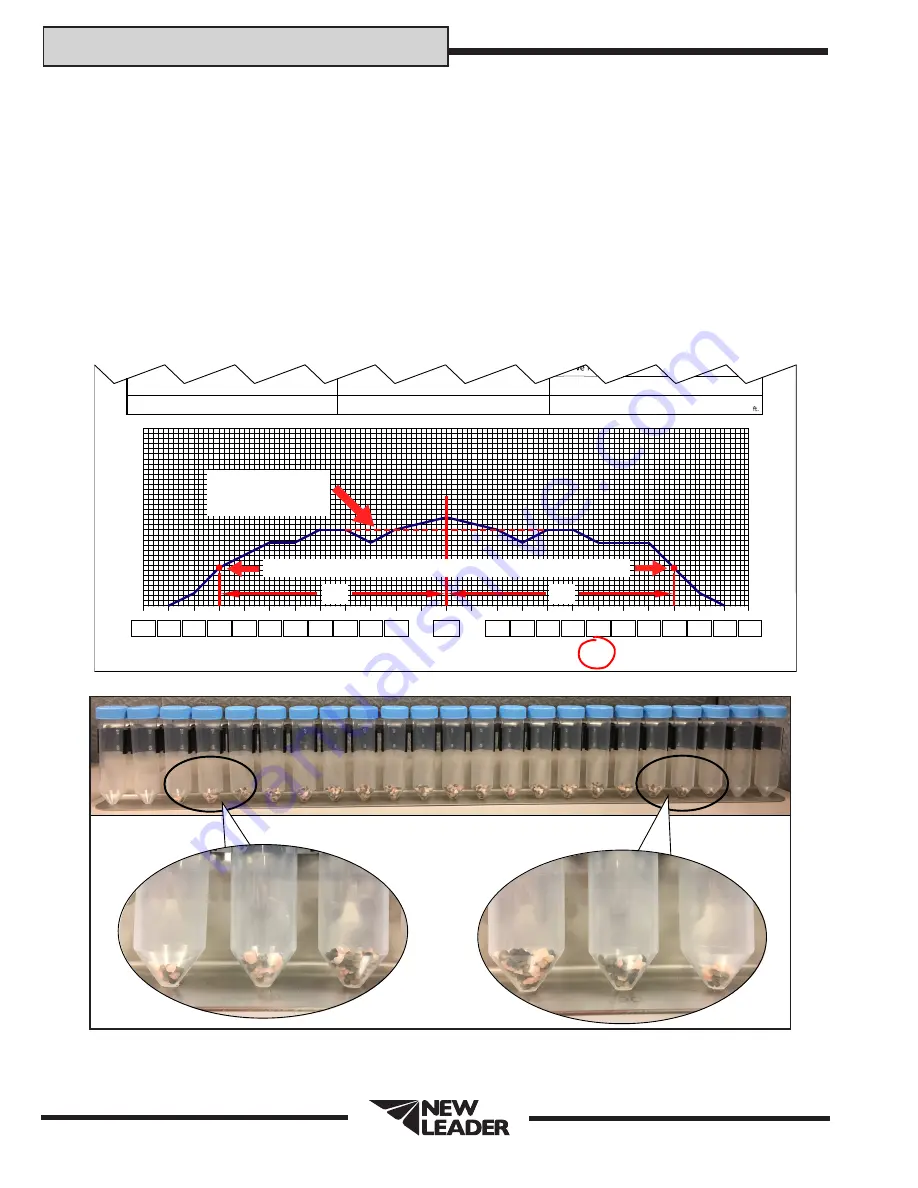
- 10 -
www.NewLeader.com
(800) 363-1771
313967-I
SPREAD PATTERN
Header
Spread Pattern
Determining Driving Centers
Once an acceptable pattern is obtained, as shown in Figure 5, driving centers can be determined. To
determine optimum driving centers (effective swath width), determine the average amount of material
in the center of the pattern. Figure 8 shows an example data sheet recorded from the profile shown in
Figure 9. Based on the example, the average amount of material in the center of the pattern is 3.0, as
indicated with the red dotted line.
Next, locate the points on both the left and right side of the pattern where the amount of material is
half the average amount at the center of the pattern. In the example shown in Figure 8, these points are
located 45’ to the left of center, and 45’ to the right of center. The distance between these two points
(90’) represents the driving centers to use.
NOTE: Once the effective swath width has been established, a change in the controller may be required.
313964-A
Temperature:
°F
lbs/acre
Spinner Speed:
RPM
Controller Vehicle Speed:
MPH
Controller Swath Width:
10’
15’
20’
25’
30’
35’
40’
45’
50’
55’
-0-
10’
15’
20’
25’
30’
35’
40’
45’
50’
55’
1
2
3
4
5
6
7
1
2
3
4
5
6
7
60’
60’
3.5
3.0
3.0
3.03.0
3.0
3.0
2.5
2.5
2.5 2.5 2.5 1.50.5
2.5 2.5
2.0
1.5
0.5
ACCEPTABLE PATTERN
Average amount of
material in the center
of the pattern = 3
EFFECTIVE SWATH WIDTH: 45’+ 45’ = 90’
45’
45’
Points where material is half of the center of the pattern = 1.5
Figure 8 - Effective Swath Width
Figure 9
80’
80’
90’
90’
100’
100’