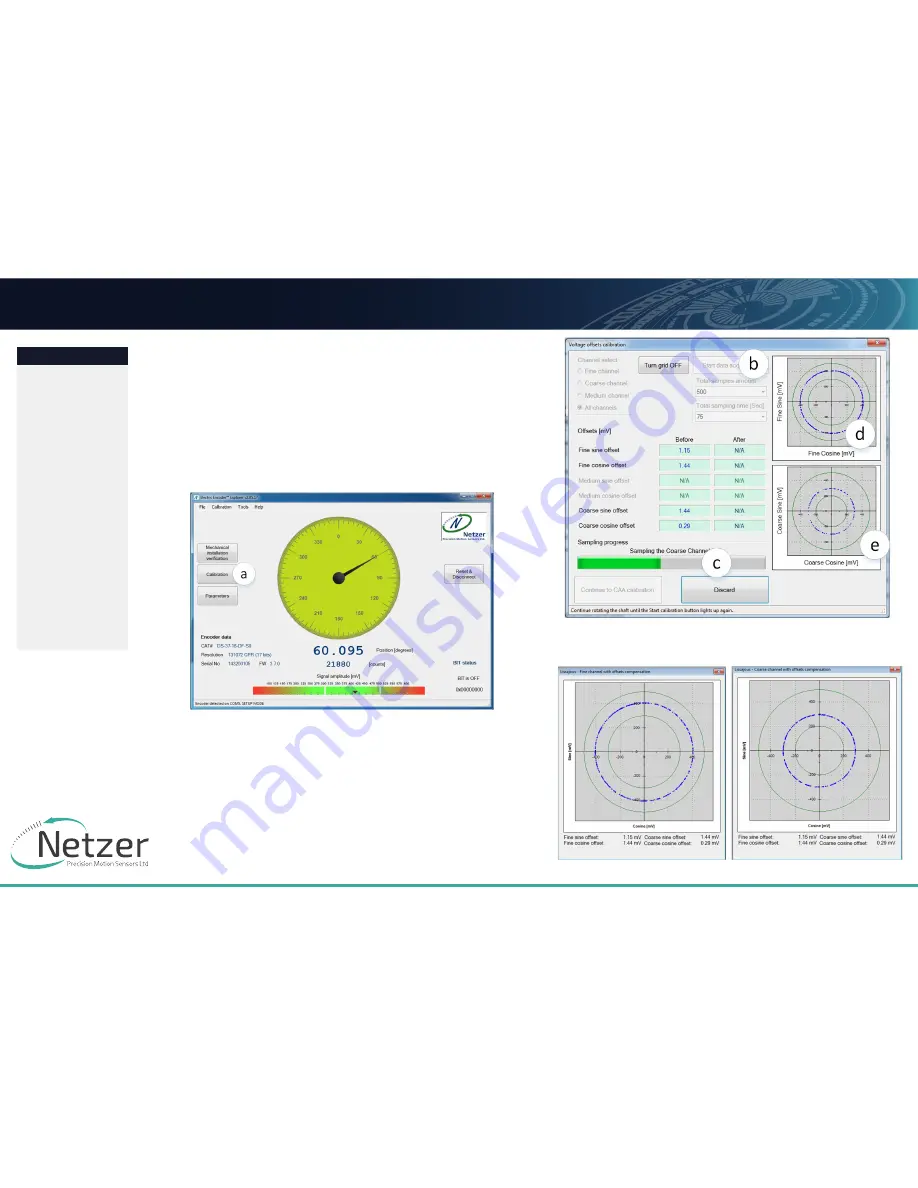
U
ser
M
anUal
Page 13 of 16
DF-150 User Manual | Rev 1.0
Netzer Precision Motion Sensors LTD Propriety
Preface
Safety
Product Overview
Unpacking
Electrical
Connection
Software
Installation
Mounting
Verification
Calibration
Mechanical ICD
Mounting options
JUNE 2016
All specifications are subject to change without notice
Contents
DF-150 Rotary Electric Encoder
8.
CALIBRATION
8.1 o
ffseT
C
alibraTion
For optimal performance of the DF-150 Electric Encoder, the
inevitable DC offset of the sine and cosine signals must be
compensated over the operational sector.
After successfully completing the Mounting Verification
procedure:
(
a)
Select [Calibration] on the main screen.
(
b
) Start the data acquisition while rotating the shaft.
The progress bar
(c
) indicates the collection progress.
Rotate the axis consistently during data collection—covering
the working sector of the application end to end—by default
the procedure collects 500 points over 75 seconds. Rotation
speed is not a parameter during data collection. Data collection
indication shows for the fine/coarse channels, a clear “thin”
circle appears in the center (
d
) (
e
) with some offset.
Offset compensated Fine / Corse Channel