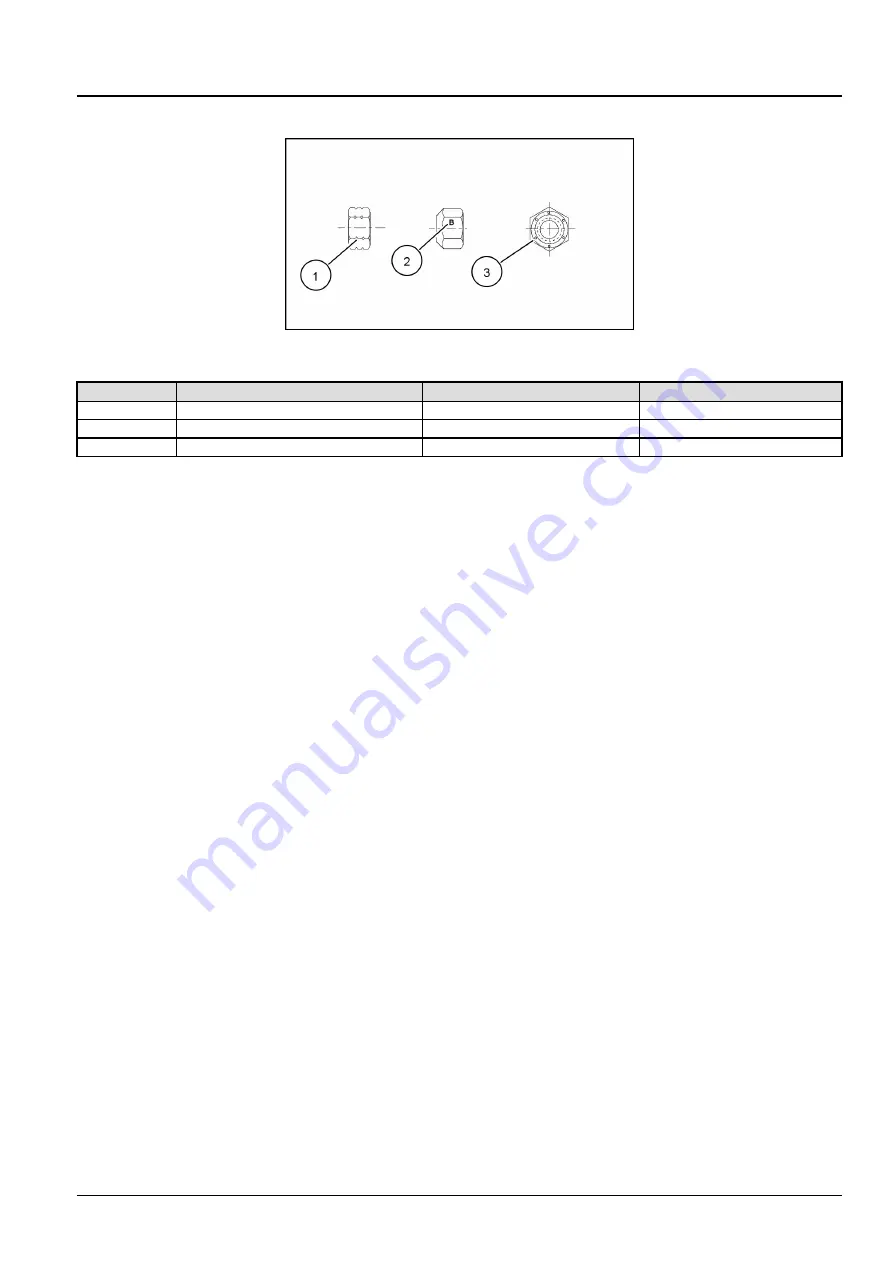
INTRODUCTION
Inch Lock Nuts, All Metal (Three optional methods)
20090268
4
Grade Identification
Grade
Corner Marking Method (1)
Flats Marking Method (2)
Clock Marking Method (3)
Grade A
No Notches
No Mark
No Marks
Grade B
One Circumferential Notch
Letter B
Three Marks
Grade C
Two Circumferential Notches
Letter C
Six Marks
84547569 01/12/2011
19