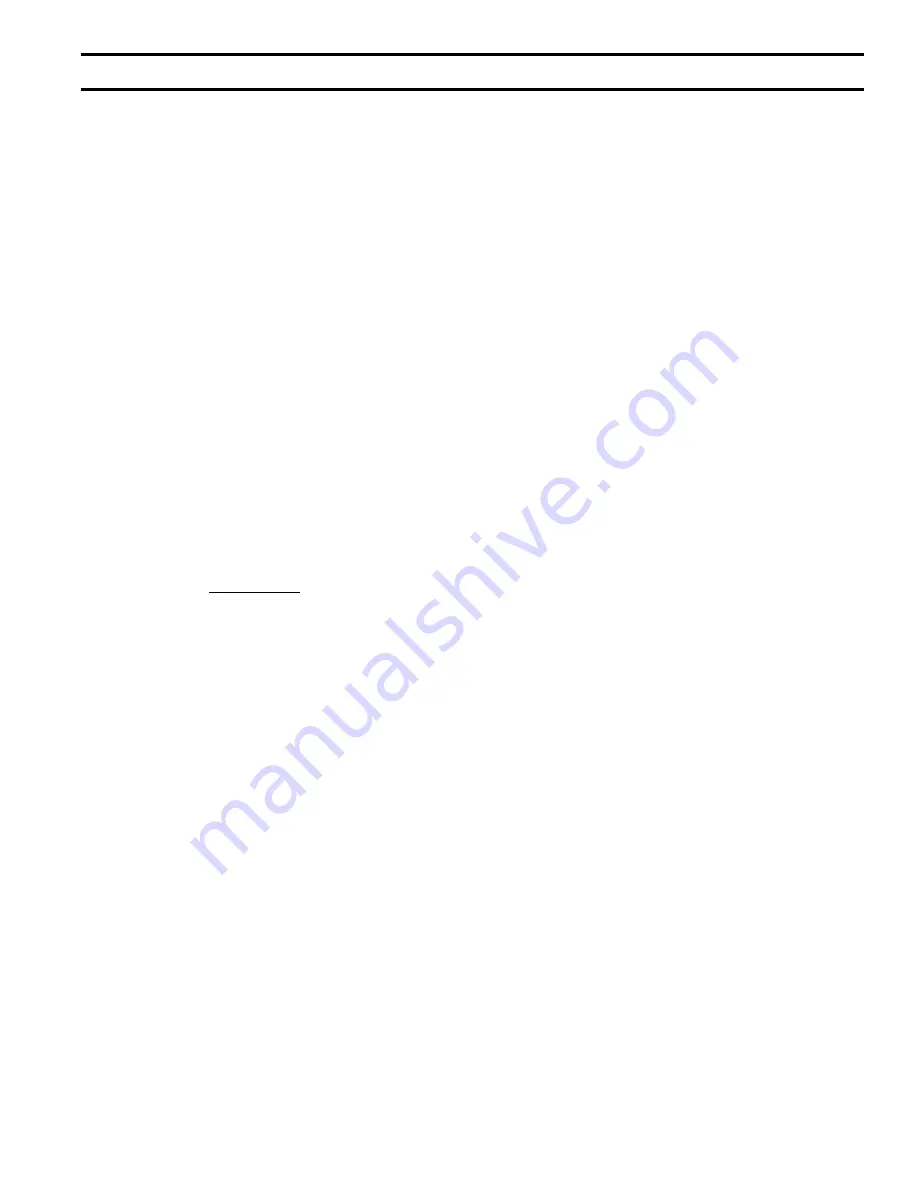
11
11
Vent installation must be in accordance with local building codes, or the local authority having jurisdiction, or the
National
Fuel Gas Code
, ANSI Z223.1/NFPA 54.
A typical vent installation is illustrated by Figure 8. The components of vent installation are the vent damper (if used), vent
connector and chimney.
1) Acceptable Chimneys - The following chimneys may be used to vent CGS-C series boilers:
•
Listed Type B or L gas vent - Install in accordance with the manufacturer’s instructions, the terms of its listing, and
applicable codes.
•
Masonry Chimney - The masonry chimney must be constructed in accordance with the
Standard for Chimneys,
Fireplaces, Vents, and Solid Fuel Burning Appliances
(NFPA 211) and lined with a clay liner or other listed lining
system. Do not vent a CGS-C series boiler into an unlined chimney.
2) Acceptable Vent Connectors - The following may be used for vent connectors:
•
Listed type B or L Gas Vent
•
Single Wall Galvanized Pipe - Use 0.018” (26 gauge or heavier). The size and location of the chimney may not
permit the use of a single wall connector in some cases. See the
National Fuel Gas Code
. Do not use single wall pipe
for vent connectors in attics.
•
Other Vent Connectors Permitted by the
National Fuel Gas Code
.
3) Chimney and Vent Connector Sizing - Size the chimney and vent connector in accordance with the
National Fuel Gas
Code.
4) Exterior Chimneys - An exterior chimney has one or more sides exposed to the outdoors below the roof line. There are
two conditions under which an exterior chimney may be used:
•
In some very restrictive cases, CGS-C series boilers may be vented into an exterior ceramic lined masonry chimney.
See the
National Fuel Gas Code
for information on when exterior chimneys may be used.
•
An exterior masonry chimney may be used if it is lined with B vent or a listed chimney lining system.
5) This boiler may be vented using a listed power venter. The power venter must be sized and installed in accordance with
the power venter manufacturer’s instructions, the terms of the power venter listing, and applicable codes. The boiler
must be electrically interlocked with the power venter to prevent boiler operation if the power venter fails to operate.
Before deciding to use a power venter, make certain that the flue gas exiting the power venter will not damage adjacent
construction or other structures. Also make certain that the power venter terminal will not be subjected to winds which
could effect power venter operation.
6) Do not connect the vent of this appliance into any portion of a mechanical vent system operating under positive pressure.
7) Do not connect the boiler into a chimney flue serving an open fireplace or other solid fuel appliance.
8) Prior to boiler installation, inspect chimney for obstructions or other defects and correct as required. Clean chimney as
necessary.
9) Vent pipe should slope upward from draft diverter not less than one inch in four feet. No portion of vent pipe should run
downward or have sags. Vent pipe must be securely supported.
10) The vertical section of vent pipe coming off the boiler should be as tall as possible, while still maintaining the proper
clearance from the horizontal vent connector to combustibles and the proper pitch called for in (9) above.
11) Vent pipe should be installed above the bottom of the chimney to prevent blockage.
12) Vent pipe must be inserted flush with inside face of the chimney liner and the space between vent pipe and chimney
sealed tight.
13) Do not install the vent damper in any portion of the vent system which is used by appliances other than the boiler being
installed.
VI. Venting
Summary of Contents for CGS-C Series
Page 24: ...24 FIGURE 17 WIRING DIAGRAM McDONNELL MILLER MODEL 67 LOW WATER CUTOFF X Electrical continued...
Page 27: ...27 27 FIGURE 19 OPERATING INSTRUCTIONS XI System Start up continued...
Page 35: ...35 35 XIII Troubleshooting continued...
Page 37: ...37 37 XIII Troubleshooting continued...
Page 39: ...39 39...
Page 41: ...41 41 XIV Repair Parts continued...
Page 43: ...43 43 XIV Repair Parts continued...
Page 45: ...45 45 XIV Repair Parts continued...
Page 47: ...47 47 XIV Repair Parts continued...
Page 49: ...49 49 XIV Repair Parts continued...
Page 51: ...51 51...
Page 52: ...52...